Opening
Did you know that aluminum is one of the most widely used metals in the world, accounting for nearly 25 million tons produced annually? Among the various grades of aluminum, 6061 and 6063 are two of the most prominent, particularly in the realm of CNC (Computer Numerical Control) machining and turning. If you’ve ever wondered why manufacturers often choose one over the other for specific applications, then you’re in the right place. In this blog, we’ll dive deep into the differences between 6061 and 6063 aluminum, explore their machining effects during CNC turning, and identify which material is best suited for your project needs.
Understanding 6061 and 6063 Aluminum Alloys
Before we dive into the CNC turning specifics, let’s start by understanding what these two aluminum alloys are all about.
6061 Aluminum Alloy
6061 aluminum is a versatile, high-strength alloy that is commonly used in various applications, including aerospace, automotive, marine, and structural engineering. It primarily consists of magnesium, silicon, and small amounts of various alloying elements. Its primary features include:
6063 Aluminum Alloy
On the other hand, 6063 aluminum is often referred to as the “architectural alloy” due to its aesthetic qualities. It is widely used in the construction of window frames, doors, and other architectural elements. Key characteristics include:
Summary of Comparison
| Property | 6061 Aluminum | 6063 Aluminum |
|————————–|—————-|—————-|
| Tensile Strength | ~290 MPa | ~230 MPa |
| Corrosion Resistance | High | High |
| Weldability | Excellent | Good |
| Surface Finish | Good | Excellent |
| Machinability | Good | Fair |
| Applications | Aerospace, automotive, marine | Architectural |
Now that we’ve gained insight into these two alloys, let’s address how they perform during CNC turning.
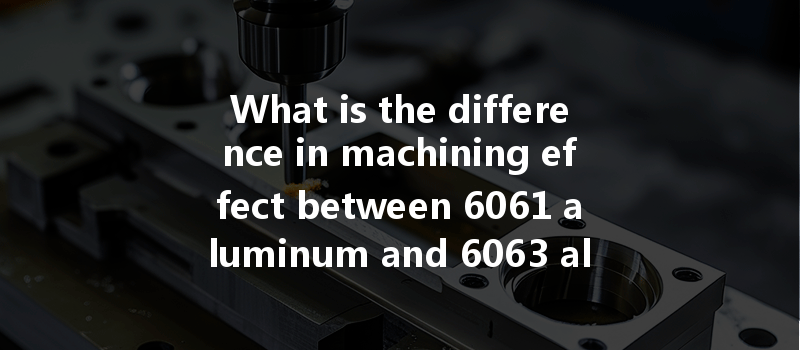
CNC Turning: Effects of Material Choices
The Role of CNC Turning
CNC turning is a precision machining process that involves removing material from a rotating workpiece to create geometrically accurate components. This process is significantly influenced by the type of material being used, and both 6061 and 6063 aluminum have their unique machining advantages and challenges.
Effects of CNC Turning on 6061 Aluminum
Effects of CNC Turning on 6063 Aluminum
Machining Solutions for Optimal Performance
To optimize CNC turning results with both 6061 and 6063 aluminum, here are some practical recommendations:
Choosing the right aluminum alloy for CNC turning is a critical decision that can significantly impact the success of your manufacturing process. While 6061 aluminum offers higher strength, versatility, and excellent machinability, 6063 aluminum excels in situations requiring superior surface finishes and formability.
CNC turning processes for both alloys each have their unique set of challenges and solutions. By understanding the specific characteristics of 6061 and 6063 aluminum, as well as how they behave under CNC turning, manufacturers can make informed decisions that enhance production efficiency and product quality.
In the ever-evolving world of manufacturing, staying informed about material options and machining technologies is essential. The distinctions between aluminum grades, such as 6061 and 6063, illuminate the relationship between material properties and machining capabilities. Hence, this topic is not only relevant but critical to consider for anyone in the machining and manufacturing sectors. Whether you are an engineer, a machinist, or a project manager, comprehending these differences paves the way for excellence in design and production.
Thank you for taking the time to explore this detailed discussion on 6061 vs. 6063 aluminum in CNC turning. Your efforts in considering these distinctions will undoubtedly lead to better manufacturing choices in your forthcoming projects. Stay informed, stay ahead!