Did you know that the aerospace industry alone accounts for approximately $800 billion annually, in large part due to its reliance on high-precision parts? Custom CNC machining has emerged as an essential solution for manufacturers across diverse sectors that demand high-tolerance components to ensure the safety, efficiency, and performance of their products. But what exactly does the process involve, and why is it so crucial in today’s manufacturing landscape? In this comprehensive guide, we delve into the intricacies of custom CNC machining for high-tolerance components, examining methodologies, benefits, applications, and future trends.
Understanding Custom CNC Machining
What is CNC Machining?
Computer Numerical Control (CNC) machining is a process that uses computer-controlled tools to manufacture parts and components with incredible precision. Commands generated from a Computer-Aided Design (CAD) program dictate the movements and operations of the machines, allowing for greater consistency and accuracy compared to traditional manufacturing processes.
High-Tolerance Components Defined
High-tolerance components are parts manufactured to strict specifications and dimensional tolerances, often within a few thousandths of an inch. These components are critical in industries like aerospace, automotive, medical devices, and precision engineering, where even the smallest deviation can lead to performance failures or safety hazards.
The Rise of Custom Solutions
The demand for customized parts has surged in recent years as industries pivot towards specialized, low-volume production runs and rapid prototyping. This shift requires manufacturers to employ agile technologies like CNC machining to meet specific customer requirements efficiently.
The Process of Custom CNC Machining
Step 1: Design and Prototyping
The process begins with the product design phase. Engineers and designers use CAD software to visualize the component, paying close attention to specifications and tolerances. Prototype models are generated to test the design’s functionality, aesthetics, and manufacturability.
Design Considerations:
Step 2: Programming the CNC Machine
Once the prototype design is finalized, the next step involves programming the CNC machine using a process called Computer-Aided Manufacturing (CAM).
Key Programming Elements:
Step 3: Setup and Calibration
Before machining begins, the CNC machine must be set up. This includes positioning the workpiece on the machine bed, securing it, and calibrating the tools to ensure precise machining operations.
Realignment Steps:
Step 4: Machining Process
With everything set, the CNC machine executes the programmed operations. Various types of CNC machines, such as CNC mills, lathes, and routers, may be employed depending on the nature of the component.
Types of Machining Operations:
Step 5: Quality Control
Quality checks are vital throughout the machining process. Inspecting dimensions and tolerances ensures that the final product meets specifications.
Methods Used:
Step 6: Finishing and Post-Processing
After machining, several finishing processes may be required, including deburring, anodizing, or surface treatment, to enhance performance characteristics or aesthetics.
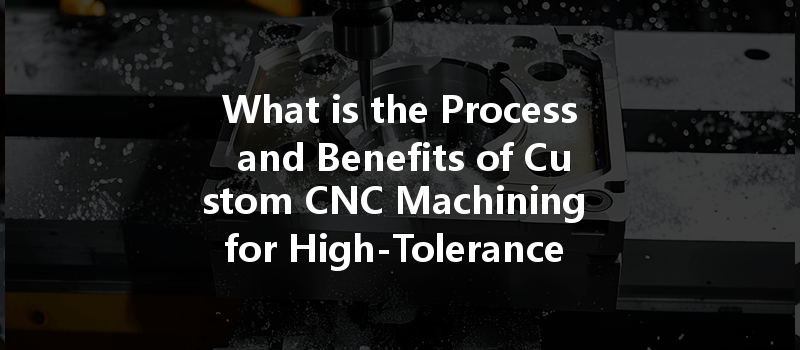
Benefits of Custom CNC Machining for High-Tolerance Components
CNC machines can produce parts to tolerances of +/
Once programmed, CNC machines can reproduce exact duplicates of components time and time again, substantially reducing variability that can stem from traditional manufacturing methods.
With CNC machining, engineers can make modifications to designs without needing significant adjustments in manufacturing setups. This flexibility fosters innovation and rapid product development.
CNC machining often leads to reduced cycle times, especially when combined with automation and advanced manufacturing practices. This efficiency results in lower production costs, even for small batch sizes.
CNC machining can be used with a wide variety of materials, including metals, plastics, and composites, accommodating diverse industry requirements.
Because CNC machining uses automated tools to remove material only where necessary, it often produces less waste compared to traditional methods, contributing to more sustainable manufacturing practices.
Applications of High-Tolerance Components Made by CNC Machining
Aerospace Industry
CNC machining is vital for aerospace parts such as turbine blades, structural components, and landing gear, where high-tolerance specifications are crucial for safety and performance.
Automotive Manufacturing
From engine components to precision gears, the automotive industry heavily relies on custom CNC machining to improve performance, fuel efficiency, and safety.
Medical Devices
In the medical field, components like implants, surgical instruments, and diagnostic devices require strict adherence to tolerances for safety and efficacy.
Defense Sector
High-tolerance components for defense applications, ranging from firearms to drones, highlight the importance of precision manufacturing.
Electronics
CNC machining produces intricate parts for electronic devices, including connectors, housings, and circuit boards, where precise alignment and dimension are essential.
Future Trends in Custom CNC Machining
Industry 4.0 and Smart Manufacturing
The advent of Industry 4.0, characterized by interconnected machines and data analytics, is poised to revolutionize CNC machining. Real-time monitoring systems will optimize production efficiencies and enhance quality control.
Automation and Robotics
The integration of robotics in CNC machining will streamline operations, allowing for autonomous manufacturing that minimizes human intervention, reduces the risk of error, and increases productivity.
Advanced Materials
The evolution of new composite and hybrid materials will pose challenges and opportunities for CNC machining, enabling manufacturers to innovate with previously unachievable designs and performance characteristics.
3D Printing Integration
Combining CNC machining with additive manufacturing will provide hybrid solutions offering capabilities for rapid prototyping and complex geometries that traditional methods may not be able to produce.
Custom CNC machining for high-tolerance components is a cornerstone of modern manufacturing, providing precision, consistency, and flexibility for businesses across various industries. By understanding the detailed process, benefits, and future trends of this essential technique, manufacturers can enhance their operations and remain competitive in today’s fast-paced market.
In summary, whether you’re in aerospace, automotive, or medical industries, understanding CNC machining is vital for producing high-quality components that meet rigorous standards. Investing time to learn about this process will empower businesses to elevate their manufacturing capabilities, innovate more effectively, and ultimately drive success in their field.
So, as we move forward into an era defined by technological advancement and increased specialization, considering the implications of CNC machining becomes more critical than ever. Embrace the precision, efficiency, and possibilities it offers, and ensure that your ventures remain at the forefront of industry innovation.