Did you know that around 60% of all engineering prototypes are made of aluminum? This lightweight metal is not only economical but also provides high strength and durability, making it ideal for a wide array of applications. In industries ranging from aerospace to automotive, prototyping serves as a crucial step in product development, and the emergence of CNC (Computer Numerical Control) machining has revolutionized this process. So, why is CNC machining particularly beneficial for developing aluminum prototypes? This blog will delve into the myriad advantages of CNC machining, explore its applications in aluminum prototyping, and provide detailed insights into how it can elevate your manufacturing process.
Understanding CNC Machining
CNC machining is an automated process that employs computer-controlled machinery for manufacturing parts. This technology allows for high precision, repeatability, and efficiency. CNC machines can perform a variety of tasks, including milling, turning, drilling, and grinding, all of which are essential in creating prototypes. Unlike traditional machining, which often relies on manual interventions, CNC machining is programmed, enabling manufacturers to achieve tighter tolerances and consistent results.
Benefits of CNC Machining for Aluminum Prototypes
One of the most significant benefits of using CNC machining for aluminum prototypes is the astounding level of precision and accuracy that can be achieved. CNC machines operate on mathematical algorithms, ensuring that each cut is made exactly as programmed. This level of precision is particularly critical in prototype development, where even small deviations can lead to significant issues in the final product.
Aluminum prototypes often require intricate designs and complex geometries, especially in fields like aerospace and medical device manufacturing. CNC machining excel at producing geometrically challenging components that would be difficult to achieve through traditional methods. This capability opens up a world of design possibilities, enabling engineers to push the boundaries of innovation.
In prototyping, maintaining consistency across multiple parts is essential. CNC machining allows manufacturers to replicate the same design with the same level of accuracy, irrespective of the number of units produced. This repeatability ensures that testing and validation processes yield reliable results, making it easier to finalize designs before moving to mass production.
Time is of the essence in product development. CNC machining can considerably reduce lead times by automating numerous steps in the manufacturing process. Compared to manual machining, CNC machines can operate continuously, which means faster turnaround on prototype builds. This efficiency is critical in fast-evolving industries where staying competitive means getting products to market quicker.
While this blog focuses on aluminum, it’s important to note that CNC machining can work with a diverse range of materials, including plastics, composites, and different metals. This versatility allows for experimentation with various materials in the prototyping phase, which can lead to optimized final designs.
Despite the initial investment in CNC technology, the long-term cost savings are substantial. The precision of CNC machining minimizes material wastage, and the increased speed reduces labor costs. In prototyping, where multiple iterations are often required, these cost efficiencies become especially evident.
Given that CNC machines are computer-operated, human error is significantly reduced. Mistakes that might occur in the manual setup and execution of machining operations are virtually eliminated, leading to a more streamlined and reliable prototype development process.
CNC machining is often integrated with Computer-Aided Design (CAD) software, which means that prototypes can be built directly from digital designs. This seamless transition from design to manufacturing accelerates the prototyping process and allows for real-time adjustments based on testing feedback.
The digital nature of CNC machining allows for quick adjustments to designs without needing to manufacture new tooling. If a design change is necessary, the CAD file can be updated, and the CNC machine can produce the new prototype without significant downtime.
CNC machining can achieve high-quality surface finishes that contribute to the aesthetic quality of the final product, as well as its functionality. This is particularly beneficial for industries such as consumer electronics, where appearance is often as critical as performance.
CNC Machining Process for Aluminum Prototyping
Understanding the CNC machining process is crucial for effectively utilizing this technology in aluminum prototype development. Here’s a step-by-step breakdown of how it typically works:
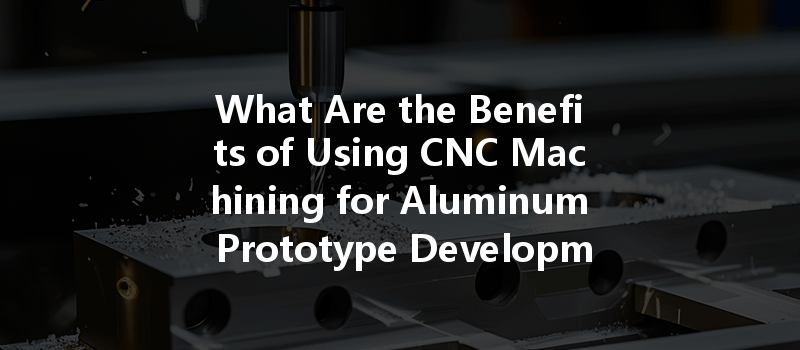
Application of CNC Machining in Various Industries
CNC machining for aluminum prototyping is used across various industries, each with its unique requirements and challenges. Here are some notable applications:
In conclusion, CNC machining offers a plethora of advantages for aluminum prototype development. Its precision, efficiency, and flexibility make it a go-to option for various industries aiming to innovate and produce high-quality prototypes. By leveraging CNC technology, manufacturers can achieve faster turnarounds, reduce costs, and create complex designs with ease.
As we enter a new era of manufacturing that increasingly relies on automation and advanced technology, CNC machining stands out as an essential process for businesses aiming to remain competitive. Whether you are a seasoned engineer or a newcomer to the industry, embracing CNC machining for your aluminum prototypes can help you streamline your production process and realize your design visions more effectively.
It’s crucial to consider the advantages discussed in this blog as you reflect on your product development strategies. CNC machining isn’t just a method; it’s a transformative approach that can redefine the way prototypes are constructed and viewed across industries, promoting innovation and supporting a higher standard of manufacturing excellence.