Did you know that 6061 aluminum is among the most widely used aluminum alloys in the CNC machining industry due to its versatility and impressive mechanical properties? According to recent statistics, approximately 60% of all aluminum used in manufacturing applications is 6061 — a clear indication of its undeniable significance. When it comes to CNC machining, understanding the cutting effects of different materials, like 6061 aluminum and transparent polycarbonate (PC) plastic, can enhance the quality, precision, and efficiency of the production process.
This comprehensive guide will delve deep into the cutting effects of 6061 aluminum and transparent PC plastic in CNC machining, providing insights, techniques, and solutions to optimize machining processes and improve product quality.
Understanding 6061 Aluminum
6061 aluminum is an alloy primarily made from aluminum, silicon, and magnesium. It possesses a unique blend of properties, including:
6061 aluminum is utilized in a multitude of industries, including:
Understanding Transparent PC Plastic
Transparent PC plastic, or polycarbonate, is a thermoplastic material recognized for its clarity, toughness, and durability. Notable characteristics include:
CNC Machining: A Brief Overview
CNC (Computer Numerical Control) machining is a technology that utilizes computers to control the movement of machines, producing parts and components with high precision. The process involves:
Material selection is critical in determining the success of CNC machining. The right material not only affects the quality of the finished product but also impacts machining efficiency, tool wear, and cutting parameters.
Cutting Mechanics in CNC Machining
Choosing the right cutting tools and parameters is essential when machining 6061 aluminum and transparent PC plastic. Key parameters include:
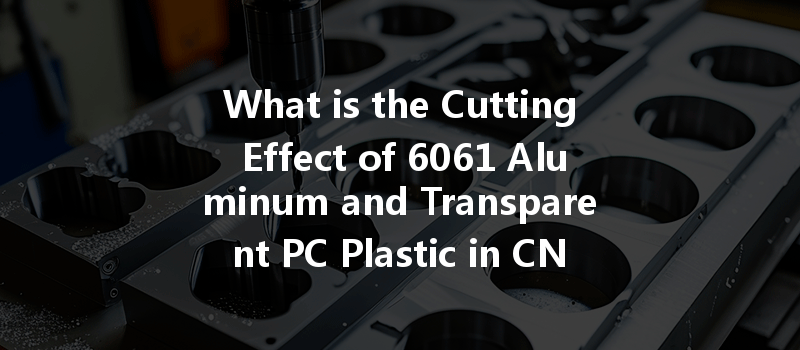
The physical and mechanical properties of both 6061 aluminum and PC plastic play crucial roles in determining the cutting effects.
Cutting Effect Analysis: 6061 Aluminum vs. Transparent PC Plastic
Machining techniques can significantly affect the aesthetic and structural integrity of the finished product. Key aspects to consider include:
The cutting effect is also tied to the longevity of the tooling. Machining aluminum tends to produce more abrasive wear on tools compared to the comparatively softer PC plastic.
Solutions to Optimize CNC Machining of 6061 Aluminum and Transparent PC Plastic
One method to improve cutting effects is to adapt cutting strategies based on the material being machined. For aluminum, strategies may include:
For PC plastic, the focus should be on:
Monitoring and managing temperatures during machining can mitigate issues like warping or melting, particularly for PC plastic. Techniques may involve:
Establish a comprehensive tool management system to:
The Future of CNC Machining: Innovations and Trends
The CNC machining landscape is ever-evolving, with new technologies emerging that could redefine the cutting effects for materials like 6061 aluminum and PC plastic. Key trends to watch include:
In summary, understanding the cutting effects of 6061 aluminum and transparent PC plastic in CNC machining is essential for manufacturers aiming to improve product quality, optimize costs, and maintain competitive advantages.
Through an in-depth analysis of material properties, cutting parameter selection, adaptive machining strategies, and emerging technologies, businesses can enhance their machining processes to produce high-quality components that meet critical industry standards.
As CNC machining continues to advance, keeping an eye on these trends and techniques will prove invaluable. Paying attention to the nuances of machining different material types ensures not just operational efficiency but also the long-term sustainability and success of manufacturing in your industry.
Reflecting on the critical importance of optimizing cutting effects will empower readers to adopt best practices that contribute to their machining efficacy in innovating and creating high-quality products for a competitive marketplace.