*
Did you know that the cutting speed of aluminum can significantly affect the efficiency and quality of CNC machining processes? In the realm of manufacturing and engineering, materials such as aluminum rely heavily on the parameters of CNC machining to determine their outcome in efficiency, cost-effectiveness, and final part quality. The two most commonly used alloys, 6061 and 5052 aluminum, are fundamental in aerospace, automotive, and various industrial applications. Yet, their machining characteristics differ markedly.
In this comprehensive blog, we will explore the differences in cutting speed between 6061 and 5052 aluminum during CNC machining, delving into the reasons behind these variations and their impact on machining practices. So, let’s take a deep dive into how understanding these discrepancies can drive better results in your CNC machining projects.
—
Chapter 1: Understanding Aluminum Alloys
1.1 Aluminum Alloys: An Overview
Aluminum is one of the most widely used metals in manufacturing because of its lightweight, high strength-to-weight ratio, resistance to corrosion, and excellent machinability. Aluminum alloys are typically categorized as either wrought or cast, with 6061 and 5052 being part of the wrought category.
1.2 Why Choose Aluminum for CNC Machining?
Aluminum’s attributes address several challenges faced in manufacturing processes. Its low weight enables easier handling and processing. Furthermore, aluminum can earn a positive environmental reputation due to its recyclability and excellent durability.
—
Chapter 2: The Basics of CNC Machining
2.1 What is CNC Machining?
Computer Numerical Control (CNC) machining is a subtractive manufacturing process that utilizes computer software to control machine tools for precision manufacturing. The accuracy and repeatability provided by CNC machines enable the manufacture of complex parts with intricate designs.
2.2 Key Parameters in CNC Machining
In CNC machining, several parameters must be optimized for successful machining operations. These include:
Each of these variables plays an essential role in the quality of the final product.
—
Chapter 3: Cutting Speed Explained
3.1 What is Cutting Speed?
Cutting speed is a critical factor in the CNC machining process. It influences the heat created during machining and the wear on cutting tools. Understanding the optimum cutting speed for different materials ensures:
3.2 How is Cutting Speed Determined?
Cutting speed is generally calculated based on the material being machined and the tool being used. Factors include:
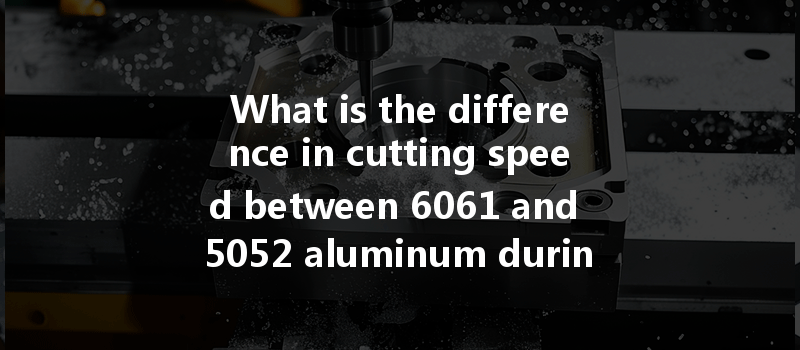
—
Chapter 4: The Cutting Speed of 6061 vs. 5052 Aluminum
4.1 Typical Cutting Speeds for 6061 Aluminum
6061 aluminum commonly operates at higher cutting speeds due to its mechanical properties. Typical cutting speeds range from 70 to 150 m/min. The specific choice within that range depends on the cutting tool material and geometry, as well as the desired surface finish.
4.2 Typical Cutting Speeds for 5052 Aluminum
Conversely, 5052 aluminum, while still machinable, generally operates at lower cutting speeds, ranging from 40 to 80 m/min. The reason for this lower value is largely due to its increased toughness and formability, which can create more heat and wear on cutting tools at higher speeds.
—
Chapter 5: Factors Impacting Cutting Speed
Several factors must be taken into account when determining the cutting speeds for 6061 and 5052 aluminum:
5.1 Material Properties
The inherent properties of both alloys, including tensile strength, hardness, and ductility, will affect their response to machining. Higher hardness can necessitate lower cutting speeds.
5.2 Tool Selection
Different tools will perform better with various materials. For instance, carbide tools are generally used with aluminum for their durability and efficiency.
5.3 Coolant Use
The use of coolant can aid significantly in dissipating heat, allowing for higher cutting speeds without compromising tool life or part integrity.
—
Chapter 6: Practical Applications of Cutting Speed Differences
6.1 Real-World Implications
In production environments, it’s crucial to select the right material and machining parameters to meet your project requirements. Considerations for 6061 aluminum include its use in automotive frames where strength is crucial, while 5052 aluminum may be more suitable for applications requiring corrosion resistance, such as marine components.
6.2 Efficient Machining Processes
Machining operators can improve efficiency by adjusting cutting speeds. For example, transitioning from 6061 to 5052 aluminum might require recalibrating machines to account for the differences in machining parameters.
—
Chapter 7:
As we have thoroughly explored throughout this blog, understanding the differences in cutting speeds between 6061 and 5052 aluminum is vital for CNC machining success. The characteristics inherent to each alloy, from their structural properties to their machinability traits, influence not only the selection of appropriate cutting speeds but also the overall quality and efficiency of the machining process.
By optimizing these parameters, engineers and manufacturers can achieve higher productivity rates, reduce tool wear, and ensure that parts meet their stringent specifications. As the manufacturing landscape continues to evolve, staying informed about such distinctions will empower businesses to make informed decisions, ultimately leading to enhanced competitiveness in the industry.
In closing, we hope this deep dive into cutting speeds in CNC machining serves as a valuable resource for you. The nuances between different aluminum alloys are not just academic; they are essential to practical applications that can significantly impact production quality and efficiency. So, the next time you engage in a CNC project involving aluminum, remember how cutting speed affects your machining outcomes and leverage this knowledge for superior results.