Did you know that steel is among the most recycled materials globally, with an estimated recycling rate of around 70%? This statistic underscores the importance of steel in various industries, particularly in manufacturing sectors where precision is paramount. Among stainless steel grades, 440C and 420 are popular choices, especially in CNC machining processes. But what sets them apart when it comes to machinability, and why does it matter? In this blog post, we will delve deeply into the differences in machinability between 440C and 420 stainless steel, examining it from a CNC machining perspective and exploring solutions for optimizing their use in manufacturing.
—
CNC machining has revolutionized the way we shape and manipulate metallic materials. It allows for precise, repeatable manufacturing processes that can produce intricate designs with a high level of accuracy. Stainless steels, known for their resistance to corrosion and excellent mechanical properties, have become indispensable materials in diverse sectors, from aerospace to medical devices.
Understanding the different grades of stainless steel is crucial for manufacturers, each with unique characteristics. 440C and 420 stainless steels are particularly noteworthy due to their applications in high-strength and wear-resistant components. Yet, choosing between them can be challenging without a firm grasp of their machinability.
2.1 Chemical Composition
The chemical compositions of 440C and 420 stainless steels play a significant role in their characteristics and machinability:
2.2 Physical Properties
Both grades exhibit excellent mechanical properties, but they vary significantly:
Understanding machinability involves assessing various factors that influence the ease of cutting and shaping a material:
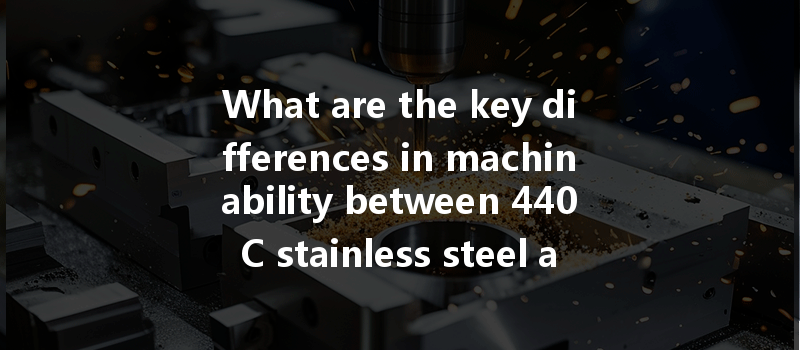
3.1 Cutting Tools and Techniques
The choice of cutting tools significantly impacts the machining process. Harder materials like 440C typically require cutting tools made from tougher materials, such as carbide or high-speed steel (HSS), to withstand wear. In contrast, softer materials like 420 can be machined effectively with standard HSS tools.
3.2 Machining Parameters
Machining parameters, including speed, feed, and depth of cut, also play a critical role. For instance, when machining 440C, lower feeds and slower speeds are generally used to mitigate tool wear. On the other hand, 420 can be machined at higher speed and feed rates due to its more forgiving nature.
When comparing the machinability of 440C and 420, it is essential to consider various parameters carefully.
4.1 Material Removal Rate
The material removal rate (MRR) refers to the volume of material removed per unit time. Typically, due to its hardness, 440C will exhibit a lower MRR compared to 420 under comparable conditions. Therefore, manufacturers aiming to optimize production time might favor 420 for bulk machining processes.
4.2 Surface Finish Quality
Surface finish is a critical consideration, especially in industries that require aesthetics or functionality, such as medical devices. Although both materials can achieve acceptable finishes, 440C may yield better results requiring less post-processing, given the right machining conditions.
4.3 Tool Wear Rates
As expected, tool wear rates will be higher when machining 440C due to its hardness. This can lead to increased costs and downtime for tool changes. Conversely, 420 typically exhibits lower wear rates, making it more cost-effective for high-volume applications.
The choice between 440C and 420 often depends on the application:
To optimize the CNC machining of both 440C and 420 stainless steels, consider the following best practices:
6.1 Choosing the Right Cutting Tools
Selecting appropriate cutting tools is crucial. For 440C, carbide tools are often the best choice, given their ability to handle high wear rates. For 420, HSS tools can suffice, allowing for higher material removal rates.
6.2 Optimizing Cutting Conditions
Machining parameters such as spindle speed and feed rate should be tailored. For 440C, slower speeds and lower feeds can help reduce heat generation and tool wear. Conversely, higher speeds and feeds are more applicable for 420 to maintain efficiency while still achieving quality results.
6.3 Tool Path Optimization
Effective tool path management using modern CNC programming techniques can significantly improve efficiency and surface finish. Utilizing CAM software can help identify optimal paths, reducing unnecessary movements and thus improving machining times for both materials.
In summary, understanding the differences in machinability between 440C and 420 stainless steel is crucial for manufacturers seeking efficiency and quality in their CNC machining processes.
Key Takeaways:
Recognizing these distinctions allows manufacturers to make informed decisions, enhancing production efficiency and product quality. Companies striving to maintain a competitive edge in today’s market should take this knowledge to heart, as it could prove pivotal in choosing the right stainless steel for their needs.
As you consider your next machining project, reflecting on these insights may well lead you to better choices—whether that’s opting for the durability of 440C or the machinability of
This blog serves a dual purpose: educating you on the nuanced disparities between these two stainless steel grades and emphasizing how critical material selection and machining practices are to successful manufacturing outcomes. The future of CNC machining lies not just in technology, but in understanding the materials we work with and how best to utilize them.