Did you know that CNC machining can process a wider variety of materials than many other manufacturing processes? From metals to plastics and composites, the possibilities are virtually limitless. In fact, the ability to precisely cut, shape, and assemble materials is what has made CNC machining the backbone of modern manufacturing. But just how diverse is the range of materials that can be manipulated through CNC technology? In this blog, we will delve into this question, explore how CNC machining can be applied across different types of materials, and uncover the implications for industries utilizing this fantastic technology.
Understanding CNC Machining
What is CNC Machining?
CNC, or Computer Numerical Control, machining is a process that utilizes programmed computer software to control the movement of factory tools and machinery. It allows for the automation of complex tasks such as drilling, milling, and turning by converting a digital design into a physical object.
The Evolution of CNC Technology
Since its inception in the 1940s and 50s, CNC technology has transformed vastly. Initially, it was primarily used for metals. However, advancements have led to significant innovations, allowing CNC machining to accommodate various materials efficiently.
The Range of Materials Processed by CNC Machining
1.1 Aluminum
Aluminum is one of the most commonly machined metals due to its lightweight and corrosion-resistant properties. It is extensively used in aerospace and automotive industries.
CNC Techniques: CNC milling and turning are frequently employed to create complex shapes, ensuring tight tolerances.
1.2 Steel
Steel is a versatile and widely used material in manufacturing, known for its strength and hardness.
CNC Techniques: Steel machining often involves substantial tooling capabilities. Techniques like CNC laser cutting help achieve precision and can handle hard steels like 4140 and
Titanium’s exceptional strength-to-weight ratio makes it an attractive option for critical applications, particularly in aerospace and biomedical sectors.
CNC Techniques: Advanced machining techniques are required for titanium due to its hardness and tendency to produce excessive heat.
1.4 Brass and Copper
These metals offer excellent machinability and are often used in electronic components and decorative items.
CNC Techniques: CNC lathes and milling machines yield high-quality finishes for brass and copper pieces.
CNC machining isn’t limited to metals; many plastics can also be processed with outstanding efficiency.
2.1 Acrylic
Known for its clarity and versatility, acrylic is often used for displays and signage.
CNC Techniques: CNC routing is frequently employed for cutting intricate designs and shapes from acrylic sheets.
2.2 Polycarbonate
Similar to acrylic but more impact-resistant, polycarbonate is common in industrial applications.
CNC Techniques: Routers and mills can be set to achieve a smooth surface finish without cracking.
With the rise of technology, composite materials have seen increased use, combining various elements to enhance performance.
3.1 Carbon Fiber
Carbon fiber provides exceptional rigidity and strength while being lightweight, making it ideal for high-performance applications.
CNC Techniques: CNC machining can accurately cut and shape carbon fiber for prototypes and final products.
3.2 Glass Fiber Reinforced Polymer (GFRP)
GFRP materials are often used in construction and automotive applications due to their durability.
CNC Techniques: This material can be processed using specialized CNC routers capable of handling fiber-reinforced materials.
The CNC Machining Process for Different Materials
The CNC machining process varies considerably based on the materials being worked on. Here’s an overview of the common steps involved in CNC machining for each category.
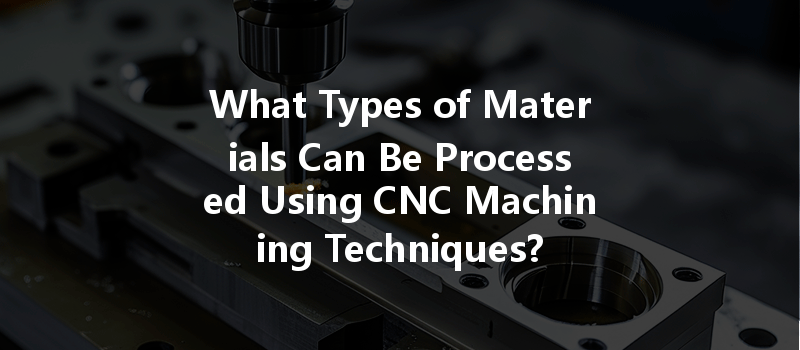
The first and foremost step is to pick the appropriate material suited for the intended application and end-use. This choice influences the subsequent machining methods, tools, and formulation of design.
Before CNC machining can begin, a Computer-Aided Design (CAD) file is created. This digital blueprint ensures precision and accuracy in representations of the component that needs to be manufactured.
Tool selection is critical for achieving high-quality results. Each material might require different tooling materials or types, including carbide, high-speed steel, or specialty tools for composites.
This step involves translating the CAD design into G-code, which instructs the CNC machine on how to move, cut, and assemble. Advanced programming software is often used to facilitate this encoding.
Once the machinery is set up, the actual machining begins. The CNC machine follows the programmed instructions to perform tasks such as milling, drilling, or turning, shaping the material into a final product based on the original design specifications.
After machining, components may undergo additional processing to achieve desired surface finishes—these may include polishing, anodizing, or coating to enhance durability and aesthetics.
Pros and Cons of Using CNC Machining for Different Materials
Advantages
Disadvantages
Case Studies
Case Study 1: Aerospace Industry
The aerospace industry requires high precision, weight reduction, and strong materials. CNC machining enables manufacturers to craft intricate components from lightweight metals like titanium, achieving high performance while ensuring safety and reliability.
Case Study 2: Medical Devices
In the medical industry, CNC machining is pivotal in creating surgical instruments and implants out of stainless steel and biocompatible plastics. The capability to adhere to strict regulations is instrumental in developing devices that require high accuracy.
Case Study 3: Automotive Parts
In automotive manufacturing, the ability to machine parts from a variety of metals and plastics is essential for both performance and aesthetic requirements. Companies can create complex engine components and lightweight body parts using advanced CNC techniques.
Future Trends in CNC Machining
As technology develops, more manufacturers are likely to adopt automated CNC systems to gain higher production rates and efficiency.
The focus is likely to shift towards new materials, including bio-based composites and lighter alloys with enhanced strength and durability.
Artificial Intelligence can enhance precision in CNC machining by predicting potential issues before they occur, optimizing processes for better efficiency.
CNC machining has revolutionized how manufacturers produce components across a wide range of materials. From metals like steel and titanium to versatile plastics and advanced composites, CNC machines can adapt to various requirements, making them invaluable tools in numerous industries. Understanding the diverse types of materials that can be processed through CNC machining is crucial for manufacturers aiming to remain competitive in a rapidly evolving technological landscape.
As you reflect on the significance of CNC machining in today’s manufacturing world, remember that the capacity to work with different materials opens up endless possibilities for innovation and design. This versatility is not merely an advantage; it’s a necessity for companies aiming to meet consumer demands with high-quality, precise products. Whether you’re an industry professional or a curious reader, recognizing the importance of CNC machining and its applications is essential to appreciate the future of fabrication and manufacturing.
Now that you’re informed about the variety of materials CNC machining can handle, consider how this knowledge might influence your next project or business decision.