An Eye-Opening Observation
Did you know that the global market for polycarbonate and acrylic materials is projected to reach approximately $17 billion by 2027? With rising demand for lightweight, durable materials in various industries, including aerospace, automotive, and manufacturing, knowing the differences in surface quality between CNC machined polycarbonate (PC) and acrylic (PMMA) can make a significant impact on product performance. This is not just an academic exercise; the choice you make can affect everything from product aesthetics to material durability.
In this comprehensive guide, we will delve into the intricacies of CNC machining for both polycarbonate and acrylic, exploring not only the distinctions in surface quality but also the overall implications for design, manufacturing efficiency, and end-use applications. This blog aims to serve as a go-to resource for engineers, designers, and industry professionals seeking clarity on material selection and machining processes.
—
Definition and Overview
Computer Numerical Control (CNC) machining is a manufacturing process wherein pre-programmed computer software dictates the movement of factory tools and machinery. The CNC machine takes in a digital design file and translates it into precise movements to create parts from a range of materials.
The Role of Materials in CNC Machining
The choice of material plays a pivotal role in the success of any machining operation. Different materials behave differently under machining conditions, affecting parameters like cutting speed, tool wear, and ultimately, surface quality. Understanding the specific characteristics of materials like polycarbonate and acrylic can lead to superior machining outcomes and enhanced product performance.
—
What is Polycarbonate?
Polycarbonate, often abbreviated as PC, is a versatile thermoplastic characterized by its high impact resistance and optical clarity. It is commonly used in applications where durability and strength are paramount.
What is Acrylic (PMMA)?
Acrylic, also known as polymethyl methacrylate (PMMA), is a transparent thermoplastic that is often seen as a lightweight alternative to glass. While it offers excellent clarity and UV resistance, it is not as impact-resistant as polycarbonate.
Properties of Each Material
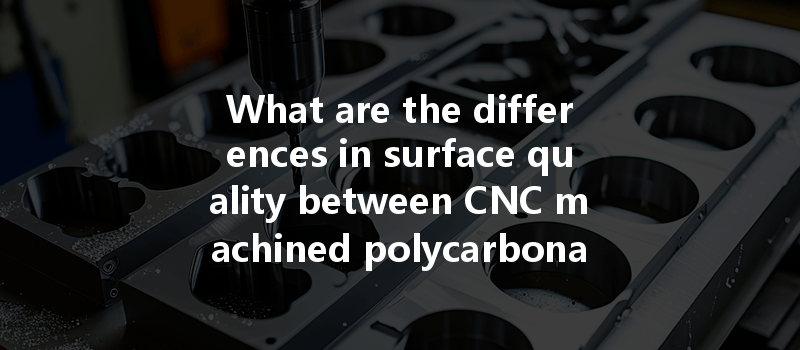
—
What is Surface Quality?
Surface quality refers to the texture and finish of the machined part’s surface. It can dramatically affect the part’s aesthetic appeal, fit and finish, functionality, and durability.
Factors Affecting Surface Quality in CNC Machining
Several factors can influence the surface quality of CNC machined parts:
—
CNC Machining Techniques
There are various CNC machining techniques, including milling, turning, and routing, each revealing different characteristics when applied to polycarbonate and acrylic.
Comparison of CNC Machining Processes for PC and PMMA
—
Visual Aesthetics
While both materials can be made clear and visually appealing, acrylic typically offers superior optical clarity. Polycarbonate, on the other hand, may exhibit a slight haze due to its manufacturing process.
Texture and Smoothness
CNC machined polycarbonate can provide a nice finish with good smoothness; however, it is often more sensitive to tool selection and machining parameters compared to acrylic.
Scratch and Impact Resistance
In practical applications, polycarbonate is generally more resistant to impacts, while acrylic is hassle-free regarding surface blemishes as it can be polished easily.
—
Popular Uses for Polycarbonate and Acrylic
Case Studies on Material Choice Impact
Selection between acrylic and polycarbonate can significantly impact project costs and timelines. For example, a case study of automotive headlamps showed that while acrylic might be cheaper initially, polycarbonate offers lower operational costs over time due to durability.
—
Tool Selection
The right tooling is essential for achieving desired finishes. Using appropriate drill bits, end mills, or specialized tools designed for plastic can enhance surface quality.
Machining Parameters and Speed
Operators should experiment with different feed rates and spindle speeds, as a higher RPM may lead to better finishes on softer materials like acrylic.
Post-Processing Techniques*
To improve surface quality, post-processing techniques such as sanding, polishing, or coating can be employed effectively.
—
In summary, understanding the differences in surface quality between CNC machined polycarbonate and acrylic is pivotal for anyone involved in manufacturing or product design. As we have discussed throughout this blog, the selection of materials directly affects both the aesthetic and functional qualities of a manufactured part.
Investing time in grasping these differences not only enhances your ability to choose the right material but also helps in developing high-quality products that meet market demands. Whether you’re involved in engineering, product design, or manufacturing, the insights gained here provide a foundation for making informed choices that can drive project success and innovation.
Ultimately, whether your application leans towards the durability of polycarbonate or the clarity of acrylic, understanding their properties and machining techniques is essential in today’s competitive landscape. This knowledge is not just valuable; it is vital for taking your projects to the next level.
So, before you embark on your next machining project, remember: the right choice of material and machining process can lead to extraordinary results!