Did you know that the aerospace industry has seen an increase in fuel efficiency of up to 20% by utilizing lightweight materials? As industries continue to push the boundaries of innovation, the discussion around lightweight materials in CNC machining has never been more pertinent. Whether you’re a manufacturer, engineer, or someone intrigued by machinery, understanding the implications of using lightweight materials could alter the trajectory of your projects.
In this blog, we will delve into the trade-offs associated with using lightweight materials for CNC machining. We will uncover the benefits, drawbacks, and the critical evaluation process that can help you make informed decisions. By the end of this article, you’ll be equipped with the knowledge needed to evaluate the effectiveness of incorporating lightweight materials into your projects.
Section 1: Understanding CNC Machining and Lightweight Materials
1.1 What is CNC Machining?
Computer Numerical Control (CNC) machining is a subtractive manufacturing process that uses computer-controlled equipment to create complex parts and components. From milling, turning, and laser cutting to 3D printing, CNC machining is a versatile capability deployed in various industries such as aerospace, automotive, and medical devices.
1.2 The Rise of Lightweight Materials
As the demand for efficiency increases, the quest for lightweight materials—such as aluminum alloys, carbon fiber, and titanium—has surged. These materials offer excellent strength-to-weight ratios and can contribute significantly to the overall performance and efficiency of the finished product.
Section 2: Benefits of Using Lightweight Materials in CNC Machining
2.1 Improved Efficiency
One of the most compelling reasons to use lightweight materials is the inherent efficiency they bring to various applications. The reduction in weight can lead to less energy expenditure in operations, especially in industries such as aerospace and automotive. For example, lighter components require less fuel and lead to lower operational costs.
2.2 Enhanced Performance
Lightweight materials often feature superior mechanical properties compared to traditional materials, making them an attractive option. Components made from materials such as carbon fiber can be engineered to withstand high stress without adding significant weight.
2.3 Design Flexibility
The malleability of lightweight materials allows for intricate designs that were previously impossible with heavier materials. This flexibility in design translates into more innovative products and allows manufacturers to explore new avenues in design optimization.
Section 3: Potential Drawbacks of Lightweight Materials
3.1 Cost Considerations
One of the most significant trade-offs when using lightweight materials is cost. Materials like titanium and carbon fiber tend to be more expensive than conventional materials. Therefore, the initial investment may not be justifiable in every application.
3.2 Durability and Fatigue Resistance
While lightweight materials have impressive strength properties, they can sometimes be more susceptible to fatigue over time. In critical applications where component life is essential, this trade-off can lead to serious considerations regarding safety and reliability.
3.3 Machining Challenges
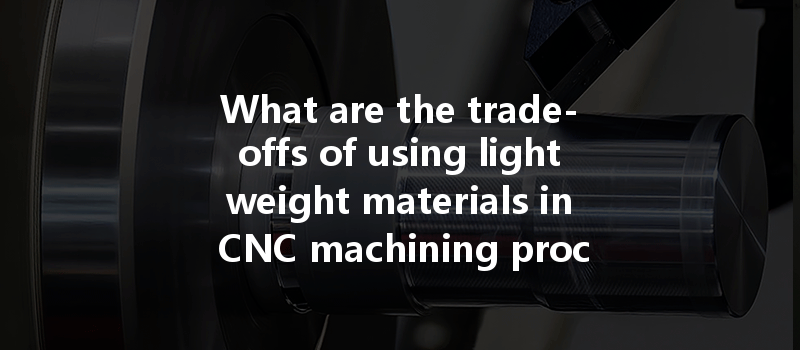
CNC machining lightweight materials may involve difficulties such as tool wear and tear, as well as challenges in achieving the desired surface finish. Specifically, materials like carbon fiber can create challenges due to their abrasive nature, necessitating specialized tooling.
Section 4: Evaluating the Trade-offs
4.1 Defining Application Requirements
Before any decisions can be made, it’s vital to define the specific requirements of your application. Factors such as load-bearing capacity, environmental conditions, and lifespan will influence your material choice. For instance, in aerospace applications, weight reduction is a priority, while in heavy machinery, durability may take precedence.
4.2 Conducting a Cost-Benefit Analysis
A thorough cost-benefit analysis can illuminate whether the advantages of lightweight materials outweigh the drawbacks. Calculate the potential savings due to reduced fuel consumption or increased efficiency and compare them with the additional costs of using lighter materials.
4.3 Prototyping and Testing
Creating prototypes using different materials can provide valuable insights. Testing under real-world conditions will allow you to assess performance, durability, and feasibility, making it easier to make informed decisions based on empirical evidence.
Section 5: Best Practices for Implementing Lightweight Materials
5.1 Selecting the Correct Material
Choosing the right lightweight material is critical. Each material comes with its unique properties that may affect performance. Research and consult experts who can provide guidance on selecting materials such as aluminum alloys versus traditional steel, or the use of carbon composites.
5.2 Pay Attention to Machining Parameters
Adjusting cutting speeds, feed rates, and tooling setup specifically for lightweight materials can affect the quality and efficiency of the machining process. Operators should be trained to handle these materials for optimal results.
5.3 Implementing Technology for Precision
Investing in advanced CNC technologies such as high-speed machining and adaptive machining can improve the outcome when working with lightweight materials. These technologies can enhance precision and reduce waste, leading to higher productivity.
The trade-offs of using lightweight materials in CNC machining are multifaceted. While the advantages—ranging from improved efficiency to enhanced performance—are compelling, it’s essential to weigh these against potential drawbacks, including cost and durability concerns.
As industries continually seek to innovate, understanding the right balance between material selection and manufacturing processes is crucial. In this blog, we explored various aspects that can influence your decision-making process, from the engineering properties of materials to best practices for implementation.
By considering these factors, you position yourself not just as a participant in the manufacturing industry, but as a forward-thinking leader poised to leverage materials that push the boundaries of what’s possible. The implications of this knowledge extend beyond just cost or efficiency—they fundamentally shape the future of manufacturing.
So, as you reflect on this blog, remember: the choices you make regarding lightweight materials can significantly influence your projects’ success and sustainability. Embrace the knowledge you’ve gained and make informed decisions as you navigate the ever-evolving landscape of CNC machining.