Did you know that aluminum is the most widely used non-ferrous metal in the world, with over 80 million tons produced annually? The versatility, lightweight properties, and corrosion resistance of aluminum make it a favorite material across multiple industries, from aerospace to automotive. Yet, not all aluminum alloys are created equal. Among them, the 1100 and 3003 alloys are frequently chosen for various machining needs. But what exactly separates these two in terms of compressive performance and their utility in CNC machining? This blog will provide an in-depth analysis, toning into the world of aluminum alloys, and aiming to resolve that very question.
Understanding Aluminum Alloys
Before diving into the specifics of 1100 and 3003 aluminum alloys, it’s vital to understand what aluminum alloys are and how they’re classified. Aluminum alloys can be divided into two main types:
Both types have unique properties, but wrought aluminum alloys are particularly favored in CNC machining due to their excellent machinability.
The 1100 Aluminum Alloy
The 1100 aluminum alloy is known for its outstanding corrosion resistance, excellent thermal conductivity, and easy workability. It’s a commercially pure aluminum alloy (99% pure), making it highly ductile. The primary characteristics of 1100 aluminum include:
The 3003 Aluminum Alloy
On the other hand, the 3003 aluminum alloy is an alloyed aluminum (about 1.2% manganese) that offers improved strength while still maintaining excellent workability. Its significant attributes include:
Comparing Compressive Performance
Compressive Strength
When it comes to compressive performance, the main differentiating factor is indeed the yield strength. The 3003 alloy, with a higher yield strength than the 1100 alloy, can better withstand compressive forces. This difference implies that for applications where compressed loads are continuously applied, 3003 aluminum would generally perform better due to its ability to handle larger forces without yielding.
Stress-Strain Behavior
The stress-strain behavior is another factor that needs to be considered in compressive performance.
Factors Affecting Compressive Strength
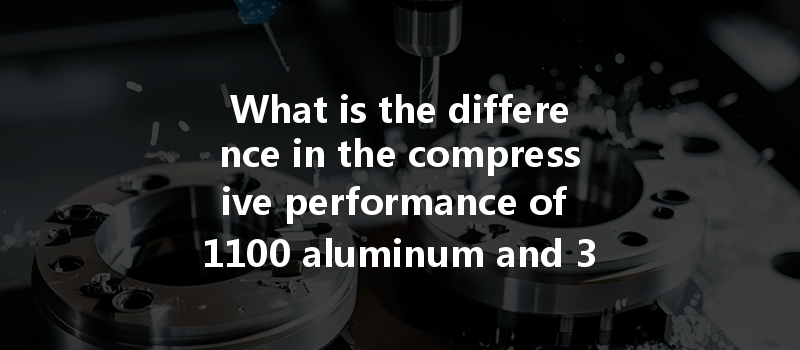
CNC Machining Considerations
When it comes to CNC machining either of these alloys, the differences in compressive performance substantially impact tooling choices, machining parameters, and anticipated outcomes.
Tool Selection
Selecting the right tool becomes essential when machining these alloys.
Machining Parameters
Several factors regarding the machining parameters need careful adjustment based on the alloy:
Surface Finish
Surface finish is often a crucial aspect in CNC machining; therefore, consider employing multiple finishing passes, especially for 3003 aluminum to achieve the desired texture and aesthetics, as its robust nature may require additional post-processing.
Real-World Applications
Understanding the differences in compressive performance can greatly inform the choice of alloys for specific applications. Here’s how each alloy holds up in real-world scenarios:
1100 Aluminum Applications:
3003 Aluminum Applications:
In conclusion, the differences in compressive performance between 1100 aluminum and 3003 aluminum primarily revolve around their yield strengths, stress-strain behavior, and how those variables affect machining processes. Understanding these differences allows manufacturers and engineers to make informed decisions about material selection based not only on strength but also on machinability, the purpose of the application, and cost-effectiveness.
Ultimately, whether you choose 1100 for its easy machinability or 3003 for its robust nature, it becomes clear that comprehending the properties and performance of these alloys is vital for successful machining processes, engineered designs, and the overall success of projects within various industries. As industries continually evolve, staying informed about material options can shed light on innovation and efficiency, making it an integral part of strategic planning in manufacturing.
Consider this blog as a gateway into understanding the subtle yet significant intricacies of aluminum alloy performance in CNC machining, ensuring that you are always a step ahead in your engineering and manufacturing endeavors. Remember, the right choice of aluminum alloy can lead to remarkable results