Did you know that brass is not only one of the most versatile metals for manufacturing, but it also has a unique property: the more you polished brass, the more of its natural properties you enhance? This characteristic makes brass exceptionally suitable for various applications, particularly in industries like electronics, plumbing, and aerospace. In the world of engineering, achieving high precision in CNC (Computer Numerical Control) machining of brass components can significantly impact functionality and performance.
As industries increasingly turn to CNC machining to produce high-precision brass parts, understanding the technical requirements becomes imperative. This blog delves deep into the technical specifications, methodologies, tools, and best practices needed to successfully CNC machine brass parts that meet stringent quality standards.
Whether you are a manufacturer looking to optimize your machining processes or a student aiming to grasp advanced manufacturing techniques, this comprehensive guide will equip you with the insights necessary to achieve impeccable results in CNC machining of brass.
What Makes Brass Unique?
Before diving into the technical requirements, it’s essential to understand why brass is an ideal choice for CNC machining.
Key Technical Requirements for CNC Machining Brass
To effectively CNC machine high-precision brass parts, here are the key technical requirements to consider:
Choosing the right grade of brass is crucial. Common types include:
CNC Machine Selection: The CNC machine must be capable of fine tolerances. Look for machines that offer:
Fixture Design: Proper fixtures ensure that the brass parts remain stable during the cutting process. Consider using:
Choosing the right cutting tools is critical for machining brass:
Setting the right cutting parameters can dramatically affect the quality of the finished part. These include:
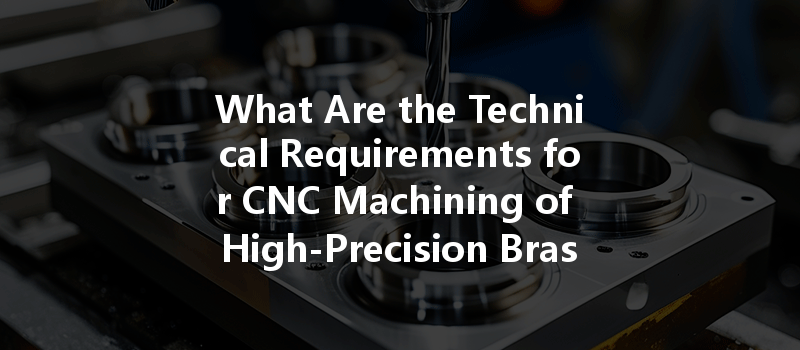
Fluid use is crucial in brass machining for cooling and lubrication:
Developing efficient machining strategies can lead to better efficiency:
Implementing robust inspection processes ensures that machined parts meet specifications:
Understanding potential problems can significantly save time and cost:
In-Depth Case Study: CNC Machining of a Brass Valve
Problem Identification
A client required a series of brass valves with high precision to be utilized in hydraulic systems. The valves faced issues of leakage due to imprecise machining operations.
Approach
Results
Upon completing the CNC machining process, extensive testing of the brass valves demonstrated a reduction in leakage by 95%, while achieving a superior surface finish, leading to successful acceptance by the client.
Understanding the technical requirements for CNC machining of high-precision brass parts is essential for manufacturers striving for excellence in quality, efficiency, and cost-effectiveness. Whether it involves selecting the right material, machine setup, tooling, or cutting parameters, each step plays a crucial role in achieving the desired outcomes.
By incorporating the specified practices into machining operations, manufacturers can deliver superior products, reduce waste, and ensure customer satisfaction. This comprehensive approach can also open pathways for innovation and improvements in brass machining technologies.
In today’s competitive landscape, staying informed about the nuances of CNC machining can set you apart. By embracing these methodologies, you pave the way toward excellence in manufacturing high-precision brass parts. Remember, excellence is not merely a goal but a journey — and it begins with understanding the critical requirements at every step of the machining process.