: The Fascinating World of CNC Machining
Did you know that in the world of CNC machining, the choice of materials—plastic versus metal—can significantly impact production quality, efficiency, and cost? According to a report from MarketsandMarkets, the global CNC machine market is expected to reach $100 billion by 2025, showcasing the increasing reliance on these technologies across industries. As more businesses embrace CNC machining, understanding the nuances of different materials and their implications is crucial. One of the most critical factors that influence the machining process is the feed rate, which varies dramatically between plastics and metals.
In this comprehensive blog, we will explore the differences between plastic and metal feed rates in CNC machining. We will also dive deep into understanding how feed rates can affect machining efficiency, product quality, and operational costs, thus offering you valuable insights and detailed solutions to optimize your CNC machining processes.
—
Chapter 1: CNC Machining – A Brief Overview
CNC machining (Computer Numerical Control machining) involves the automated control of machines through computerized programming. This precision process allows for the creation of complex parts and components across various materials, including metals, plastics, composites, and more.
1.1 The Importance of Feed Rate
The feed rate is a critical machining parameter that refers to the speed at which the tool moves relative to the workpiece during machining. It is typically expressed in units such as inches per minute (IPM) or millimeters per minute (MM/min). The feed rate directly affects:
Given these implications, understanding the differences in feed rates between plastic and metal machining is fundamental for optimizing processes.
—
Chapter 2: The Feed Rates of Plastics vs. Metals
2.1 Feed Rates for Plastic Machining
Plastics are typically softer and more forgiving materials compared to metals, which allows for higher feed rates during CNC machining. Here are some key considerations:
2.2 Feed Rates for Metal Machining
Machining metals often requires more caution, as they are denser and more robust materials. This leads to lower feed rates to ensure quality and tool longevity:
—
Chapter 3: Influencing Factors on Feed Rate Selection
Choosing the right feed rate based on material type is just the beginning. Several factors can influence the appropriate feed rate you should choose for your CNC machining operation.
3.1 Tool Material and Geometry
The composition and design of your cutting tool play a significant role in determining the optimal feed rate:
3.2 Machine Capability
The type and condition of the CNC machine itself can affect feasible feed rates. High-precision CNC machines can handle higher feed rates and produce better-quality finishes than older or less-capable machines.
3.3 Workpiece Thickness
The thickness of the material also dictates the feed rate. For instance:
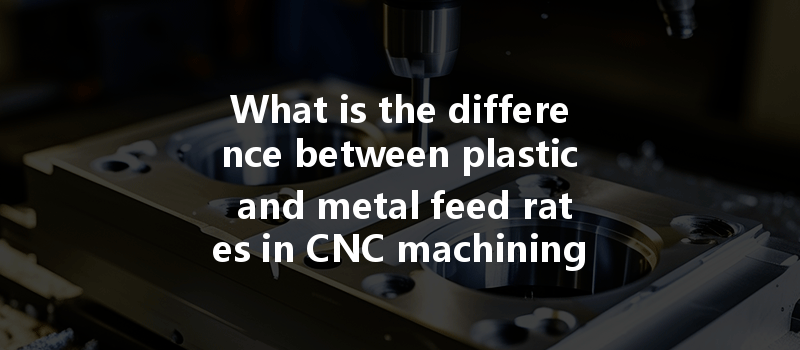
3.4 Machining Strategy
The strategy you adopt for machining can impact feed rate decisions as well. Strategies include:
—
Chapter 4: Impact of Feed Rate on Machining Outcomes
4.1 Production Time vs. Quality
4.2 Tool Wear and Longevity
4.3 Surface Finish Quality
—
Chapter 5: Best Practices for Selecting Feed Rates
5.1 Conducting Feasibility Studies
Before beginning production, conduct feasibility studies to determine the most effective feed rates without sacrificing quality.
5.2 Utilizing Simulation Software
Many modern CNC applications come with simulation software that can predict outcomes based on feed rate choices—ensure that it’s adequately utilized in your operations.
5.3 Continuous Feedback Loop
Incorporating a continuous feedback system into your CNC machining operations will allow you to adapt feed rates based on production performance.
5.4 Investing in Training
Costs associated with improper feed rate settings can add up—investing in proper training for operators to understand the nuances of feed rates can recoup this cost.
—
Chapter 6: Common Problems and Solutions
6.1 Excessive Tool Wear
6.2 Poor Surface Finish
6.3 Machine Overheating
—
: The Importance of Understanding Feed Rates
In CNC machining, the choice of materials—plastic or metal—holds considerable influence over the feed rate and, ultimately, the efficiency, quality, and cost of production. By understanding the differences in feed rates for plastics and metals, along with the factors that influence these rates, manufacturers can optimize processes, enhance product quality, and improve overall operational efficiency.
This blog should serve as a valuable resource for anyone involved in CNC machining, offering insights into best practices for feed rate selection and adjustment. With CNC machining on the rise, and the expected market growth, reconsidering the balance between speed and quality could lead to greater innovations and efficiencies in your operations.
Always remember: in the intricate world of CNC machining, the smallest adjustments can lead to significant improvements!