Did you know that aluminum ranks as the third most abundant element in the earth’s crust, making up about 8% of its mass? Furthermore, due to its lightweight and corrosion-resistant properties, aluminum is often the go-to metal for various applications, especially in aerospace, automotive, and electronics industries. With the advent of technology, Custom CNC machining has revolutionized the way we manufacture parts and components from aluminum alloys. In this blog, we will explore the multitude of benefits that CNC machining offers for custom aluminum alloy parts, diving deep into why this manufacturing method is crucial for businesses looking to gain a competitive edge.
What Is CNC Machining?
CNC Machining, or Computer Numerical Control Machining, is an automated machining process that employs pre-programmed computer software to control machinery. Unlike traditional machining methods that require manual operation, CNC machines enable precise cutting, milling, drilling, and shaping of various materials, specifically metals like aluminum.
The Importance of Custom Aluminum Alloy Parts
The unique properties of aluminum alloys make them desirable in various industries. Common attributes include:
However, to fully leverage these properties, manufacturers often require custom aluminum parts tailored to their specific needs. This is where CNC machining comes into play.
Why Choose CNC Machining for Custom Aluminum Alloy Parts?
Here are the key benefits of using CNC machining for custom aluminum alloy parts:
CNC machines provide unparalleled precision, allowing for tolerances as tight as ±0.001 inches. This level of accuracy is essential for industries such as aerospace, where even the smallest deviation can have catastrophic consequences. CNC machining ensures that every component meets exact specifications, thereby reducing the risk of errors.
CNC machining allows for complex geometries and intricate designs that would be impossible to achieve using traditional methods. Whether it’s creating unique shapes or custom features like holes and threads, CNC allows manufacturers the freedom to innovate.
CNC machining drastically reduces production time due to its automated processes. Once a program has been developed and fine-tuned, machines can run continuously, producing parts in a matter of hours instead of days or weeks. This accelerated speed is especially beneficial for businesses requiring rapid prototyping or those involved in fast-paced industries.
Another compelling advantage of CNC machining is its material efficiency. Traditional machining often involves excessive waste due to cutting and shaping, increasing costs and negatively impacting sustainability initiatives. CNC machining, however, is designed to minimize waste, making it a more economical choice for companies looking to optimize their resources.
Consistency is crucial in manufacturing, particularly when producing large quantities of parts. CNC machines excel in delivering consistent results, meaning that every part produced will maintain the same quality and dimensions. This repeatability is vital for maintaining brand reputation and customer satisfaction.
While the initial investment for CNC machinery may be high, the long-term savings outweigh upfront costs. The combination of speed, precision, and material efficiency translates into a lower cost per part, making CNC machining a wise financial choice for businesses of all sizes.
CNC machining is compatible with a wide range of aluminum alloys, allowing manufacturers the flexibility to choose the right material for their specific application. This is particularly important in specialized industries like electronics, aerospace, and automotive, where different alloys may be required for various components.
Detailed Solutions for Successful CNC Machining
To get the best results from CNC machining for custom aluminum alloy parts, several steps can be taken. Here’s a comprehensive guide to ensuring optimal production:
Step 1: Material Selection
Selecting the right aluminum alloy is crucial for achieving desired performance characteristics. Common alloys include:
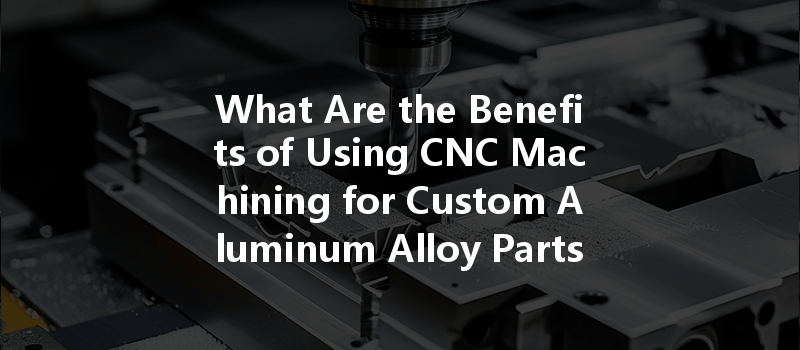
Consider the required strength, corrosion resistance, and weight when making your selection.
Step 2: Design for Manufacturing (DFM)
Utilizing DFM principles can significantly improve the CNC machining process. Ensure your design is optimized for machining, considering factors like:
Step 3: Selecting the Right CNC Machining Center
Choosing the correct CNC machining center is essential. Factors to consider include:
Step 4: Programming and Tool Path Optimization
The programming phase is crucial for ensuring that the machine operates efficiently and accurately. Deliver the correct G-code to the machine, and undergo these critical steps:
Step 5: Quality Control and Testing
Once machining has commenced, implementing rigorous quality control measures is essential:
Utilizing CNC machining for custom aluminum alloy parts comes with a plethora of benefits including precision, flexibility, speed, and cost-effectiveness. By understanding the advantages and following a comprehensive approach to production—from material selection to quality control—manufacturers can greatly improve their outcomes.
As technology continues to advance, the role of CNC machining in the manufacturing landscape is only expected to grow. Therefore, businesses that adopt CNC machining not only remain competitive but also enhance their capabilities for innovation and efficiency.
In summary, the shift toward CNC machining for custom aluminum alloy parts is not just a trend; it represents a significant evolution in manufacturing, addressing core issues like precision, efficiency, and cost-effectiveness. Investing time and resources into this technology can lead to substantial long-term benefits, solidifying your place in the dynamic landscape of modern manufacturing.
If you’re considering implementing CNC machining for your projects, take this knowledge and explore how it can apply to your specific needs. The potential can transform your production capabilities, ensuring you remain at the forefront of your industry.