Did you know that the melting point of steel can vary significantly based on its chemical composition? While many people believe steel is a uniform material, the reality is far more complex. From construction to aerospace, steel’s versatility and strength make it a fundamental component in various industries. Yet, understanding how its composition influences its melting point can be the key to optimizing CNC machining processes and ensuring the integrity of final products.
Understanding Steel Composition
To effectively navigate CNC machining—especially when working with different grades of steel—it’s essential to understand what steel is made of. Steel is primarily composed of iron, but its precise characteristics depend heavily upon the addition of other elements. The most common alloying elements include:
The variations in these elements lead to different grades of steel, each exhibiting unique properties, including melting points.
The Melting Point of Steel: An Overview
The melting point of a material is one of its most critical properties, especially in applications involving CNC processing. For most carbon steels, the melting point is typically between 1425°C to 1540°C (2600°F to 2800°F). However, stainless steels and other alloyed steels can have varying melting points depending on their specific chemical compositions.
The Impact of Chemical Composition on Melting Point
The amount of carbon present in steel has a direct correlation with its melting point. Higher carbon concentrations typically lead to increased melting temperatures. For instance, while low-carbon steels (around 0.05% to 0.15% carbon) have a lower melting point, high-carbon steels (0.60% to 1.00% carbon) will require higher temperatures to melt effectively.
Each alloying element has a distinct influence on the melting behavior. Here’s a brief overview:
The internal structure of steel plays an essential role in its melting behavior. For example, a pearlitic or martensitic structure will behave differently under heat compared to a ferritic structure. Adjusting the heat treatment processes can also alter these microstructures, which directly affects how the material responds to machining processes.
Implications for CNC Machining
Understanding the relationship between the melting point and chemical composition is crucial in CNC processing for several reasons:
When machining steel with different melting points, it’s paramount to select appropriate cutting tools. Tools must withstand the heat generated during processing. High-speed steels (HSS) and carbide tools can be evaluated based on the melting point of the steel being machined.
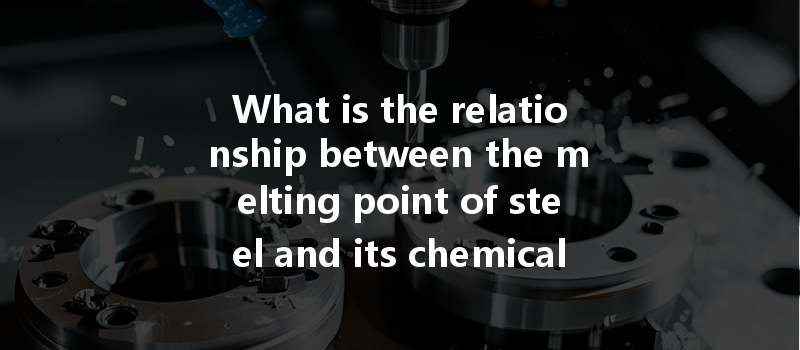
Effective temperature management can help maintain the integrity of the steel part being processed. Knowing the melting point allows technicians to adjust feed rates and spindle speeds accordingly, which helps prevent unwanted thermal deformation.
Prior to the CNC machining process, heat treatment methods such as tempering and annealing might be implemented to manipulate the microstructure of the steel. Understanding the melting point helps in designing heat treatment cycles for optimal results.
Keeping track of chemical compositions and melting points contributes to the quality assurance process. Materials can be pre-tested to ensure they meet specifications before machining begins.
Selecting the appropriate steel based on its melting point can also influence production costs. For example, excessive overheating due to incorrect parameters can lead to material wastage, thus impacting project budgets.
Solutions and Best Practices
To effectively leverage the knowledge of steel melting points and chemical compositions in CNC machining, here are some best practices and solutions:
Utilize material testing to verify the composition of the steel before beginning the machining process. This ensures that the material adheres to required specifications regarding melting point and performance.
Adjust machine settings based on the melting points of the materials being processed. Consult heat tables or software that provides insights into the appropriate parameters for specific alloys.
Invest in regular training for CNC operators to understand the implications of steel’s chemical compositions. Knowledge of how to anticipate and respond to issues related to melting points can improve overall efficiency.
Implement adaptive machining technologies that respond in real-time to material behaviors. This technology can help monitor temperatures and adjust parameters dynamically, ensuring optimal cutting without risking melting or deformation.
Keep detailed records of steel compositions for all projects. Establish a traceability system that allows quick identification of the materials’ properties in case of quality checks. This will foster an environment of accountability and continuous improvement.
Understanding the melting point of steel and its relationship with the chemical composition is vital for successful CNC machining. By gaining insights into how different alloying elements alter melting temperatures, manufacturers and machinists can optimize their processes, ensure material integrity, and enhance the overall quality of their products.
The intersection of science and manufacturing in CNC processing offers exciting possibilities, but it comes with challenges. As industries demand ever-more precise components made from various grades of steel, a sound understanding of these relationships is not just advantageous—it’s imperative.
We hope this blog has illuminated the complexities surrounding steel’s chemical composition and melting point and provided practical solutions to optimize CNC machining processes. Whether you’re an engineer, a machinist, or a manufacturer, this is a crucial area worth considering as you strive for excellence in your operations.