:
Did you know that the global machining market is expected to reach a staggering $225 billion by 2025? This growth is fueled in large part by the increasing demand for precision engineering components across various industries, including aerospace, automotive, and medical devices. A significant factor that can greatly influence the overall cost of CNC machining processes is the material used—specifically, aluminum and stainless steel. But what exactly drives the cost differences between these two materials in CNC machining?
In this blog, we will explore the intricacies behind machining costs, specifically focusing on the comparative analysis of aluminum and stainless steel, their properties, the factors that affect machining costs, and ways to optimize these processes. By the end of this guide, you will have a comprehensive understanding of the financial implications of selecting between aluminum and stainless steel in CNC machining projects.
Understanding Aluminum and Stainless Steel
Aluminum is lightweight, highly malleable, and has excellent corrosion resistance, making it a popular choice for a wide range of applications. It can easily be machined, welded, and formed, thus offering high versatility.
Stainless steel, on the other hand, is known for its strength, durability, and resistance to rust and corrosion. While it offers superior structural integrity, it is heavier and often more challenging to machine compared to aluminum.
Factors Influencing Machining Costs
Cost Analysis Case Study
To illustrate the cost differences effectively, let’s consider a hypothetical CNC machining project where both aluminum and stainless steel components are required for the same application (e.g., a bracket).
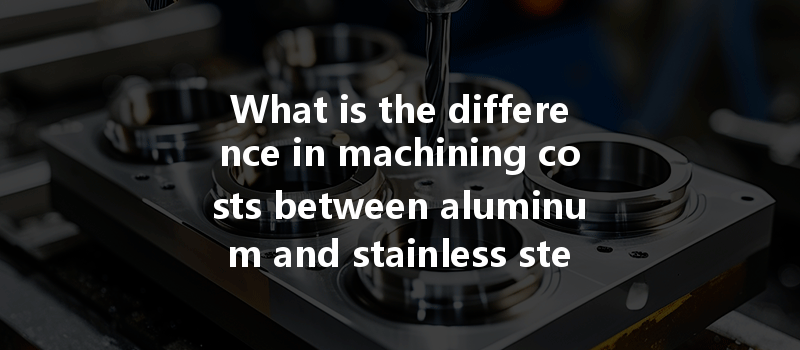
Thus, overall costs can be summarized as follows:
From this simple analysis, it becomes apparent that the cost of machining stainless steel is significantly higher than that of aluminum in this example.
Strategies to Reduce Machining Costs
Selecting the right cutting tools can reduce wear and extend their life. Utilizing tools specifically designed for the material being machined can greatly enhance process performance.
Proper settings for cutting speed, feed rate, and depth of cut can optimize machining efficiency. Knowing specific materials can help in planning the ideal parameters. For instance, stainless steel may benefit from slower speeds to prevent work hardening.
Using techniques such as high-speed machining (HSM) for aluminum and more effective cooling methods for stainless steel can vastly improve cost-effectiveness.
Utilizing CNC machines with automation features can reduce labor costs, improve consistency, and decrease cycle times, particularly important when machining stainless steel components.
In some cases, considering alternative materials or alloys may meet performance requirements at lower costs. For instance, certain aluminum alloys provide sufficient strength for specific applications while being more cost-effective.
Leveraging batch production methods for both materials may allow manufacturers to capitalize on economies of scale, ultimately leading to reduced per-unit costs.
In conclusion, understanding the differences in machining costs between aluminum and stainless steel is pivotal for any company involving CNC machining processes. While aluminum generally proves to be more cost-effective due to lower material costs, faster machining times, and easier tooling, stainless steel offers benefits in strength and applications where durability is critical. Each material possesses distinct advantages and disadvantages that must be evaluated based on specific project requirements.
Ultimately, the choice of material depends heavily on the desired properties, the application in question, and of course, budgetary constraints. By effectively analyzing these aspects and implementing strategic cost-reduction methods, manufacturers can not only manage costs but also enhance overall efficiency in their CNC machining operations.
As the machining market continues to evolve, it remains crucial for decision-makers to remain informed about emerging trends, technological advancements, and best practices in order to maintain competitiveness and operational excellence. Understanding the true costs associated with various materials is essential in shaping successful machining strategies that can lead to sustainable growth and innovation in the industry. Therefore, take time to consider your options carefully and weigh the financial implications of material choice in your next machining project. In this ever-competitive landscape, this knowledge is not merely advantageous—it is imperative.