: The Intricacies of CNC Milling
Did you know that more than 75% of all metal components manufactured today are aluminum-based? This impressive statistic highlights the significance of aluminum alloys in various industries, including automotive, aerospace, and consumer electronics. With a growing demand for lightweight yet durable materials, the precision and accuracy of manufacturing processes, particularly CNC (Computer Numerical Control) milling, directly impact product quality and performance.
CNC milling of aluminum alloys is a complex process that requires a careful selection of techniques, tools, and parameters to ensure optimal results. As the industry continues to evolve, manufacturers are facing increased pressure to reduce costs while improving precision. This blog aims to explore the best techniques for CNC milling aluminum alloys, offering solutions for achieving high-quality outcomes and timely deliveries.
Understanding CNC Milling of Aluminum Alloys
What is CNC Milling?
CNC milling is a subtractive manufacturing process that involves the use of computer-controlled machines to remove material from a workpiece and create a desired shape or part. Unlike traditional machining methods, CNC milling uses algorithms and software programs to control the motion of cutting tools, allowing for greater accuracy and repeatability.
Why Aluminum Alloys?
Aluminum alloys are favored for CNC milling due to their lightweight nature, corrosion resistance, and ability to be easily machined. Additionally, they possess excellent thermal conductivity and strength-to-weight ratios, making them ideal for various applications. Common aluminum alloys used in CNC milling include 6061, 7075, and 2024, each offering specific properties suitable for different tasks.
Key Techniques for CNC Milling of Aluminum Alloys
One of the most critical factors in achieving quality CNC milling results is the selection of appropriate tools. Here are some considerations:
Setting appropriate cutting parameters is essential to ensure both tool and workpiece longevity:
Effective cooling and lubrication are vital in maintaining tool life and improving product quality:
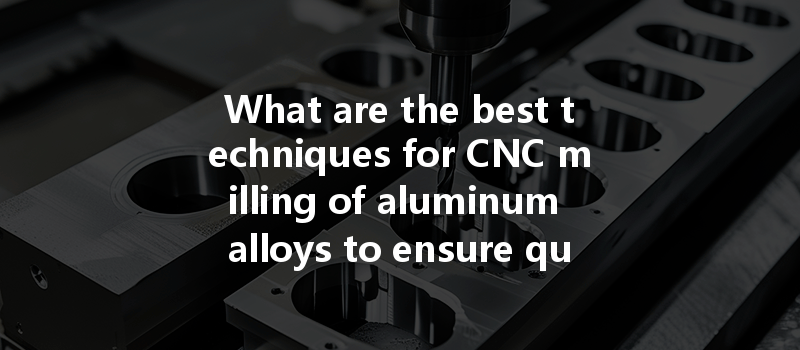
Optimizing the tool path can significantly improve machining accuracy and efficiency. Several strategies to consider include:
Proper fixturing is key to achieving accurate and consistent milling results:
To guarantee precision in CNC milling of aluminum alloys, implementing a robust quality control process is essential:
The CNC milling industry is constantly changing, with new techniques and technologies aimed at improving productivity and quality. Companies should remain committed to ongoing training and staying updated on industry trends:
: Pioneering Quality and Precision in CNC Milling
In conclusion, CNC milling of aluminum alloys is a multifaceted process that requires diligent attention to techniques, tools, and parameters. From tool selection and cutting parameters to cooling methods and tool path strategies, each element plays a vital role in ensuring high-quality outcomes. Additionally, the importance of fixture setup and rigorous quality control is underscored, as they serve as the final gatekeepers of precision.
As the demand for lightweight and durable materials continues to rise, the CNC milling industry must adapt and innovate. By fostering a culture of continuous improvement and embracing technological advancements, manufacturers can position themselves to meet both current and future market demands.
In today’s competitive landscape, understanding and implementing the best techniques for CNC milling aluminum alloys is not just beneficial but critical. These processes are key to achieving superior quality and satisfying customer requirements while balancing industry pressures to reduce costs and improve efficiencies. As you contemplate your next CNC milling project, consider the techniques discussed in this blog, and you’ll be well on your way to achieving unmatched precision and quality in aluminum machining.