Did you know that as of 2021, the global market for additive manufacturing (3D printing) was projected to reach over $40 billion by 2024? In contrast, CNC machining, which has been an industry staple for decades, has also seen significant growth, but operates on fundamentally different principles. This raises an intriguing question: What is the difference between the impact of additive manufacturing and CNC machining on materials?
Understanding these differences is crucial for engineers, manufacturers, and anyone involved in production, as the choice between these methods can significantly affect product quality, cost, and time-to-market. In this blog post, we’ll delve deep into the comparison of these two cutting-edge manufacturing processes, examining their impacts on materials, design freedom, economics, and more.
Chapter 1: Understanding the Basics
1.1 What is Additive Manufacturing?
Additive manufacturing, colloquially known as 3D printing, refers to processes that create objects layer by layer from various materials based on digital models. Common materials used include plastics (like PLA and ABS), metals (like titanium and aluminum), ceramics, and even bio-materials.
1.2 What is CNC Machining?
CNC (Computer Numerical Control) machining is a subtractive manufacturing process that involves removing material from a solid block to create desired shapes and components. This is achieved using CNC machines that are programmed to automate the cutting, drilling, and milling processes.
Chapter 2: Material Impact
2.1 Material Properties in Additive Manufacturing
Strength and Durability
Additive manufacturing excels in producing complex geometries that are often not achievable through traditional methods. However, the overall material strength may not match that of machined components. The layer-by-layer approach may introduce weaknesses at the interfaces between layers, particularly in some polymers.
Thermal Properties
Additionally, thermal properties can vary dramatically between different additive manufacturing processes. For example, Fused Deposition Modeling (FDM) plastics have lower thermal stability compared to SLS (Selective Laser Sintering) nylon parts.
2.2 Material Properties in CNC Machining
Precision and Accuracy
CNC machines provide a high degree of precision and can achieve tight tolerances that are often necessary for high-performance applications. The material properties tend to be batch-consistent, enhancing reliability and reducing variability.
Physical Properties
The machining process tends to compact the material, improving its thermal and mechanical properties. It also offers a wide selection of materials that can be machined for specific applications, from metals like stainless steel to composites.
Chapter 3: Design Considerations
3.1 Design Freedom in Additive Manufacturing
One of the most significant advantages of additive manufacturing is its design freedom. Designers can create highly intricate parts with complex internal structures that cannot be manufactured using traditional methods.
Case Study: Aerospace Components
In aerospace, additive manufacturing is employed to produce lightweight components with complex geometries, contributing to fuel efficiency.
3.2 Design Limitations in CNC Machining
CNC machining is limited by certain design constraints. Features like undercuts, complex internal channels, and intricate designs may be challenging or impossible to execute.
Case Study: Precision Engineered Parts
However, CNC machining remains the preferred choice for producing precision components like engine blocks, where the dimensional accuracy is critical.
Chapter 4: Economic Impact
4.1 Cost Analysis of Additive Manufacturing
While the initial setup cost for additive manufacturing can be higher, the capability to produce low volumes without tooling often results in lower overall costs for prototypes and small batches.
Economies of Scale
However, the cost per unit significantly increases at scale, making it less economically viable for mass production.
4.2 Cost Analysis of CNC Machining
CNC machining, while requiring more investment for tool changes and precision setups, provides economies of scale. When producing large quantities, the cost per unit is often much lower compared to additive processes.
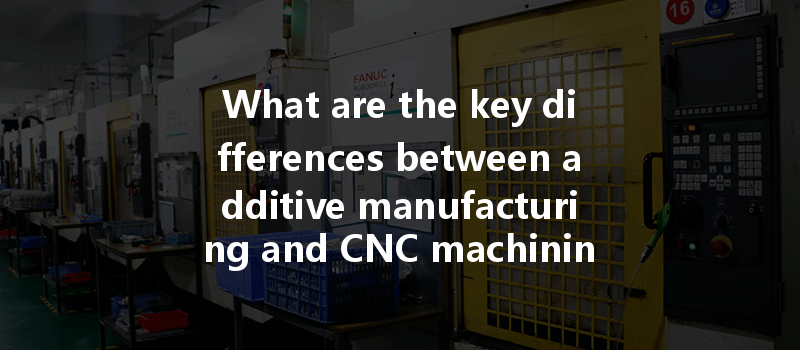
4.3 Time to Market Considerations
The speed of development and production also varies. Additive manufacturing can cut down on lead times, particularly when prototyping new designs. However, CNC machining typically enables faster production times for finalized designs.
Chapter 5: Sustainability
5.1 Environmental Impact of Additive Manufacturing
Additive manufacturing has the potential to minimize waste, as it only uses the materials necessary to create the part. Additionally, some methods allow for the use of recycled materials.
5.2 Challenges in CNC Machining
Conversely, CNC machining tends to produce significant material waste as material is removed to create the final part. The energy consumption and environmental impact of both processes also vary and are influenced by factors like machine efficiency and material choice.
Chapter 6: Industry Applications
6.1 Additive Manufacturing Applications
Additive manufacturing is widely used in industries like aerospace, healthcare (for prosthetic limbs and dental implants), and automotive (for small, lightweight components).
6.2 CNC Machining Applications
CNC machining is prevalent in industries that require high-precision parts, such as automotive (engine components), electronics (circuit board casings), and industrial machinery (custom fixtures).
Chapter 7: Comparing Pros and Cons
7.1 Advantages of Additive Manufacturing
7.2 Disadvantages of Additive Manufacturing
7.3 Advantages of CNC Machining
7.4 Disadvantages of CNC Machining
In summary, both additive manufacturing and CNC machining offer unique benefits and implications for material usage. Choosing between the two methods depends significantly on the specific needs of a project, including factors like design complexity, material requirements, production volume, and cost considerations.
As the manufacturing landscape continues to evolve, staying informed about these technologies is essential for industry professionals. Both additive and subtractive manufacturing processes play significant roles in shaping the future of production.
Understanding their impacts on materials allows for better decision-making, potentially leading to advancements in product quality, efficiency, and sustainability. As technology advances, we may see an even greater intersection of these methods, leading to innovative solutions that leverage the strengths of each. This blog not only serves as a comprehensive resource but also encourages thinkers in the field to reflect on the growing importance of production choices in fostering a more efficient future.