Did you know that the precision machining market is expected to reach approximately $130 billion by 2028, driven in part by the burgeoning demand for high-quality aluminum die-casting components? With the automotive and aerospace industries leading the charge, businesses worldwide are increasingly turning to precision machining to enhance their production capabilities. If you’re curious about what sets precision machining apart in the realm of aluminum die-casting parts, you’re in the right place. This blog will delve into the intricacies of precision machining, highlighting its benefits, techniques, and applications, ensuring you understand why it is essential for modern manufacturing processes.
Understanding Precision Machining
What is Precision Machining?
Precision machining is a manufacturing process that involves removing material from a workpiece to create precise parts and components. By employing various techniques such as milling, turning, and grinding, machinists can achieve tolerances of up to +/
What is Aluminum Die-Casting?
Aluminum die-casting is a technique that allows for the mass production of complex aluminum parts. It involves injecting molten aluminum into a steel mold, where it cools and solidifies into the desired shape. Compared to other metals, aluminum is lightweight, corrosion-resistant, and has excellent thermal conducting properties, making it a popular choice for a variety of industries.
The Interplay Between Precision Machining and Die-Casting
While die-casting is excellent for producing large volumes of complex parts quickly, sometimes a secondary operation is required to achieve the desired precision and finishing. This is where precision machining comes in. By integrating precision machining with aluminum die-casting, manufacturers can produce high-quality components with intricate details and superior surface finishes.
Benefits of Precision Machining for Aluminum Die-Casting Parts
Precision machining allows manufacturers to achieve very tight tolerances, which are often necessary for high-performance applications. Parts manufactured through precision machining exhibit high dimensional accuracy, which translates to fewer defects, reduced rework, and lower production costs.
In today’s competitive landscape, the ability to fabricate parts with complex geometries is essential. Precision machining enables the production of intricate designs that may be difficult or impossible to achieve through traditional manufacturing processes alone.
Precision machining techniques can produce parts with a superior surface finish compared to die-casting alone. This can enhance the aesthetic appeal of products as well as improve their functional performance, such as reducing friction and wear in mechanical applications.
Precision machining minimizes waste by carefully planned cuts and operations, making it an environmentally friendly option. Additionally, the ability to machine parts from bar stock or billets offers design flexibility and reduces the need for large quantities of raw materials.
While die-casting is known for its speed, adding precision machining to the process can further expedite production timelines. With the right setup and equipment, manufacturers can achieve rapid turnaround times, meeting even the most demanding deadlines.
The precision machining process is adaptable to custom orders and immediate changes in design. This is particularly significant in industries that require bespoke components due to changing specifications or customer demands.
Techniques in Precision Machining for Aluminum Die-Casting Parts
CNC (Computer Numerical Control) milling machines are ubiquitous in precision machining. These machines utilize rotating cutting tools to remove material from a workpiece. CNC milling is particularly effective for creating complex geometries and surface finishes that meet precise specifications vital in aluminum die-casting applications.
CNC turning involves rotating the workpiece against a stationary cutting tool. This method is ideal for producing cylindrical components and allows for high-speed operations. Parts that require intricate cuts or high precision benefit significantly from CNC turning.
EDM is another essential technique, particularly for creating fine details in tough materials. It works by eroding specific areas of the workpiece using controlled electrical discharges, making it suitable for applications that require extreme accuracy.
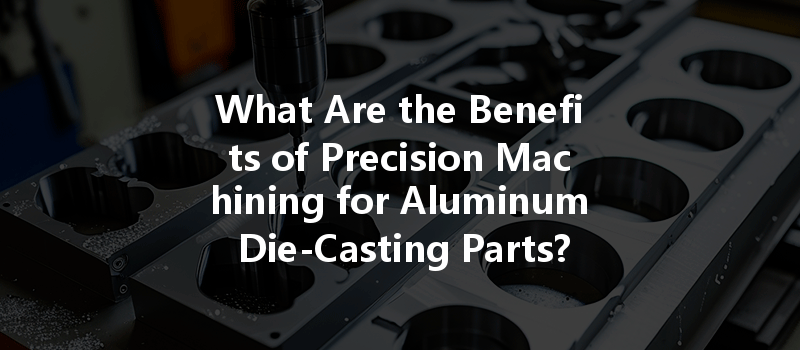
Laser cutting is gaining traction in precision machining due to its ability to slice through aluminum with high precision and speed. With minimal thermal distortion of the workpiece, laser cutting creates clean finishes while preserving the integrity of the material.
Grinding processes are often employed after initial machining to achieve tighter tolerances and smoother surfaces. Precision grinding can remove material uniformly and is ideal for high-precision applications in industries such as aerospace and automotive.
Applications of Precision Machining in Aluminum Die-Casting
The automotive sector uses precision machined aluminum die-cast parts for various applications, including engine components, transmission housings, and chassis parts. The lightweight nature of aluminum helps enhance fuel efficiency while its strength ensures safety.
In aerospace, each component must meet stringent safety regulations while ensuring lightweight performance. Precision machining allows manufacturers to produce intricate parts such as brackets, housings, and structural components that meet rigorous industry standards.
Precision machined aluminum parts are widely used in consumer electronics, especially in high-end products like smartphones and laptops. The combination of aesthetic appeal and functionality makes precision machining in die-casting essential in this rapidly evolving field.
Precision machining plays a pivotal role in fabricating medical devices, where reliability is crucial. Aluminum die-cast parts often serve in devices that require rigorous testing and conformity to health regulations.
Many industrial applications utilize precision machining to produce parts that withstand heavy loads and adverse conditions. These components are essential in construction machinery, manufacturing equipment, and various other industrial applications.
Overcoming Challenges in Precision Machining for Aluminum Die-Casting Parts
Tool wear can affect precision over time, necessitating regular checks and balancing of machining parameters to mitigate this issue. Using high-quality cutting tools and timely maintenance can prolong tool life and enhance overall precision.
Regular calibration of machinery is crucial in maintaining accuracy. Manufacturers must invest in high-quality setups and follow a diligent maintenance routine to ensure that the precision machining process meets tight tolerances.
Effective programming of CNC machines is vital for success. Mistakes in programming can lead to costly errors, so skilled programmers must oversee the process and utilize simulation software to anticipate potential problems.
Aluminum presents specific challenges in machining due to its softness and thermal conductivity. Adjusting machining parameters and tool choices can help mitigate these issues, allowing manufacturers to achieve the desired results in die-casting.
Precision machining for aluminum die-casting parts represents a vital component in modern manufacturing across various industries. The techniques employed enable manufacturers to achieve high tolerances, superior finishes, and the flexibility to create intricate designs. As industries push for innovation and efficiency, embracing precision machining is not just an option but a necessity.
Understanding the benefits, techniques, and applications of precision machining can empower businesses and engineers to make informed decisions that can elevate their operations to meet the needs of today and tomorrow. Investing in precision machining offers long-term advantages that often translate to improved quality, reduced waste, and ultimately, increased profitability.
So, as you contemplate the steps forward for your manufacturing processes, consider the insights shared in this blog. Adopting these techniques and understanding their importance can help your business thrive in a competitive landscape while ensuring the production of high-quality aluminum die-cast components.
By embracing precision machining, you are not just keeping up with industry standards—you’re setting them.