: The Importance of Surface Finish
Did you know that the surface finish of machined parts can account for as much as 30% of the total cost of those parts? In the world of CNC (Computer Numerical Control) machining, the surface finish is crucial, as it directly impacts the functionality, performance, and aesthetic appeal of machined components. One commonly sought finish in the industry is the RA (Roughness Average) 0.8 finish for aluminum components, recognized for its smoothness and suitability for various applications requiring a degree of precision.
For manufacturers aiming for quality, understanding how to measure and achieve an RA 0.8 finish can be critical to their success. This comprehensive guide explores the measurement methods for achieving an RA 0.8 finish in aluminum CNC machining, offering detailed insights to ensure you grasp both the theory and practice behind it.
—
1.1 What is Surface Finish?
Surface finish refers to the texture and roughness of a surface produced by a manufacturing process, including CNC machining. Factors include the subtle (or not-so-subtle) variations in surface texture that can significantly affect the part’s quality and functionality.
1.2 Importance of Surface Finish
An optimal surface finish can enhance a part’s durability, lower manufacturing costs through less wear on tools and machines, and improve aesthetics for products where appearance matters. Industries such as aerospace, automotive, and electronics heavily regulate surface finish standards to ensure safety and performance.
1.3 Common Surface Finish Metrics
A few key metrics used to describe surface roughness include:
2.1 Definition of RA 0.8 Finish
RA 0.8 finish denotes a specific surface roughness value, with the ‘Ra’ indicating a roughness average of 0.8 micrometers (µm) or 0.0008 millimeters. It is a common finish requirement in various applications where smooth surfaces contribute significantly to the operation of parts.
2.2 Applications of RA 0.8 Finish
Components requiring RA 0.8 finishes are found in sectors like:
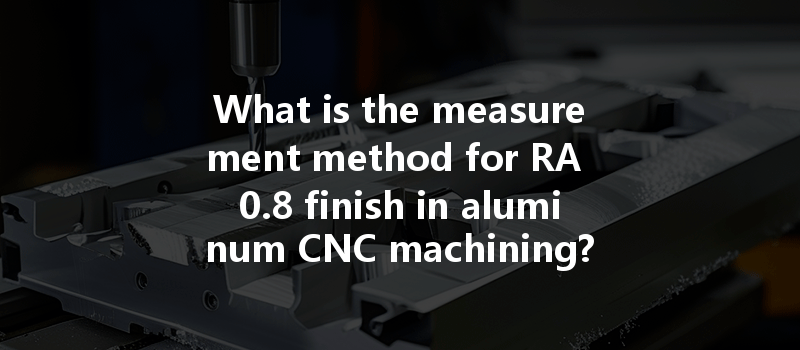
2.3 Benefits of Achieving RA 0.8 Finish
An RA 0.8 finish reduces the potential for stress concentrations, improves contact performance, and decreases the chances of galvanic corrosion occurring on machined aluminum parts.
3.1 Contact Measurement Methods
Contact measurement techniques involve placing a probe in contact with the surface to gather data about roughness. The most common tools include:
3.2 Non-contact Measurement Methods
Non-contact methods use light or laser technology to measure surface features without touching the surface. These methods minimize potential damage and are important in delicate applications:
3.3 Selective Measurement Tools and Their Uses
Various instruments can be utilized based on the materials and precise requirements, including:
4.1 Importance of Machining Parameters
Every parameter in the CNC machining process affects the resultant surface finish. Key aspects include:
4.2 Tool Selection and Toolpath Strategy
Choosing the right tool for the job is crucial. Hard, sharp tools typically yield better finishes. Moreover, implementing strategies like climb milling can create smoother finishes than conventional milling.
4.3 Cutting Speed and Feed Rate Optimization
Optimizing cutting speed and feed rate can have a significant impact on surface finish quality. Higher speeds often produce smoother finishes, but they must be matched with the correct feed rate to prevent tool wear and ensure controlled material removal.
5.1 Surface Treatments: Anodizing, Polishing, and Coating
Surface finishing processes such as anodizing and polishing can improve a component’s surface finish further post-machining. Anodizing can enhance durability, while polishing can achieve the desired smoothness.
5.2 Importance of Cleaning and Deburring
Post-machining cleaning and deburring are vital for removing any burrs or particulates that could compromise the surface finish. Employing techniques such as ultrasonic cleaning can ensure thorough removal.
5.3 Quality Control and Inspection Processes
Implementing robust quality control measures ensures that the surface finish meets specified standards. Regular inspection intervals, involving both visual and instrumental checks, are crucial for maintaining high-quality outputs.
6.1 Case Study 1: Aerospace Component Manufacturing
This case study details how a leading aerospace manufacturer improved surface finish on critical components by adopting advanced CNC machining technologies combined with rigorous quality inspection.
6.2 Case Study 2: Medical Device Production
A medical device company faced challenges meeting strict FDA requirements. They implemented systematic quality control processes that included R&D into the optimal conditions for achieving RA 0.8 finishes on sensitive components.
6.3 Case Study 3: Automotive Applications
A manufacturer specializing in automotive engine parts discovered new tooling methods that minimized surface roughness variations, achieving uniform RA 0.8 finishes and beneficial production scales.
7.1 Common Issues Faced by Manufacturers
Manufacturers often face challenges such as tool wear, fluctuations in machine performance, and material inconsistencies that impact the ability to achieve a desired surface finish.
7.2 Solutions and Best Practices
Maintaining a solid maintenance schedule for machines, leveraging advanced technologies, and investing in operator training can mitigate many challenges associated with achieving consistent surface finishes.
7.3 Continual Improvement Strategies
Engaging in continual improvement methodologies such as Six Sigma can help manufacturers systematically identify areas for improvement in achieving and measuring surface finishes.
: The Importance of Precise Measurement in CNC Machining
Achieving an RA 0.8 finish in aluminum CNC machining requires not only meticulous attention to measurement methods but also an understanding of the entire machining process—from tool selection to post-machining treatments.
This blog has detailed the importance of surface finishes, particularly RA 0.8, the various measurement methods available, and the best practices to achieve quality results. Remember that the surface finish of your components can greatly influence their performance and longevity. As manufacturing continues to evolve, staying informed about techniques and technologies for measuring and achieving desired finishes will be paramount in ensuring quality and competitive advantage.
In closing, the knowledge gained from this guide will equip you with the necessary tools to think critically about surface finishes in your own projects. By focusing on precise measurement and high standards, you can demonstrate excellence in your work, ensuring that you not only meet but exceed expectations in today’s fast-paced manufacturing environment.