In the world of manufacturing where precision meets innovation, CNC machining stands out as a revolutionary approach to creating components with impeccable accuracy. At YL Machining, we take pride in being at the forefront of this technology, offering a wide range of services that not only meet but exceed the industry standards. One crucial aspect of CNC machining that often gets overlooked is the importance of surface treatment processes. These processes significantly enhance the performance, durability, and aesthetics of machined parts.
In this article, we’ll dive deep into the various CNC surface treatment processes available at YL Machining, elucidating their benefits, applications, and selecting the right process for your needs. This guide aims to equip you with the knowledge necessary to make informed decisions, whether you are an engineer, a product designer, or simply an enthusiast of advanced manufacturing.
Join us as we embark on this journey through the intricacies of CNC surface treatment technologies and discover how YL Machining can partner with you to achieve excellence in your projects.
—
CNC surface treatment refers to processes applied to the surface of a machined component to improve its properties, such as corrosion resistance, wear resistance, appearance, and surface finish. These treatments are essential to enhance the longevity and performance of parts used in diverse applications like aerospace, automotive, medical devices, and electronics.
2.1 Enhancing Durability
One of the primary reasons for surface treatment is to enhance the durability of components. Materials like metals can corrode or wear under harsh operating conditions. Surface treatments create barriers preventing environmental damage, thereby extending the lifespan of the part.
2.2 Improving Aesthetics
The visual appeal of components is vital, especially in consumer-facing industries. Surface treatments can enhance the appearance of parts, providing a sleek, polished look that meets aesthetic expectations.
2.3 Increasing Functionality
Certain surface treatments improve the functionality of parts. For example, adding a layer of coating can influence electrical conductivity, thermal stability, or friction properties, which are essential characteristics for specialized applications.
YL Machining provides a comprehensive suite of CNC surface treatment processes, including but not limited to:
3.1 Anodizing
Definition: Anodizing is an electrolytic process that converts the metal surface into an aluminum oxide finish, enhancing corrosion resistance and surface hardness.
Applications:
Benefits:
3.2 Powder Coating
Definition: Powder coating involves applying a dry powder that is cured under heat to form a hard, protective coating.
Applications:
Benefits:
3.3 Electroplating
Definition: Electroplating is a process that uses electrical current to reduce dissolved metal cations, allowing them to form a thin coating on the surface of a component.
Applications:
Benefits:
3.4 Vapor Deposition (PVD & CVD)
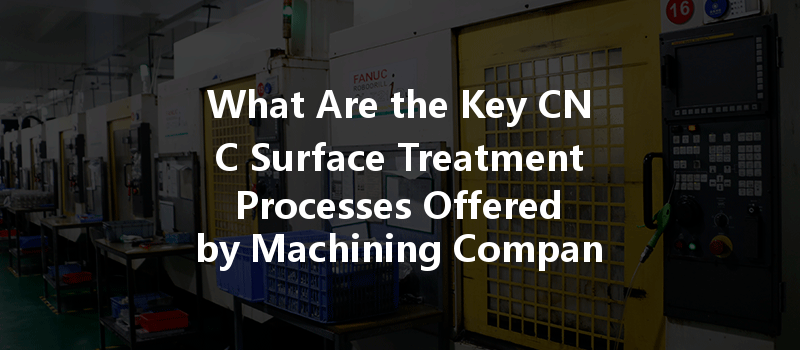
Definition: Physical Vapor Deposition (PVD) and Chemical Vapor Deposition (CVD) are processes that deposit a thin film of material onto a substrate, enhancing surface properties.
Applications:
Benefits:
3.5 Sandblasting
Definition: Sandblasting (or abrasive blasting) is a surface treatment that uses high-pressure abrasive materials to clean or texture a surface.
Applications:
Benefits:
3.6 Passivation
Definition: Passivation is a chemical treatment process that enhances the corrosion resistance of metals, particularly stainless steel, by removing free iron and creating a protective oxide layer.
Applications:
Benefits:
Choosing the right surface treatment process depends on a variety of factors, such as:
4.1 Material Type
Different materials respond uniquely to surface treatments. For example, aluminum parts are best suited for anodizing, while steel components may require electroplating or passivation.
4.2 Desired Properties
What do you need from your component? If your focus is on corrosion resistance, anodizing or passivation may be ideal. If aesthetics are critical, powder coating or electroplating could be the best choices.
4.3 Application Environment
Consider the environment where the part will be used. For parts exposed to harsh conditions, protective coatings like PVD or CVD may be more appropriate, while parts in controlled environments may prioritize cost-effectiveness.
At YL Machining, we emphasize the importance of quality control throughout the surface treatment process. Each batch undergoes rigorous testing to ensure conformity to specifications. This includes:
Surface treatment processes are invaluable in enhancing the properties and performance of CNC machined components. At YL Machining, we pride ourselves on offering an extensive array of surface treatment options tailored to meet the unique needs of our clients. From anodizing to powder coating, our processes are designed to ensure the highest quality and durability of components across various industries.
As you consider your next project, remember the significant impact surface treatments can have on your components. If you have any questions or need further assistance, our expert team at YL Machining is here to guide you through every step of the process. Together, we can create solutions that elevate your products to new heights of excellence.
—
Feel free to adjust the content to align with desired tone and audience while ensuring it retains a professional and informative nature.