Opening:
Did you know that stainless steel is one of the most dynamically versatile materials used in manufacturing? It accounts for approximately 50% of all metals processed globally. Among the many varieties of stainless steel, 17-4PH and 316 hold particular significance in various industries, including aerospace, automotive, and medical. However, differing machining properties and applications between these two stainless steel grades mean that manufacturers must thoughtfully choose the right CNC processing tools. In this blog, we will dive into the essential differences in CNC processing tool selection for 17-4PH stainless steel and 316 stainless steel, exploring why the right tool choice can make or break a machining project.
Understanding Stainless Steel Grades: An Overview
Before we delve into tool selection, it’s essential to understand the characteristics and compositions of 17-4PH and 316 stainless steels.
Known for its exceptional strength and hardness, 17-4PH is a precipitation-hardening stainless steel. This alloy contains approximately 17% chromium and 4% nickel, along with copper which promotes its hardenability. Commonly used in high-strength applications such as aerospace components, chemical processing, and dental instruments, 17-4PH offers excellent corrosion resistance.
Often referred to as marine grade stainless steel due to its enhanced corrosion resistance, 316 contains 16% chromium, 10% nickel, and 2% molybdenum. This composition provides improved resistance to pitting and crevice corrosion, especially in chlorine-rich environments. Typically used in marine applications, medical devices, and food processing equipment, 316 is recognized for its durability and hygiene.
The Importance of Tool Selection in CNC Processing
The effectiveness of CNC (Computer Numerical Control) machining significantly relies on the tooling used. When machining materials like stainless steel, several factors must be taken into account, including:
Selecting the right tools not only influences the quality and accuracy of the final parts but also impacts production efficiency, tooling costs, and overall piece longevity. Let’s examine how these factors specifically apply to machining 17-4PH and 316 stainless steels.
The hardness of the workpiece material directly determines the type of cutting tools you’ll need. Since 17-4PH is harder than 316 stainless steel, this affects the choice of tools:
Typically, carbide tools are preferred for machining 17-4PH due to their hardness and resistance to wear. Specialized coatings such as titanium nitride (TiN) or aluminum oxide (Al2O3) further enhance performance, allowing better heat resistance and reduced friction.
While carbide tools are also suitable for 316, you might opt for tools with a higher cobalt content to improve toughness and wear life in this softer stainless steel. Tools with a sharp edge are crucial to avoid work hardening.
The geometrical aspects of cutting tools play a crucial role, too. Here’s how they typically differ:
For 17-4PH, look for tools with a design that facilitates efficient chip removal and minimizes friction. Tool geometries should have higher rake angles to decrease cutting resistance.
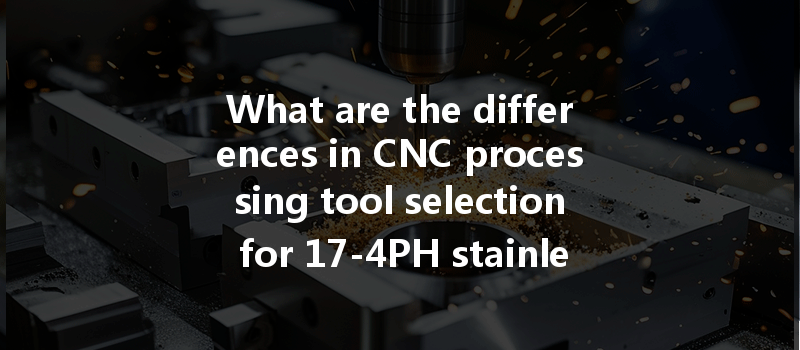
For 316 stainless steel, tools with rounded edges tend to reduce the risk of work hardening but may require a sharper cutting edge to effectively slice through the material without deformation.
The success of CNC machining depends heavily on adjusting cutting parameters to suit the material:
Recommended cutting speeds for 17-4PH can be lower than those of 316 due to its greater hardness. Typical speeds might range from 80 to 150 feet per minute (FPM) based on cutter type.
Shorter depths of cut for 17-4PH aid in controlling tool wear and achieving accurate finishes. For 316, slightly higher feed rates can improve efficiency but necessitate close monitoring to mitigate risks of work hardening.
When machining any type of stainless steel, the right cooling and lubrication can prevent overheating:
Consider using high-pressure coolant systems. This will keep temperatures manageable and assist chip removal, which is vital to avoid thermal distortion.
Utilizing cutting fluids specifically designed for stainless steel can help reduce friction. These fluids are effective in preventing galling and extending tool life during processing.
Monitoring and evaluating tool wear is key to maintaining a productive CNC environment:
Anticipate increased wear rates due to the material’s hardness. Regular checks and timely tool replacement are essential to maintain quality.
The wear on tools used for 316 stainless steel can be monitored through visual inspections and performance measurements. Using coated tools can help extend their operational lifespan.
: Choosing Wisely for Efficient CNC Machining
In the CNC world, the selection of tools for machining 17-4PH stainless steel and 316 stainless steel is pivotal for achieving production goals. By understanding their distinct properties and recommended tooling practices, manufacturers can optimize machining processes, reduce costs, and enhance the quality of the final products.
As industries continue to evolve with innovations in CNC technology and materials, being aware of the nuances in tool selection for different stainless steel grades is crucial—not just for efficiency, but for maintaining competitive advantages in manufacturing. The thoughtful integration of knowledge, technology, and practice will empower machinists and engineers to forge durable and high-performing components for future applications.
In summary, recognizing the importance of selecting the right CNC tools for specified grades of stainless steel encourages best practices in machining and reinforces the value of ongoing education in the manufacturing sector. Remember, the tools you choose can significantly impact both your bottom line and the integrity of your products. It’s a topic worth contemplating as technology and market demands continue to advance.