: The Golden Alloy Dilemma
Did you know that brass is one of the most widely used alloys in the manufacturing industry, particularly in CNC machining, due to its excellent machinability, corrosion resistance, and aesthetic appeal? Among the myriad of brass alloys available, two of the most prominent types are 75 brass and C360 brass. While they may appear to be similar at a glance, understanding their properties and applications can greatly impact the efficiency, cost, and quality of your machining processes.
In this blog, we will dive deep into the intricate world of brass alloys, exploring the fundamental differences between 75 brass and C360 brass, their machinability, mechanical properties, applications, and how to choose the right type for your CNC machining needs.
Chapter 1: Brass Alloy Basics
1.1 What is Brass?
Brass is a copper-zinc alloy known for its excellent corrosion resistance, good mechanical properties, and low friction. The varying proportions of copper and zinc give rise to different types of brass, each suited for specific applications. The versatility of brass makes it a preferred choice in various industries, including plumbing, electrical, and automotive.
1.2 Composition of Brass Alloys
Brass alloys can be categorized based on their chemical composition, which includes elements such as copper, zinc, lead, and tin. The varying percentages of these elements affect the physical and mechanical properties of the alloy.
Chapter 2: Understanding Machinability
Machinability refers to how easily a material can be machined to desired specifications. This is crucial in CNC machining where precision and efficiency are paramount.
2.1 Factors Affecting Machinability
Chapter 3: Comparisons of 75 Brass and C360 Brass
3.1 Machinability
3.2 Mechanical Properties
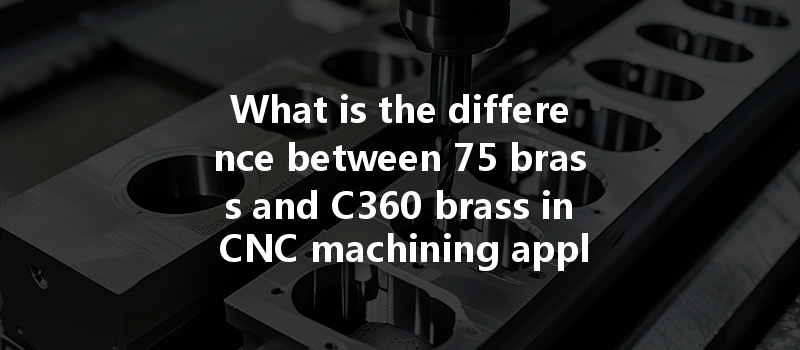
3.3 Applications
Chapter 4: Choosing the Right Brass Alloy
The decision between 75 brass and C360 brass ultimately depends on the specific requirements of your CNC machining project. Here are some criteria to consider:
4.1 Application Needs
Determine the environment the final product will operate in. For instance, if the part will be exposed to high corrosion, 75 brass may be the better choice.
4.2 Budget Considerations
C360 brass can yield cost savings in terms of machining time and tooling wear, making it the economically favorable option for high-volume production.
4.3 Desired Tolerance and Finish
If precise tolerances and high surface finishes are critical, C360 brass can provide more efficient results without sacrificing quality.
Chapter 5: Techniques for Optimizing CNC Machining with Brass
5.1 Tool Selection
5.2 Machining Parameters
: Making the Right Choice
Understanding the intricacies of 75 brass and C360 brass is essential for successful CNC machining. Each alloy has its unique advantages and disadvantages, making it vital to assess the specific needs of your project before making a decision.
In summary, choosing between 75 brass and C360 brass involves weighing factors such as machinability, mechanical properties, application needs, and cost-effectiveness. By considering these key aspects, you can optimize your CNC machining processes, reduce waste, and improve the overall quality of your finished products.
As you embark on your CNC machining projects, remember that the alloy you choose can impact not only the manufacturing process but also the longevity and performance of the final product. So, the next time you find yourself deciding between brass alloys, keep in mind the insights shared in this blog, and make informed decisions that will help you achieve optimal results in your machining endeavors.