Did you know that stainless steel is one of the most widely used materials in the world? According to a report published by the International Stainless Steel Forum (ISSF), global stainless steel production reached approximately 52 million tons in 2022 alone. Among the numerous grades available, 347 and 316L stainless steel stand out due to their unique properties and versatile applications.
This blog aims to delve into the intricacies of 347 and 316L stainless steel, particularly focusing on how their processing methods differ in CNC machining. With an increasing number of industries adopting advanced manufacturing techniques, understanding these differences is vital for engineers, manufacturers, and designers alike.
Overview of Stainless Steel Types
Stainless steel is known for its excellent corrosion resistance, strength, and versatility. It’s an alloy primarily composed of iron, chrom, and a minimum of 10.5% chromium. The chromium content forms a passive layer of chromium oxide on the surface, preventing further corrosion.
While many grades exist, stainless steels can be broadly categorized into three families:
347 Stainless Steel:
347 stainless steel is an austenitic alloy which contains niobium and tantalum as stabilizing agents that prevent grain boundary carbide precipitation. Its high temperature strength and excellent oxidation resistance make it suitable for applications in environments subjected to high temperatures.
316L Stainless Steel:
316L is another austenitic stainless steel known for its low carbon content, making it highly resistant to corrosion – particularly pitting and crevice corrosion. The addition of molybdenum enhances its resistance to harsh chemicals, making it an ideal choice for marine and chemical industries.
Differences in Processing Methods
A. Cutting Tools
B. Machining Parameters
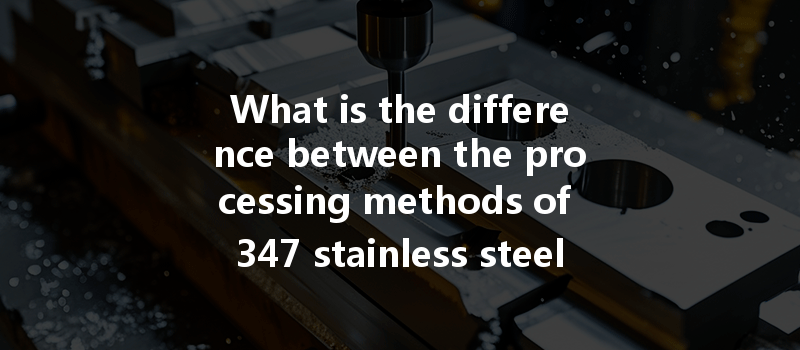
Advantages and Disadvantages
| Criteria | 347 Stainless Steel | 316L Stainless Steel |
|—————————–|—————————————–|——————————————-|
| Corrosion Resistance | High at elevated temperatures | Excellent in various environments |
| Machinability | More challenging, requires specific tools | Easier to machine |
| Cost | Generally higher due to alloying elements | Moderately priced, widely available |
| Temperature Tolerance | Superior for high-heat applications | Suitable for moderate temperatures |
| Weldability | Fair, less ideal for certain welding | Excellent, can be welded without loss of corrosion resistance |
Applications of 347 and 316L Stainless Steel
Challenges in CNC Machining 347 and 316L Stainless Steel
Both materials lead to significant tool wear, particularly due to 347’s toughness and 316L’s tendency to work-harden.
Both stainless steels exhibit thermal expansion properties. Thus, CNC machining parameters must be carefully monitored to accommodate this behavior, preventing dimensional inaccuracies.
Monitoring and Quality Control
Utilizing tools like in-process measurement and automated inspections can markedly improve the machining process and final product quality.
Post-machining, both materials should be inspected rigorously. Testing through non-destructive techniques can ensure that components meet stringent industry standards.
Maintaining a record of all the parameters can be invaluable for future projects, especially when working with complex materials like 347 and 316L stainless steel.
The differences between processing methods for 347 and 316L stainless steel in CNC machining are critical knowledge for any manufacturing operation aiming to maximize efficiency and product quality. Both materials come with unique characteristics that require tailored approaches in machining, tooling, and post-processing.
Understanding these distinctions not only enhances the capabilities of engineers and machinists but also assists them in making informed choices based on application requirements. Whether it’s in aerospace, chemical processing, or medical manufacturing, recognizing the fundamental differences between these stainless steel types can lead to optimized processes and superior end-products.
As we move further into an era of advanced manufacturing, it’s worth investing time and resources into mastering these techniques. The ability to choose the right material and the right processes enables manufacturers to push boundaries and cater to evolving industry demands.
Ultimately, this blog illustrates the importance of understanding the specifics of these stainless steel grades to ensure successful outcomes in CNC machining. So, next time you encounter a machining project involving 347 or 316L stainless steel, remember the insights shared here and the critical role they play in the larger manufacturing landscape.