CNC (Computer Numerical Control) machining has revolutionized the manufacturing sector, providing unparalleled precision, repeatability, and efficiency. However, selecting the appropriate CNC machining method for a specific material can be complex and requires a thorough understanding of various factors. As a leader in precision machining, YL Machining understands the intricacies involved in this decision-making process. In this article, we will explore the key factors to consider when choosing CNC machining for different materials, ensuring that your next project meets quality and performance expectations.
Material Characteristics
The mechanical properties of materials, such as strength and hardness, are fundamental in determining appropriate CNC machining techniques. Harder materials, such as titanium or certain alloys, require specialized tools and machining parameters to avoid damage to cutting tools and ensure accurate results. For softer materials like aluminum or certain plastics, standard machining methods may suffice.
For instance, materials like steel necessitate the use of carbide tools due to their hardness, while softer materials can often be machined with high-speed steel tools. Understanding the specific hardness and tensile strength of your material will enable you to select appropriate tools and cutting speeds to enhance efficiency and reduce tool wear.
The machinability of a material refers to how easily it can be machined, including its tendency to produce chips, its work hardening behavior, and how it reacts to heat during machining. Materials like copper and brass are known for their excellent machinability, offering cleaner chips and good surface finishes.
In contrast, materials such as stainless steel can be challenging to machine due to their tendency to work harden. Therefore, knowing the machinability rating of the materials under consideration can help optimize the machining process.
CNC Machining Techniques
Different materials require different cutting speeds and feed rates, which directly influence the quality of the finished product. Hard materials demand slower cutting speeds to prevent tool damage, while softer materials can often be machined at higher speeds.
Each material comes with its recommended cutting speed, typically expressed in surface feet per minute (SFM). For example, aluminum can generally be machined at speeds between 900 to 3,000 SFM, depending on the alloy and tooling used. It is crucial to consult machining handbooks or manufacturer specifications specific to the material to determine the optimal cutting speeds and feed rates for your project.
Tool selection is crucial for successful CNC machining. The type of tooling used can significantly impact both the quality of the finished piece and the efficiency of the machining process. Factors such as tool geometry, materials, coatings, and number of flutes should be taken into consideration.
For instance, carbide tools are often recommended for machining harder materials like steel and titanium due to their strength and longevity. Conversely, high-speed steel tools are commonly used for softer materials. Coatings on cutting tools, such as TiN (Titanium Nitride), can also enhance durability and performance by reducing friction and heat during machining.
Design Considerations
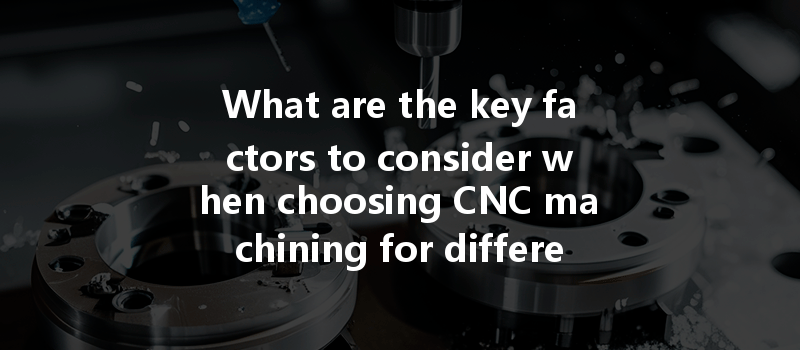
The required tolerances and surface finish are significant factors in determining machining methods. CNC machining can achieve high precision—typically within ±0.001 inches—depending on both the process and the tooling used.
For intricate designs or applications requiring tight tolerances, it’s vital to select CNC techniques that can achieve the desired specifications. Consider examining ANSI (American National Standards Institute) standards and ASME Geometric Dimensioning and Tolerancing (GD&T) principles to better understand the requirements for your project.
The complexity of the part being machined also plays a pivotal role in material selection. Intricate designs may benefit from materials that offer ease of machining without compromising strength. Additionally, certain materials may be less forgiving of design intricacies that require tight tolerances.
Materials like PEEK (Polyether Ether Ketone) provide excellent mechanical performance in complex geometries but require advanced machining techniques due to their thermal properties. Understanding the complexity of your design will help isolate the best materials and machining processes.
Economic Considerations
Material cost is an inevitable consideration in CNC machining. While higher-performing materials like titanium may produce superior results, they also come with increased costs, affecting the overall budget.
Balancing quality and cost is essential, as selecting high-end materials may not yield proportional performance improvements for every application. It’s important to conduct a cost-benefit analysis to determine which materials align with the project’s financial and functional goals.
Finally, the expected production volume significantly influences the choice of both material and machining technique. For low-volume runs or prototypes, it may be worthwhile to opt for materials that are less expensive and easier to machine. However, for high-volume production, material cost, machinability, and tooling wear become more critical in driving profitability.
For instance, while certain metals may offer superior performance, their cost may only be justified when produced in higher quantities. On the other hand, rapid prototyping with plastics may be more beneficial for low-volume runs.
Choosing the right CNC machining process for different materials requires a nuanced understanding of various technical, design, and economic considerations. By assessing material characteristics, selecting appropriate machining techniques, and taking into account tolerance requirements and production volumes, you can optimize your CNC machining process for superior quality and efficiency.
At YL Machining, we pride ourselves on our expertise in CNC machining for a wide range of materials. Our commitment to precision and quality ensures that every project we undertake is executed to the highest standards. If you have any questions about your next CNC machining project or need assistance with material selection, feel free to reach out to us for tailored support.
By understanding the key factors influencing CNC machining, you’ll be well-equipped to make informed decisions that enhance both the performance and cost-effectiveness of your manufacturing processes.