Did you know that the CNC machining market is expected to reach over $100 billion by 2025? As industries increasingly turn to automation and precision engineering, custom CNC machining has become an essential choice for producing high-quality industrial parts. In this blog, we will explore the various benefits of custom CNC machining, outlining how these processes can enhance production efficiency, reduce waste, and deliver precision-engineered components that meet specific industry needs.
Understanding CNC Machining
What is CNC Machining?
CNC (Computer Numerical Control) machining is a manufacturing process that utilizes programmed computer software to control machine tools. This includes processes such as drilling, milling, turning, and grinding. The precision and repeatability offered by CNC machining make it ideal for producing detailed and complex parts that meet exact specifications.
The Importance of Custom CNC Machining
While standard CNC machining services cater to general demands, custom CNC machining tailors solutions to the specific requirements of a business. This process allows for the production of unique parts that blend advanced technology with individual client specifications, making it invaluable in various sectors—from aerospace and automotive to medical devices and electronics.
Benefits of Custom CNC Machining for Industrial Parts
One of the standout advantages of custom CNC machining is its high level of precision. CNC machines operate with extreme accuracy, often within a few microns. This precision ensures that every component produced fits perfectly into its assembly and meets the defined tolerances.
Industries such as aerospace, which require components with exact specifications for safety and functionality, benefit immensely from this level of precision. Custom CNC machining allows manufacturers to create parts that adhere to stringent quality standards, ensuring the performance and reliability of the final product.
In today’s rapidly changing market, flexibility is essential. Custom CNC machining provides the ability to design parts tailored to unique specifications, accommodating a wide range of materials, designs, and dimensions. This adaptability allows companies to respond quickly to market demands or changes in design, thus maintaining a competitive edge.
Furthermore, CNC machines can produce small batches of custom parts, making it easier for customers to develop prototypes or new products without the need for significant upfront investment in tooling.
While it may seem that custom solutions are more expensive than mass-produced alternatives, the reality is often different. With custom CNC machining, companies benefit from reduced material waste and lower labor costs, as these machines can operate autonomously once programmed.
Additionally, the ability to produce precisely what is needed means there is less leftover material, which reduces overall costs. Moreover, custom parts can potentially eliminate the need for costly rework or repairs, offsetting initial production costs and yielding savings.
The automation of CNC machining significantly improves production efficiency. Once a design is programmed, machines can run continuously, producing large quantities of parts with minimal human intervention. The quicker cycle times achieved through CNC machining can lead to faster development and production schedules.
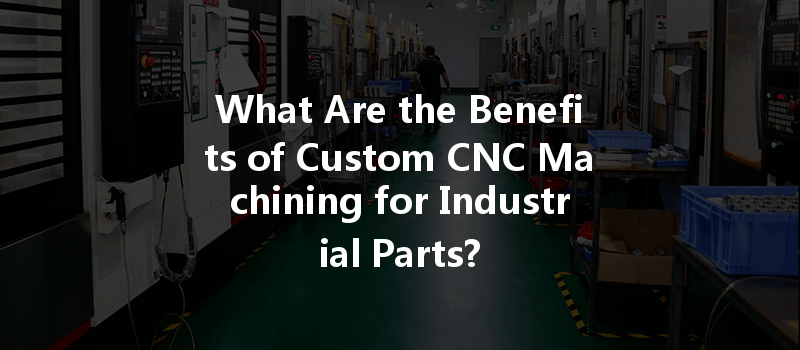
This efficiency is particularly beneficial for industries where time-to-market is critical. By enabling rapid prototyping and simultaneous production runs, custom CNC machining allows businesses to launch new products faster and adapt quickly to changing consumer demands.
Quality control is paramount in industries that manufacture precision-engineered parts. Custom CNC machining incorporates stringent quality control measures throughout the manufacturing process. Advanced CNC machines are often equipped with sensors and software that monitor production parameters in real-time, ensuring that each part meets the desired specifications.
This level of quality control reduces the likelihood of defects and enhances the overall reliability of products. Partnering with reputable custom CNC machining services means that manufacturers can trust that they will receive consistently high-quality parts.
Another significant advantage of custom CNC machining is its ability to work with a broad array of materials. Whether it’s metals such as aluminum, titanium, and stainless steel, or plastics, composites, and wood, CNC machines can be programmed to accommodate different material properties.
This versatility allows businesses to select the best materials for their specific applications, optimizing performance and functionality. The ability to prototype using various materials also fosters innovation and product development.
How Custom CNC Machining Works
To fully appreciate the benefits of custom CNC machining, it’s essential to understand the mechanics of how it operates. Generally, the process encompasses several key stages:
In conclusion, custom CNC machining offers unparalleled advantages for the production of industrial parts. With its ability to deliver precision-engineered components that cater to specific needs, this manufacturing process enhances quality, efficiency, and cost-effectiveness. In an ever-evolving market where adaptability and speed are crucial, investing in custom CNC machining is an intelligent choice for businesses seeking to maintain competitiveness and deliver high-quality products.
As industries continue to embrace automation and precision engineering, understanding the benefits of custom CNC machining will be essential for organizations aiming to navigate the complexities of modern manufacturing successfully. Remember, the right machining solutions can not only broaden your capabilities but also set you apart from competitors in your industry. Whether you’re developing a new prototype or scaling up production, consider the significant advantages that custom CNC machining can bring to your operations.