Did you know that aluminum is the most widely used non-ferrous metal in engineering applications? In the world of CNC machining, the choice between aluminum alloys can significantly impact the functionality and durability of the final product. Among the most popular alloys used are 6061 and 7075 aluminum, each with unique properties and applications. With a strong emphasis on surface treatment processes, this blog aims to provide a comprehensive understanding of how these two aluminum alloys differ, particularly concerning their CNC machining requirements and performance outcomes.
The Importance of Aluminum Alloys in CNC Machining
Aluminum alloys are favored in CNC machining for their lightweight, strength, and corrosion resistance. The aerospace, automotive, and electronics industries extensively use these materials, relying on their favorable characteristics to produce high-quality components. Understanding the differences between various aluminum alloys is crucial for engineers and manufacturers looking to select the right material for their projects.
Overview of 6061 Aluminum
6061 aluminum is a versatile alloy primarily composed of magnesium and silicon. Its excellent mechanical properties make it a popular choice for various applications, including structural components, marine environments, and automotive parts. Here are some key attributes of 6061 aluminum:
Overview of 7075 Aluminum
7075 aluminum is known for its exceptional strength-to-weight ratio, making it the alloy of choice for applications requiring high strength and low weight. Commonly used in aerospace components, military applications, and performance vehicles, 7075 aluminum boasts the following characteristics:
Comparing Surface Treatment Processes
Surface treatment processes are crucial in enhancing the properties of aluminum alloys, providing protection against wear, corrosion, and environmental effects. Understanding how the surface treatments differ for 6061 and 7075 aluminum can lead to better decision-making regarding their selection for specific applications.
Anodizing
Anodizing is one of the most commonly used surface treatments for aluminum alloys. The process involves creating a controlled oxide layer on the surface, enhancing corrosion resistance and appearance.
Powder Coating
Powder coating is another effective surface treatment that involves applying a dry powder to the aluminum surface, which is then cured under heat to form a protective layer.
Alodine Treatment
Alodine treatment, also known as chromate conversion coating, adds a thin, protective layer on the surface of aluminum, enhancing corrosion resistance without significantly altering the base metal’s properties.
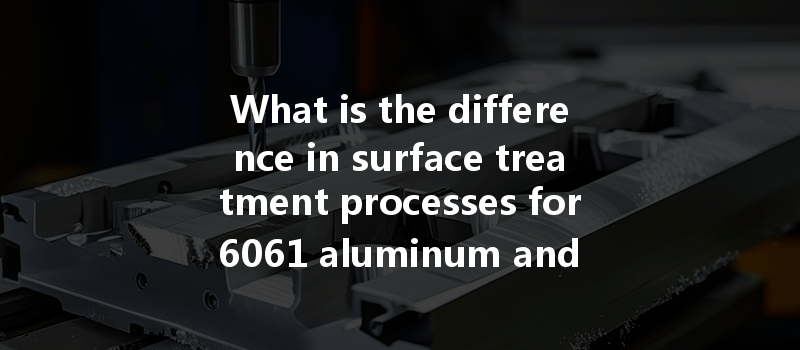
Cleaning and Degreasing
Before applying any surface treatment, cleaning and degreasing are vital steps that influence the adhesion and effectiveness of the applied coatings.
Comparison of Machinability
Both 6061 and 7075 aluminum exhibit good machinability; however, there are important differences that can influence their processing in a CNC machining environment.
Summary of Surface Treatment Differences
Real-World Applications for 6061 and 7075 Aluminum
Understanding the surface treatment differences is essential for making informed decisions regarding material selection in specific applications.
Applications of 6061 Aluminum
Applications of 7075 Aluminum
In summary, understanding the differences in surface treatment processes for 6061 aluminum and 7075 aluminum in CNC machining is crucial for manufacturers, engineers, and anyone involved in the production of components from these popular alloys. While both alloys have their strengths and weaknesses, selecting the right surface treatment processes can significantly affect performance, aesthetics, and ultimately, the success of the end application.
By knowing the correct surface treatment methods for each aluminum alloy, manufacturers can enhance durability, improve corrosion resistance, and meet the specific requirements of their projects. As we continue to push the boundaries of engineering applications, it is essential to stay informed about these vital differences to ensure optimal results.
Investing time in understanding these distinctions is vital not only for product performance but also for cost-effectiveness and efficiency in production. As industries increasingly rely on advanced materials, knowing how to take advantage of the unique characteristics of each aluminum alloy can make a significant difference in the success of any CNC machining endeavor.
So, as you reflect on the information shared in this blog, consider the impact that informed decisions about aluminum alloys and their treatment can have on the future of your projects.