Did you know that POM (Polyoxymethylene), commonly known as acetal, has one of the highest strength-to-weight ratios among engineering plastics? This remarkable polymer is widely used in precision machining applications due to its mechanical properties, chemical resistance, and low friction characteristics. However, reducing cutting force during CNC machining of POM plastic becomes crucial to achieve optimal machining performance, extending tool life, and ensuring a high-quality surface finish.
In this comprehensive blog post, we will explore the key factors that influence cutting force in CNC machining POM plastic and provide a detailed solution to mitigate these challenges. From tool selection and cutting parameters to cooling systems and deburring techniques, we will delve deep into each aspect that contributes to the machining process.
Understanding POM Plastic
Before diving into the specific strategies for reducing cutting force, it’s essential to understand what POM plastic is and why it’s chosen for CNC machining.
POM is a thermoplastic with a high tensile strength and stiffness that exhibits superior dimensional stability. It finds application in industries like automotive, aerospace, and consumer goods, typically in gears, bearings, and various other precision components.
However, these advantageous properties also pose challenges when machining POM, particularly in terms of cutting force.
Impact of Cutting Force on CNC Machining
Cutting force is defined as the force required to remove material from a workpiece during the machining process. High cutting forces can lead to several issues, including:
Key Factors Affecting Cutting Force in CNC Machining POM Plastic
Now that we understand the implications of cutting forces, let’s explore the crucial factors that can be optimized for reducing these forces during CNC machining of POM plastic.
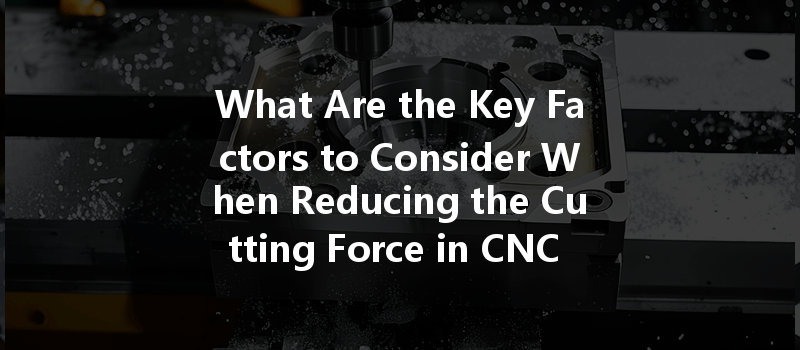
Step-by-Step Guide to Implementing Solutions
To effectively reduce cutting force while machining POM plastic, follow these consolidated steps:
Reducing cutting force during the CNC machining of POM plastic isn’t just about efficiency; it’s about maximizing the quality of the finished part while minimizing costs and prolonging tool life. By focusing on critical factors like tool selection, cutting parameters, machine rigidity, cooling strategies, and fixture design, manufacturers can effectively overcome the challenges posed by high cutting forces.
The solutions presented in this blog not only contribute to improved machining processes but also enhance overall productivity in manufacturing. It’s essential for businesses to keep these considerations in mind as they explore opportunities in machining POM and other plastics, where precision and quality are of utmost importance.
In the ever-evolving landscape of CNC machining, understanding the nuances of material properties and machining dynamics, specifically regarding POM plastic, remains crucial. The implications of these factors extend beyond immediate costs and efficiencies, affecting product quality, operational longevity, and competitive edge in the industry. Therefore, investing time and resources in learning and implementing these strategies will pay dividends in the long run.
Let’s prioritize reducing cutting force in CNC machining practices and drive innovation while maintaining the highest levels of precision and quality in plastic components.