Did you know that aluminum is one of the most abundant elements in the Earth’s crust, making up about 8% of it? This lightweight metal not only has excellent corrosion resistance but also maintains its strength at elevated temperatures compared to many other metals, making it ideal for various engineering applications. Among the many grades of aluminum, the 5052 alloy stands out due to its unique combination of strength, formability, and resistance to aggressive environments. But just how well does 5052 aluminum perform when subjected to high temperatures? In this comprehensive guide, we will explore the high-temperature resistance of CNC machined 5052 aluminum and its many applications.
Understanding 5052 Aluminum Alloy
Composition and Properties
5052 aluminum belongs to the 5000 series of aluminum alloys, which are primarily alloyed with magnesium. Its composition typically includes:
Mechanical and Thermal Properties
5052 aluminum is known for its excellent mechanical properties, which include:
When it comes to thermal properties, 5052 aluminum exhibits a melting point of approximately 607°C (1,125°F). This data point is crucial for understanding its high-temperature resistance.
High-Temperature Resistance Characteristics
One of the standout features of 5052 aluminum is its ability to withstand elevated temperatures without significant loss of mechanical integrity. Research indicates that:
CNC Machining and Its Impact on Properties
CNC (Computer Numerical Control) machining is a widely utilized manufacturing process that employs computers to control machine tools. This method allows for a high degree of precision when machining 5052 aluminum. One of the significant advantages of CNC machining is that it can enhance the mechanical properties of the alloy.
Cold working that occurs during machining often leads to work-hardening effects, further increasing the material’s strength. However, care must be taken to manage heat during the machining process to prevent thermal distortion and maintain dimensional accuracy.
Applications of 5052 Aluminum
The versatility of 5052 aluminum makes it suitable for various applications, particularly where high strength-to-weight ratios and corrosion resistance are required.
5052 aluminum is commonly used in the automotive sector for manufacturing components such as:
Due to its high-temperature resistance, it can effectively withstand the fluctuating temperatures encountered in various components.
In marine environments, where parts are frequently exposed to saltwater and high humidity, 5052 aluminum’s excellent corrosion resistance is beneficial.
Applications include:
These applications require materials that can endure both mechanical stress and thermal variations, which makes 5052 an ideal choice.
5052 aluminum is often employed in the aerospace industry due to its lightweight properties and strength under high temperatures. Common aerospace applications include:
Since aerospace components frequently experience variations in temperature, the high-temperature resistance of 5052 aluminum contributes to the safety and durability of these parts.
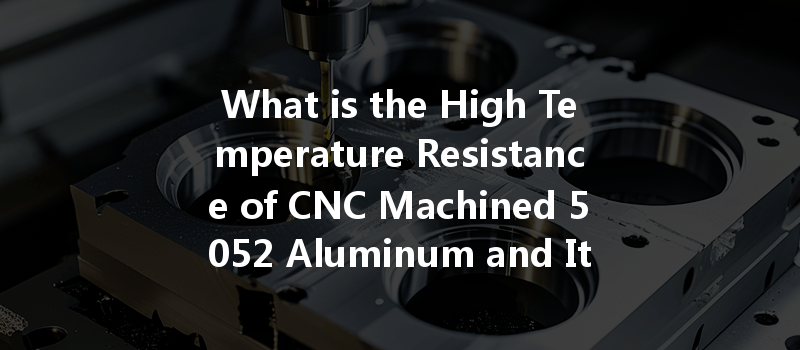
The architectural industry has also embraced 5052 aluminum for building facades, structural components, and roofing systems. The material’s resistance to weathering and high temperatures makes it suitable for:
Apart from being structurally sound, the lightweight nature of this alloy can significantly reduce the overall weight of structures.
In various industrial settings, 5052 aluminum is an effective choice for components exposed to high-temperature operating environments. Typical applications include:
Ultimately, the material’s properties enable it to perform effectively even in the most demanding industrial applications.
Challenges and Solutions in High-Temperature Machining
While 5052 aluminum is well-known for its performance at elevated temperatures, specific challenges arise during CNC machining processes, particularly when managing the thermal effects that come into play. Below, we will discuss some of these challenges and offer practical solutions.
Challenge:
CNC machining processes can generate substantial heat, leading to thermal expansion and potential distortion of parts made from 5052 aluminum.
Solution:
Employ precise cooling techniques during machining, such as:
Challenge:
High temperatures can accelerate tool wear, affecting machining accuracy and part quality.
Solution:
To combat tool wear, manufacturing teams can adopt strategies such as:
Challenge:
Occasionally, the surface finish of CNC machined components may be compromised due to high temperatures.
Solution:
Implement finishing techniques post-machining. For example:
Challenge:
Rapid thermal fluctuations can induce residual stresses in machined parts, potentially compromising their structural integrity.
Solution:
Control thermal contraction by allowing machined components to cool uniformly and carefully managing post-machining heat treatment processes.
The Future of 5052 Aluminum in High-Temperature Applications
As technology evolves, so too does the potential for enhanced performance of materials like 5052 aluminum in high-temperature applications. Innovations such as advanced alloying techniques, new machining technologies, and surface treatments may unleash even greater capabilities in managing high-temperature resistance.
Emerging Technologies
In summary, 5052 aluminum offers impressive high-temperature resistance combined with excellent mechanical properties and corrosion resistance, making it an exceptional choice for a range of applications from automotive to aerospace. By understanding its capabilities, businesses can fully leverage this alloy’s potential through careful consideration of machining processes and innovative technologies.
As industries evolve, the need for materials that can withstand high temperatures with minimal degradation will only grow. Keeping abreast of advancements in CNC machining and innovations in material technologies is vital. This not only enables companies to remain competitive but also ensures the products they deliver meet safety and quality standards in increasingly demanding operating conditions.
Reflecting on the importance of this topic, it is clear that understanding 5052 aluminum’s properties and machining techniques is essential for success in a rapidly evolving landscape. Remember that the next time you encounter an aluminum application, it may very well be the resilient 5052 alloy working diligently behind the scenes to stand the test of time and temperature. Consider this: how might your industry benefit from leveraging the unparalleled potential of 5052 aluminum? Let your imagination guide you as you explore the possibilities.