Did you know that approximately 75% of product development leaders believe that rapid prototyping significantly shortens the time to market? In today’s fast-paced manufacturing world, the ability to produce high-quality prototypes quickly and accurately is more crucial than ever. Among the various techniques available, 5-axis CNC machining stands out as a powerhouse for creating intricate designs with precision and efficiency.
In this blog, we delve deep into the benefits, applications, and mechanics of 5-axis CNC machining. As the manufacturing landscape continues to evolve, understanding the capabilities of this highly advanced technology is essential for engineers, designers, and manufacturers alike. Whether you’re already familiar with CNC machining or just starting to explore its intricacies, this comprehensive guide will provide you with valuable insights into leveraging 5-axis CNC machining for superior prototype development.
What Is 5-Axis CNC Machining?
Before diving into the benefits, let’s clarify what 5-axis CNC machining entails. Unlike traditional 3-axis machines, which only move along the X, Y, and Z axes, 5-axis CNC machining can rotate around two additional axes. This incredible capability allows for unparalleled flexibility in terms of the angles and directions from which a tool can access the workpiece.
The Axes Explained
Panoramic access to the workpiece allows for more complex geometries and reduces the need for multiple set-ups, which minimizes errors and enhances efficiency.
The Key Benefits of 5-Axis CNC Machining
One of the most significant advantages of 5-axis CNC machining is its ability to achieve high precision with intricate designs. With the capability to angle the cutting tool from various directions, it significantly reduces the occurrence of tool wear and extends tool life. As a result, you can expect tighter tolerances, which is especially beneficial in industries such as aerospace, medical devices, and automotive, where precision is critical.
Traditional machining methods often require changing tool setups to access different sides of a workpiece. However, with 5-axis CNC machining, you can machine multiple sides of a part in a single setup. This not only saves time but also minimizes the risk of errors that can occur during repositioning. Manufacturers are increasingly finding that a single-phase setup reduces lead time and enhances production efficiency.
5-axis machines allow for complex shapes to be machined without the need for elaborate fixtures. Traditional machining often requires complex fixturing for securely holding the workpiece. With 5-axis machining, the machine’s configuration allows better access to challenging angles, reducing the need for multiple workholding setups.
5-axis CNC machining opens the door to capabilities that leave traditional 3-axis machines behind in design complexity. Intricate geometries, undercuts, and complex surface finishes become feasible in a single turn of the machine. This flexibility allows engineers and designers to push the boundaries of innovative designs, evolving the prototype development process to a cutting-edge standard.
The capability for continuous tool movement in 5-axis machining leads to smoother, more refined finishes. The ability to angle the cutting tool reduces the necessity for multiple passes at varying angles, contributing to a superior surface finish. This is particularly important in consumer-facing products, where aesthetics can significantly impact marketability.
While the initial investment in 5-axis machining technology may be higher than that of 3-axis systems, the long-term savings can be substantial. Reducing labor costs, minimizing setup times, and ensuring precision translate into fewer defective parts and rework costs. Companies can ultimately achieve a higher return on investment through increased productivity and quality.
5-axis CNC machining is especially advantageous for industries requiring incredibly complex and sophisticated parts. In sectors such as aerospace, medical implants, and automotive engineering, the intricacies of designs demand a machining process capable of achieving such specifications. The cumulative benefits of precision, reduced setup time, and increased flexibility make 5-axis machining the ideal choice for these sectors.
Applications of 5-Axis CNC Machining
5-axis CNC machining is making waves across many industries due to its advanced capabilities. Here are some notable applications:
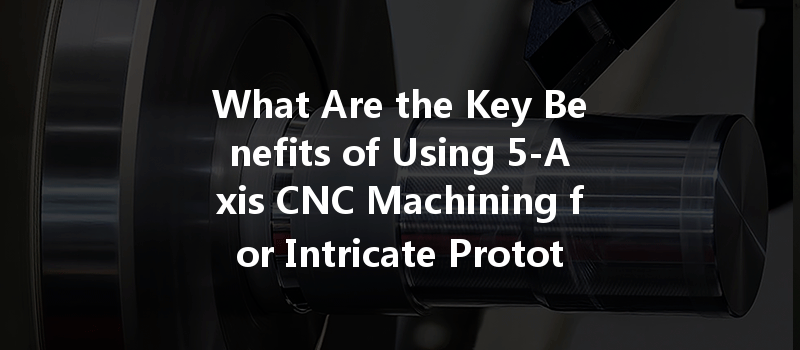
Aerospace Industry
In aerospace, the manufacturing process must adhere to stringent regulations. 5-axis machining can produce lightweight yet sturdy components that enhance aerodynamics, improve fuel efficiency, and ensure safety. Due to its high precision, parts such as turbine blades, housings, and intricate engine components are fabricated with finesse.
Medical Devices
With a growing emphasis on patient-specific devices and implants, the medical industry is leaning on 5-axis machining for custom solutions. The ability to create complex geometries allows for the development of intricate surgical instruments and implants, tailored precisely to individual patient needs.
Automotive Sector
From prototypes to final production models, the automotive industry relies on 5-axis CNC machining for components ranging from engine blocks to custom brackets. The flexibility allows manufacturers to test and refine designs quickly, optimizing performance while assuring regulatory compliance.
Electronics
5-axis CNC machining can produce compact enclosures, connectors, and intricate housings needed for electronic devices. Its ability to work with various materials, including aluminum and titanium, makes it a favored choice for the electronic industry, where functionality and aesthetics go hand-in-hand.
Defense
In defense applications, where reliability and performance are paramount, 5-axis machining is instrumental in fabricating weapon housing, satellite components, and equipment used in combat scenarios. The precision involved ensures that critical components can withstand extreme conditions.
Choosing the Right 5-Axis CNC Machining Service
Selecting the right service provider is essential for maximizing the benefits of 5-axis CNC machining. Here are the key factors to consider:
Expertise and Experience
It’s crucial to partner with a service provider that has a proven track record in 5-axis machining. It’s worth investigating their portfolio of previous projects to understand their range and capability.
Technology and Equipment
The capabilities of the machinery used can affect the quality of the final product. Ensure that the service provider utilizes modern and well-maintained 5-axis CNC machines equipped with the latest technology and software.
Material Knowledge
Different materials have unique characteristics that influence the machining process. The chosen provider should have extensive knowledge in working with diverse materials (e.g., aluminum, titanium, plastic) to ensure optimal results.
Lead Times and Flexibility
In the fast-paced world of prototyping, lead times can often dictate project success. Seek out providers with the capacity for quick turnarounds while still maintaining quality control during the process.
Quality Assurance
An effective quality management system is vital to ensure parts meet designated standards. Look for service providers that incorporate comprehensive quality assurance protocols to maintain the integrity and quality of the products.
In conclusion, 5-axis CNC machining offers a multitude of advantages for intricate prototype development, from enhanced precision and reduced setup times to design flexibility and improved surface finish. As industries evolve and demand more complex products, the ability to rapidly develop prototypes has become a significant competitive advantage.
Incorporating 5-axis CNC machining into your prototyping process not only optimizes time and cost but also fosters innovation and creativity in design. As we look toward the future of manufacturing, embracing the full capabilities of advanced technologies like 5-axis CNC machining will be imperative in keeping pace with market demands.
Thinking critically about how technology such as 5-axis CNC machining can impact your workflow is not just beneficial; it is essential in an industry where precision and efficiency define success. By understanding and implementing these solutions, manufacturers can unlock a new level of craftsmanship in their prototype development and ultimately drive their business forward.
As you navigate your journey in manufacturing, it’s essential to keep these benefits in mind and consider how they can be tailored to suit your specific needs and projects. The future is indeed bright for those who harness the full potential of this transformative technology.