Did you know that the global automotive industry is projected to exceed $3 trillion in market value by 2025? The complexity behind this robust sector lies not only in design and manufacturing but also in the precision needed to create intricate components that meet stringent safety and performance standards. Central to this precision is Computer Numerical Control (CNC) machining, a technology that revolutionized manufacturing. However, as beneficial as CNC machining is, the automotive industry faces several technical difficulties when applying this technology.
In this blog, we will delve into the intricacies of CNC machining in the automotive sector, examining both the challenges and solutions, ultimately offering a comprehensive understanding that will help stakeholders navigate this critical aspect of manufacturing.
—
Understanding CNC Machining
CNC machining refers to a computer-controlled manufacturing process that utilizes various tools, such as drill bits, lathes, and mills, to create precise parts from raw materials. In the automotive industry, CNC machining is crucial for fabricating components like engine blocks, gearboxes, and suspension parts.
While its capabilities are vast, the transition to CNC machining in automotive production has not been without its obstacles. Factors such as material selection, precision requirements, and investment costs can create complications. The following sections will explore these challenges in detail.
—
Technical Challenges of CNC Machining in Automotive Manufacturing
Automotive parts must adhere to stringent precision and tolerance standards. Even a minor deviation can lead to catastrophic failures, affecting vehicle safety and performance. Common challenges related to precision include:
Solution: Adopting advanced sensor technologies for real-time monitoring and utilizing adaptive control systems can improve precision significantly. These systems adjust the operation of the CNC machine based on the feedback received from the machining process itself.
The choice of materials has a significant influence on the CNC machining process. The automotive industry often deals with high-strength materials like steel and titanium, which can be challenging to machine.
Solution: Investing in cutting-edge tools specifically designed for hard materials can alleviate some of these issues. Additionally, pre-treating materials through processes like annealing may improve their machinability.
As automotive designs evolve, the need for more complex geometries increases. Many modern cars feature intricate components that require advanced machining capabilities.
Solution: Utilizing 5-axis CNC machines and advanced CAD/CAM software can enable manufacturers to tackle complex designs more efficiently, thereby reducing cycle times and improving accuracy.
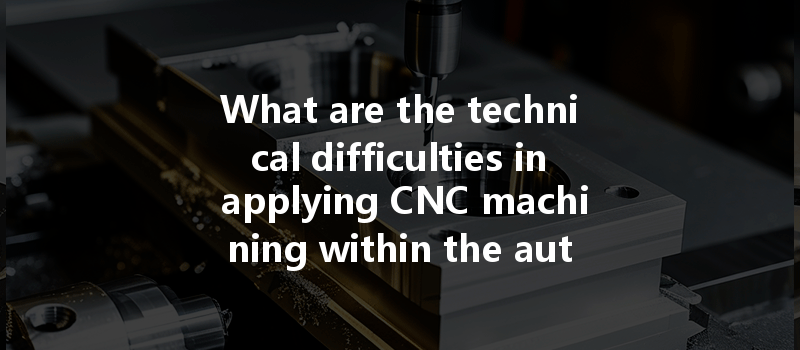
While CNC machining provides precision, it can often fall short in terms of speed when compared to traditional methods, especially in high-volume production environments.
Solution: Streamlining workflows through lean manufacturing principles and efficient scheduling can reduce downtime. Investing in faster machine tools and exploring automation with robotics can also help improve overall efficiency.
Implementing CNC machining often requires substantial capital investment, which can be a barrier for smaller manufacturers.
Solution: Emphasizing planned maintenance schedules and predictive maintenance strategies can help mitigate unexpected downtime. Additionally, considering leasing options or collaborating with CNC servicing specialists may be cost-effective alternatives for smaller companies.
Transitioning to CNC machining necessitates skilled personnel who understand both the technology and machining principles.
Solution: Establishing comprehensive training programs that emphasize both theoretical knowledge and practical experience will elevate the skill level of the workforce. Embracing partnerships with technical schools can also support skill development.
—
Future Trends and Technological Innovations
As the automotive industry continually evolves, so too will the demands placed on CNC machining. Upcoming trends that may influence this technology include:
—
Navigating the technical difficulties of CNC machining in the automotive industry is no small feat. The challenges related to precision, material selection, complex geometries, cycle times, costs, and workforce training are significant, but they are not insurmountable. By investing in cutting-edge technology, advanced training methods, and efficient workflows, manufacturers can turn these challenges into opportunities for enhanced productivity and performance.
Ultimately, understanding these intricacies is essential for any stakeholder involved in the automotive sector. As the industry evolves, adapting to these realities will not only ensure your competitive edge but also contribute to the overall safety and reliability of vehicles in today’s market. The discussion about improving CNC machining is not just about technology; it is about engineering a safer and more efficient future for the automotive world.
—