Did you know that according to industry reports, laser cutting contributes to an estimated 40% of the total market for precision metal fabrication? As technological advancements drive demand for higher precision and efficiency in production processes, businesses are increasingly exploring different cutting methods available in CNC machining. Among these methods, laser cutting and plasma cutting stand out as two of the most widely employed techniques. But what exactly are the key performance differences between these two approaches, and how can each be leveraged effectively to meet specific manufacturing needs?
This blog aims to dissect the intricacies of both laser cutting and plasma cutting, providing a comprehensive analysis of their performance parameters, applications, and potential benefits. By exploring each method in detail, we will help you make informed decisions on which technique suits your CNC machining projects best.
Chapter 1: Understanding CNC Machining Cutting Methods
Before diving into the performance differences between laser and plasma cutting, it’s essential to grasp what CNC machining entails. CNC (Computer Numerical Control) machining is a manufacturing process that uses pre-programmed computer software to control the movement of factory tools and machinery. It allows for greater precision, accuracy, and automated performance in cutting materials compared to manual methods.
Key Cuts in CNC Machining:
Chapter 2: Laser Cutting
2.1 How Laser Cutting Works
Laser cutting employs a high-powered laser beam to melt, burn, or vaporize the material being cut. The laser beam is directed onto the material using optics and a CNC system. This approach offers incredible precision, making laser cutting ideal for intricate designs.
2.2 Key Advantages of Laser Cutting
a. Precision and Detail: Laser cutting delivers remarkably high precision levels, with the capability of achieving a kerf as narrow as 0.1 mm.
b. Versatility: It can cut through a wide array of materials, including metals, plastics, fabrics, and even ceramics, expanding its application in various industries.
c. Clean Cuts: The process generates minimal thermal distortion, resulting in smooth edges with little to no post-processing required.
d. Computer Control: The CNC technology allows for complex shapes and designs that would be difficult to replicate using traditional cutting methods.
2.3 Applications of Laser Cutting
Chapter 3: Plasma Cutting
3.1 Understanding Plasma Cutting
Plasma cutting utilizes a high-velocity jet of ionized gas (plasma) to melt the material away. The surrounding air helps cool the molten material, facilitating effluent elimination from the cutting path.
3.2 Key Advantages of Plasma Cutting
a. Speed: Plasma cutting is significantly faster than laser cutting, particularly for thicker materials, which can be beneficial in high-volume production environments.
b. Thicker Material Capability: It readily cuts materials up to several inches thick, making it suitable for heavy-duty applications.
c. Lower Initial Cost: Plasma cutting systems generally have a lower setup cost compared to laser systems, making them attractive for smaller operations.
3.3 Applications of Plasma Cutting
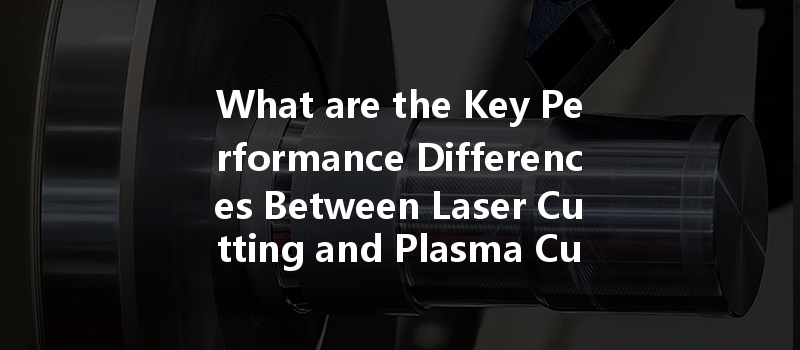
Chapter 4: Performance Comparison Between Laser Cutting and Plasma Cutting
4.1 Precision
Precision is arguably one of the most significant factors when comparing laser and plasma cutting. Here, laser cutting excels with its ability to produce exceptionally detailed cuts as fine as 0.1 mm. In contrast, plasma cutting’s kerf can be wider, usually ranging from 1 mm to 5 mm, making it less suitable for detailed work.
4.2 Speed
When assessing speed, plasma cutting takes the lead, especially when dealing with thicker materials. It can cut through 1-inch steel at rates that are often two to three times faster than lasers. However, this speed does come at a cost to precision.
4.3 Material Compatibility
While both methods can cut various metals, laser cutting shines in handling thin materials like stainless steel, aluminum, and even non-metals like acrylic and wood. Plasma cutting, however, is adept at slicing through thick ferrous materials, such as carbon steel.
4.4 Cost Efficiency
Initial costs for laser cutting systems tend to be higher, but they offer savings on labor and material through precision cuts and reduced waste. Plasma systems have lower upfront costs but may require more extensive labor as the need for post-processing can increase due to the wider kerf and rougher edges associated with plasma cuts.
4.5 Thermal Distortion
Laser cutting produces minimal thermal distortion, resulting in a higher quality cut with less cleanup needed afterward. Plasma cutting generally induces more heat into the material, leading to larger heat-affected zones, which can necessitate additional finishing processes.
Chapter 5: Choosing the Right Cutting Method for Your Application
Understanding the differences between laser and plasma cutting empowers businesses to select the right method for their specific applications. Factors to consider include:
Chapter 6: Future Trends in Laser and Plasma Cutting Technologies
As technology advances, both laser and plasma cutting methods are evolving to enhance performance and expand capabilities.
6.1 Advancements in Laser Cutting Technology
Developments in fiber laser technology have revolutionized laser cutting by offering higher power levels and efficiency. Fiber lasers have a shorter wavelength that enables better absorption in metals, resulting in faster cutting speeds, especially for reflective materials.
6.2 Plasma Cutting Innovations
The introduction of High-Definition (HD) plasma systems provides better cut quality and increased precision. These systems utilize advanced cooling and gas control enhancements that reduce the heat-affected zones, similar to laser cutting in some aspects.
In summary, both laser cutting and plasma cutting each possess unique advantages and distinct limitations that cater to various industries and applications. Laser cutting offers unparalleled precision and a clean finish, making it suitable for intricate designs on thin materials. On the other hand, plasma cutting shines in speed and thickness, making it ideal for heavy-duty metal fabrication.
Choosing the right cutting method hinges on a variety of factors, including material type, production volume, and budget constraints. As both technologies continue to evolve, staying informed on their capabilities and advancements will empower manufacturers to make strategic decisions that enhance productivity and product quality.
Remember, the choice between laser and plasma cutting isn’t just about comparing two methods; it’s about finding the right fit for your specific needs and challenges. By leveraging the appropriate technology, you will ensure the success and efficiency of your CNC machining processes in today’s competitive landscape.
As we move forward, keep evaluating your options and thinking critically about which cutting method aligns best with your operational goals. The choice you make today can ultimately shape the future of your manufacturing capabilities.