When considering materials for CNC turning, the choice between 440C and 410 stainless steel can significantly impact the performance and durability of components. At YL Machining, we understand that the selection of the right material hinges on their mechanical properties, corrosion resistance, heat treatment capabilities, and suitability for specific applications. In this article, we’ll delve into the differences between these two alloys, highlighting their key characteristics and ideal usages in CNC turning operations.
Composition and Properties
410 Stainless Steel
440C Stainless Steel
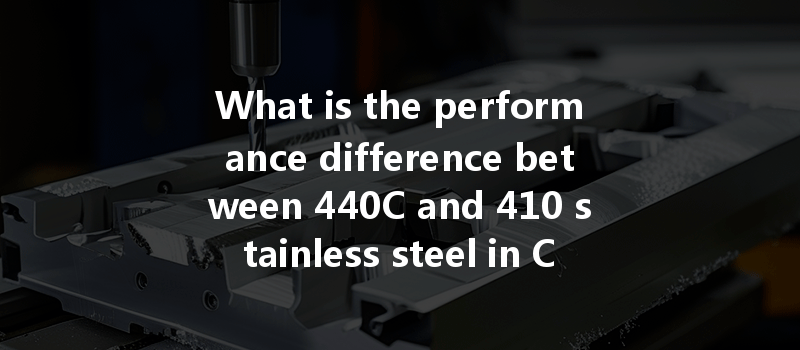
Machinability
Both materials can be machined effectively; however, 410 stainless steel is generally regarded as easier to machine due to its lower hardness compared to 440C. The increased hardness of 440C means that it may require specialized tooling, higher cutting speeds, and more robust machine setups to achieve optimal results while minimizing tool wear.
Applications and Suitability
In summary, while both 440C and 410 stainless steel have their respective advantages in CNC turning applications, the choice largely depends on the specific requirements of your project. If higher corrosion resistance and hardness are priorities, 440C would be the superior option, albeit with more challenging machinability. Conversely, the more accessible 410 steel offers a balance of moderate properties ideal for less demanding environments.
At YL Machining, we are dedicated to helping you navigate the complexities of metal selection and CNC machining processes. By understanding the distinctions between 440C and 410 stainless steels, we can assist you in making informed decisions that enhance your project’s performance and longevity. If you require further assistance or need a quote for your next project, feel free to reach out to our team.