Did you know that fire incidents in manufacturing lead to an estimated loss of over $2.3 billion annually in the United States alone? This statistic not only highlights the financial implications of fires in industrial settings but indicates a pressing need for companies to prioritize safety. One critical aspect of this safety measure depends on understanding the fire resistance of materials, especially CNC machined parts, which serve as the backbone of modern manufacturing.
In this comprehensive blog, we will explore the fire resistance of CNC machined parts, including the types of materials used, their properties, testing methods, and implications for manufacturing. The goal is to provide manufacturers with detailed solutions and insights that can enhance their fire safety protocols and reduce potential risks.
1.1 What is CNC Machining?
Computer Numerical Control (CNC) machining is a method that employs computer-aided design (CAD) to control tools and machinery. It offers significant advantages, including precise cuts, high efficiency, and the ability to produce complex geometries. CNC machining has a wide range of applications, including in the aerospace, automotive, and medical sectors.
1.2 Importance of Materials
CNC machined parts can be made from various materials, including metals, plastics, and composites. The choice of material can significantly impact the performance and safety of the parts, especially in fire-prone environments. Materials with higher fire-resistance ratings can prevent or minimize the spread of fire, protect sensitive components, and ensure worker safety.
2.1 Safety First
Fire resistance is crucial in any manufacturing environment. In CNC machining, processes often involve high temperatures and friction, which can lead to ignition. Fire-resistant materials can mitigate the risks associated with such processes, potentially saving lives and preventing catastrophic damage.
2.2 Regulatory Compliance
Manufacturers are subject to various safety regulations, many of which mandate the use of fire-resistant materials in production processes. Complying with these regulations is imperative not only for avoiding penalties but also for maintaining a good reputation and customer trust.
2.3 Cost Efficiency
While fire-resistant materials may have a higher upfront cost, their adoption can save companies money in the long term by reducing the risk of fire-related damages, loss of materials, and associated legal liabilities.
3.1 Metals
3.2 Plastics
3.3 Composites
4.1 Overview of Testing Methods
Effective testing is essential to ensure materials meet fire safety standards. Common methods for testing the fire resistance of CNC machined parts include:
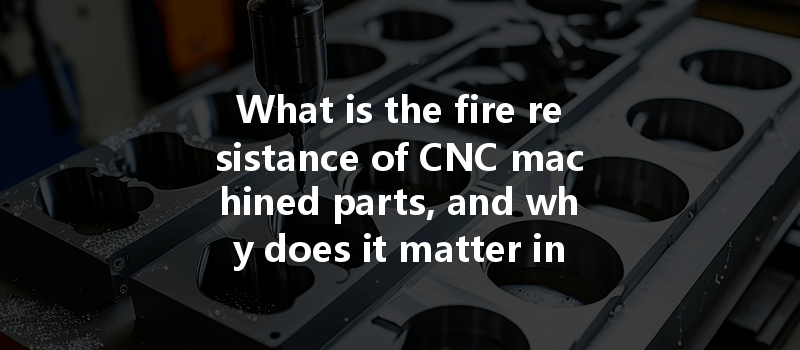
4.2 Selecting Testing Standards
Manufacturers must adhere to various national and international testing standards for fire resistance, such as:
5.1 Material Selection Criteria
Choosing the appropriate fire-resistant material involves considering:
5.2 Machining Techniques and Fire Safety
Implementing fire safety measures during the CNC machining process is crucial. Techniques include:
6.1 Aerospace Industry
In aerospace manufacturing, components undergo stringent fire testing. The use of advanced titanium alloys and flame-retardant composites reflects the industry’s commitment to safety.
6.2 Automotive Sector
The automotive industry employs fire-resistant materials and rigorous testing standards to enhance the safety of vehicles. Innovations such as flame-retardant plastics in interior components highlight this focus.
6.3 Electronics Manufacturing
Electronics manufacturers face unique fire hazards, especially regarding circuit boards and casings. The use of flame-retardant thermoplastics is common to ensure safety in volatile environments.
In conclusion, understanding the fire resistance of CNC machined parts is crucial for ensuring safety, compliance, and cost-efficiency in manufacturing. By selecting appropriate materials, implementing robust testing methods, and integrating safety measures into the CNC machining process, manufacturers can significantly reduce fire-related risks.
The implications of fire resistance go beyond compliance; they reflect a company’s commitment to safety and sustainability. Manufacturers must consider the long-term benefits and infer the importance of material selection and process improvements as they relate to fire safety in CNC machining.
As we look toward the future of manufacturing, the lessons learned from emphasizing fire resistance can lead to safer, more resilient manufacturing practices. Let’s prioritize safety—it’s not just a requirement; it’s an investment in our people and our progress.