When it comes to CNC machining, precision and surface quality are paramount in producing components that meet the stringent demands of various industries. Aluminum, a ubiquitous material known for its lightweight and corrosion-resistant properties, is often machined to achieve specific surface finishes that play a critical role in subsequent applications. Among the most important metrics in the manufacturing process is the concept of surface roughness, specifically the RA (Roughness Average) value. This blog aims to elucidate the difference between an RA 0.8 finish and general surface roughness in the context of aluminum CNC machining. Understanding these concepts will not only enhance product quality but also prevent costly errors during manufacturing, particularly for companies like YL Machining that aim to uphold superior quality standards.
The Basics of CNC Machining
CNC machining, or Computer Numerical Control machining, refers to the automated control of machining tools via a computer. This process turns a design into a precisely manufactured part, often using a range of materials, with aluminum being one of the most popular choices. The CNC machining process involves several operations, including milling, turning, drilling, and grinding, which can all contribute to the finished surface of the component.
When machining aluminum, operators must consider the surface finish needed for the part’s intended application. This finish impacts not just aesthetics but also functionality. An appropriate finish can enhance properties such as adhesiveness, friction, corrosion resistance, and fatigue strength.
What is Surface Roughness?
Surface roughness is a critical measure of the texture of a surface, quantified by the height of its surface irregularities. It is typically represented by the “Ra” value, which indicates the average roughness over a specified length of the surface.
The importance of surface roughness in aluminum CNC machining stems from its direct correlation with various performance attributes, including:
Decoding RA Values
The RA value, measured in micrometers or microinches, serves as an industry’s standard for assessing surface roughness. For example:
In contrast, surfaces with higher RA values, such as 3.2 or even upwards, can represent quite rough finishes and are typically suitable for less demanding applications or for parts that will undergo subsequent finishing processes, such as coating or plating.
RA 0.8 Finish Explained
An RA 0.8 finish is generally regarded as a high-quality finish, especially in aluminum CNC parts. Achieving this finish requires precise control over machining parameters and processes. Here are the key characteristics and benefits of RA 0.8 finishing:
One of the most immediate advantages of an RA 0.8 finish is the aesthetic quality it imparts to the aluminum part. This finish provides a shiny and reflective surface that enhances the overall visual appeal of the item, a crucial factor in applications such as jewelry design or consumer electronics.
Parts with RA 0.8 finishes exhibit enhanced functional properties, including:
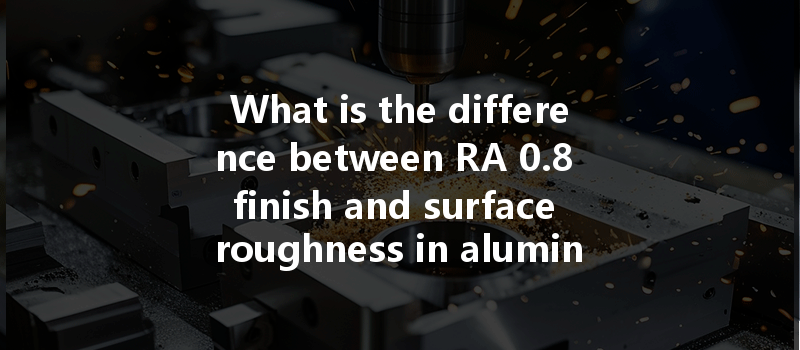
Should the part require any post-machining treatments such as anodizing or painting, the RA 0.8 surface finish often provides an ideal substrate that improves adhesion and ensures a uniform application.
Distinguishing RA from General Surface Roughness
While RA values are a specific representation of surface quality, the broader concept of surface roughness encompasses more than just RA measurements. This can include metrics such as Rq, Rz, and Rt values. Let’s delve into how these differ:
Practical Applications of RA 0.8 Finish
Given its attributes, parts with an RA 0.8 finish find application across numerous sectors, including:
The Machining Process to Achieve RA 0.8
In conclusion, understanding the difference between an RA 0.8 finish and general surface roughness in aluminum CNC machining plays a vital role in achieving high-quality and functional components. Companies like YL Machining can leverage this knowledge to better serve their clients, ensuring that parts not only meet specifications but enhance the overall performance and integrity of the products being manufactured.
By prioritizing surface quality in CNC machining processes, businesses can extract significant gains in both customer satisfaction and operational efficiency, positioning themselves as leaders in the competitive landscape of manufacturing. As we navigate through the requirements of modern machining, it becomes increasingly clear that precision, quality, and detail in every aspect hold the key to success.
—