Did you know that surface treatments can account for up to 30% of the total cost in CNC machining processes? As industries seek to improve the performance, durability, and aesthetic of components, understanding the underlying costs associated with these treatments becomes paramount for manufacturers and buyers alike. But what exactly drives these costs, and how can you navigate them to optimize your production process? In this comprehensive guide, we’ll dissect and analyze the key components of CNC machining surface treatment costs and offer solutions for cost efficiency.
—
In the fast-paced world of manufacturing, every penny counts. With competition growing fiercer and margins tightening, businesses can no longer afford to overlook any aspect of their production costs. This is especially true for surface treatments in CNC machining. As critical processes that enhance the usability and lifespan of components, understanding the costs associated with surface treatments is essential for making informed decisions that can lead to substantial savings.
CNC machining, or Computer Numerical Control machining, is a manufacturing process that utilizes programmable software and precision machinery to control the movement of tools and equipment. This high-tech approach allows manufacturers to create intricate parts from various materials with unprecedented accuracy, reducing human error and maximizing efficiency. When combined with surface treatments, CNC machining can significantly improve the functionality and appearance of parts.
Surface treatments serve multiple purposes in CNC machining. They improve corrosion resistance, enhance wear resistance, optimize electrical conductivity, and provide an aesthetically pleasing finish. Common treatments include anodizing, plating, coating, and polishing, each with unique benefits and applications. Due to their critical role in component performance and longevity, understanding the costs involved in these treatments is indispensable for buyers and manufacturers.
The total cost of surface treatments in CNC machining can often be broken down into several key components:
4.1 Labor Costs
Labor costs encompass the wages and benefits paid to technicians and operators who perform surface treatment processes. This includes skilled labor needed for specific treatments, overhead for management, and any training required for specialized treatment techniques. Labor will vary significantly depending on the complexity of the materials being treated and the experience level of employees.
4.2 Material Costs
The materials required for surface treatments can include chemicals (for plating and coating), metals (for anodizing), and consumables (like abrasives for polishing). These costs fluctuate based on market prices, material availability, and the specific requirements of the treatment process.
4.3 Equipment Costs
The machinery necessary for surface treatments can be a significant capital investment. Equipment prices vary based on capabilities, including the size of the components being treated and the degree of automation. Depreciation, maintenance, and repair costs for this equipment also contribute to the overall expense.
4.4 Operational Overheads
Operational overheads include expenses related to facilities, utilities, safety measures, and any required permits. These costs are typically shared across all production processes but should be calculated against surface treatment activities to understand the true cost.
4.5 Quality Assurance
Quality assurance involves inspections, testing, and certifications needed to ensure that surface treatments meet specified standards. This may involve additional labor costs, materials for testing, and the potential for rework if components fail to meet quality criteria.
Certain variables can influence the overall cost of surface treatments, including:
5.1 Material Type
Different materials require specific treatments, and the costs can dramatically differ depending on the substrate. For example, stainless steel often requires different treatments than aluminum or plastics, leading to variances in pricing.
5.2 Treatment Complexity
More complex treatments, such as multi-layer coatings and special finishes, will generally have higher associated costs due to increased labor and time requirements.
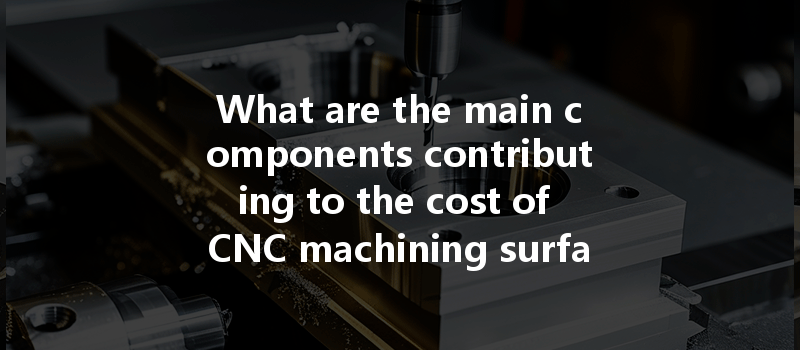
5.3 Production Volume
Economies of scale often play a critical role—larger production runs can significantly reduce costs per unit due to minimized setup times and bulk purchasing of materials.
5.4 Geographical Location
The cost of labor and materials can differ based on the geographical region where machining and treatments are performed. Certain areas may have higher costs due to local regulations or availability issues.
Let’s examine some of the most common surface treatment processes employed in CNC machining and their respective cost factors.
6.1 Anodizing
Anodizing is an electrochemical process that converts the metal surface into a decorative, durable, corrosion-resistant finish. The costs are influenced by the type of anodizing (e.g. sulfuric or hard anodizing), the size of the batch, and the raw material prices.
6.2 Plating
Plating involves depositing a layer of metal onto a substrate to enhance properties such as conductivity and resistance to wear. The type of plating—such as electroplating or electroless plating—determines the complexity and costs of labor and materials used.
6.3 Coating
Coatings, like powder coating or liquid painting, add a protective layer to parts. The costs depend on the application method, materials used, and post-treatment processes such as curing.
6.4 Shot Peening
This mechanical process enhances fatigue strength by bombarding the surface of components with small balls. While it provides significant performance benefits, the machinery and associated wear materials can be quite costly.
6.5 Polishing
Polishing is employed to achieve a high-gloss finish and is often combined with other treatments. Labor costs for skilled technicians to achieve the desired finish can be substantial, making careful planning essential.
To better illustrate the aforementioned points, let’s provide a few brief case studies showcasing cost breakdowns for different surface treatments.
Case Study 1: Aluminum Anodizing for Aerospace Components
A manufacturer processes 1,000 small aluminum parts intended for aerospace applications. The breakdown is as follows:
Cost per part: $5
Case Study 2: Hard Chrome Plating for Mechanical Components
A manufacturer orders hard chrome plating for 500 mechanical components. The breakdown reveals different cost structures:
Cost per part: $12
Understanding these examples helps clarify how different processes impact overall costs and provide context for financial planning.
Now that we understand the components and factors, here are actionable strategies to minimize surface treatment costs:
8.1 Leveraging Technology
Utilizing advanced CNC programming and equipment automation can reduce labor costs and enhance precision, leading to less waste and rework.
8.2 Bulk Scheduling
By scheduling treatments in bulk rather than sporadic small batches, businesses can benefit from reduced material and setup costs.
8.3 Supplier Negotiation
Building strong relationships and negotiating with suppliers for better rates on bulk material purchases can decrease the overall costs of treatments.
8.4 Material Optimization
Choosing materials that require less expensive treatments or alternative coatings can lead to significant savings in the long run. Analyzing the cost versus performance of materials is crucial.
As technology evolves, so too do the methods and materials used in surface treatments. Key trends that may influence costs in the coming years include:
Understanding the components of CNC machining surface treatment costs is crucial for manufacturers aiming to maintain competitive pricing and high-quality standards. By dissecting labor, material, equipment, and quality assurance costs, companies can navigate potential pitfalls in budgeting and make informed decisions that optimize production processes. Moreover, differentiating factors like material type, treatment complexity, and production volume play significant roles in shaping these costs.
As you reflect on the complexities of surface treatments in CNC machining, consider why this knowledge is vital for your operations; it allows for better cost estimation, planning, and ultimately provides a competitive edge in a competitive manufacturing landscape. By implementing the strategies mentioned and staying updated on future trends, you can effectively manage and possibly reduce your surface treatment expenses, driving greater profitability and success in your CNC operations.
This blog serves as a valuable reference point in your journey toward optimized manufacturing processes. Remember: informed choices lead to efficient production, lower costs, and enhanced product quality, making it a worth-pondering topic for anyone involved in the machining industry.