*
Did you know that approximately 70% of CNC machining operations are followed by some form of post-processing? This statistic highlights the crucial role that post-processing plays in ensuring the final product meets the desired specifications for quality, precision, and performance. For those involved in the manufacturing and engineering sectors, understanding the various post-processing techniques employed after CNC machining can be the key to delivering high-quality parts that satisfy customer needs.
In this blog, we will explore the comprehensive realm of post-processing methods used in CNC precision machining, detailing techniques, benefits, and critical considerations along the way. From surface finishing to assembly and inspection, this deep dive will equip you with essential knowledge to optimize your CNC machining processes.
—
What is CNC Precision Machining?
CNC (Computer Numerical Control) precision machining is an advanced manufacturing process that employs computer-controlled machines to produce intricate components with high levels of accuracy. By utilizing materials like metals, plastics, and composites, CNC machining can create parts for a wide range of industries, including aerospace, automotive, medical devices, and electronics.
However, while CNC machining offers exceptional precision, it often isn’t the final word in achieving optimal part quality. That’s where post-processing comes into play.
The Importance of Post-Processing
The term “post-processing” refers to the subsequent steps taken after the primary CNC machining process. Its significance cannot be overstated as it directly influences the component’s appearance, functionality, and compliance with industry standards. The main objectives of post-processing include:
By effectively employing post-processing techniques, manufacturers can achieve superior product quality while also enhancing durability, aesthetic appeal, and performance.
—
Common Post-Processing Techniques in CNC Machining
Now that we’ve established the importance of post-processing, let’s delve into some common techniques that can be employed after CNC precision machining.
Surface finishing is one of the most critical forms of post-processing. The goal here is to improve the surface texture and quality of CNC machined parts. Various methods can achieve this, including:
Benefits: Improved surface finish contributes to both functional and aesthetic elements of a part, thus enhancing market appeal.
Heat treatment is another vital post-processing step. This involves altering the mechanical properties of a part through controlled heating and cooling processes. Common heat treatment methods include:
Benefits: Heat treatment can significantly enhance the strength, hardness, and durability of parts, making them suitable for demanding applications.
Post-processing may also include the assembly of individual components into a larger system or product. This may involve tasks such as:
Benefits: Proper assembly ensures the functionality and performance of the final product, impacting its overall success in the market.
Quality control is a crucial step in the post-processing sequence to ensure that all components meet the required standards. Key practices include:
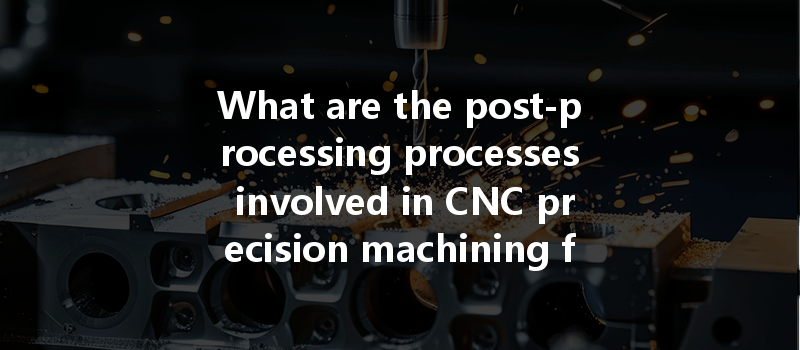
Benefits: Quality control prevents defects and ensures that only high-quality parts are delivered, thus maintaining customer satisfaction.
Cleaning and deburring are essential for the preparation of parts for further processing or final use. This involves:
Benefits: Clean and deburred parts enhance the visual aesthetics and reduce potential failure points, improving overall product reliability.
—
Advanced Post-Processing Techniques
In addition to the common post-processing techniques mentioned earlier, there is a suite of advanced methodologies employed to meet specific applications or industry standards.
In some cases, post-processing can involve additive techniques to enhance features or add elements. For example, 3D printing may be used to add complex geometries that are difficult to achieve with traditional machining methods.
Benefits: This hybrid approach can optimize material usage, reduce weight, and achieve intricate designs.
Laser technology can play a significant role in post-processing by executing applications such as:
Benefits: Laser-based techniques offer precision and minimal intrusion, making them suitable for high-value components.
This method includes shaping materials using hydraulic pressure for unique geometries. Hydroforming allows the production of complex shapes that can reduce welds and assembly requirements.
Benefits: The seamless nature of hydroforming leads to enhanced strength and less material waste.
—
Challenges in Post-Processing and Solutions
While post-processing techniques are essential for high-quality manufacturing, they can present challenges that require careful management. Here are some common challenges and potential solutions.
Post-processing can add lead time to the production process, potentially affecting delivery schedules.
Solution: Effective planning and scheduling, combined with integrated workflows that minimize downtime, can help address time conflicts.
Post-processing can incur additional costs, which may impact the overall budget of a project.
Solution: Evaluating the necessity of each process and prioritizing those that provide the greatest value can help manage costs effectively.
Different materials require unique post-processing techniques, which can complicate workflow.
Solution*: Standardizing post-processing methods for similar materials ensures consistency and efficiency while also training operators on material-specific techniques.
—
In conclusion, post-processing is a fundamental aspect of CNC precision machining that greatly impacts the quality, performance, and aesthetic appeal of machined parts. By mastering various techniques such as surface finishing, heat treatment, assembly, quality control, and advanced methodologies, manufacturers can deliver high-quality components tailored to specific industry standards and customer expectations.
Understanding the post-processing landscape not only provides insight into optimizing manufacturing processes but also elevates the overall brand by ensuring product reliability and innovation. As technologies and techniques continue to evolve, staying abreast of post-processing advancements will be key to maintaining a competitive edge in the fast-paced manufacturing world.
This blog serves to remind both newcomers and seasoned professionals about the importance of emphasizing post-processing to enhance the outcomes of CNC precision machining. When high-quality parts are your goal, post-processing should not be an afterthought but rather an integral part of your machining strategy. It’s a crucial investment in quality, functionality, and, ultimately, customer satisfaction.