Did you know that over 90% of manufacturers globally are adopting CNC (Computer Numerical Control) machining to streamline their production processes? As industries strive for efficiency, precision, and reduced turnaround times, CNC machining has emerged as a game-changing solution. In this blog, we will delve into the myriad benefits of custom CNC machining for industrial parts, uncovering how it enhances productivity, quality, and overall operational efficiency.
The landscape of manufacturing is changing rapidly, driven by advances in technology and ever-evolving market demands. With the increasing complexity of parts and the need for mass customization, manufacturers must look for innovative solutions to meet their production goals. Custom CNC machining is one such solution that has gained traction across various sectors, from automotive to aerospace.
In this blog, we’ll explore:
Let’s dive deeper into these key areas to better understand the sophisticated world of custom CNC machining and its critical role in modern manufacturing.
Understanding CNC Machining
CNC machining is a manufacturing process that uses computer-controlled machinery to create complex parts with a high degree of precision. Unlike traditional machining methods, which rely heavily on human operators, CNC machines operate based on pre-programmed software. This results in greater accuracy, consistency, and efficiency, making CNC machining a popular choice for producing intricately designed components.
Brief Overview of CNC Technology
At its core, CNC machining employs various tools and techniques such as milling, turning, and drilling to shape materials into desired forms. The process typically involves the following steps:
By leveraging this technology, manufacturers can produce parts that are not only dimensionally accurate but also tailored to meet specific requirements in terms of material, functionality, and design.
The Custom CNC Machining Process
Custom CNC machining refers to the process of creating parts that are designed and manufactured to meet the unique specifications of clients. This approach allows for personalization and flexibility that traditional manufacturing processes may not offer. The custom CNC machining process can be broken down into several stages:
Key Benefits of Custom CNC Machining for Industrial Parts
One of the foremost benefits of custom CNC machining is the exceptional precision it delivers. CNC machines can achieve tight tolerances of +/
For instance, in the aerospace industry, components must fit together seamlessly to ensure safety and performance. CNC machining enables manufacturers to produce parts that meet stringent aerospace standards.
CNC machining supports an extensive range of materials, including metals (like aluminum, steel, and titanium), plastics, wood, and composites. This versatility allows industrial manufacturers to source components that best fit their operational needs.
Additionally, CNC machines can execute various machining processes in a single setup. From milling and turning to drilling and grinding, a custom CNC machining provider can tackle diverse manufacturing needs using one machine.
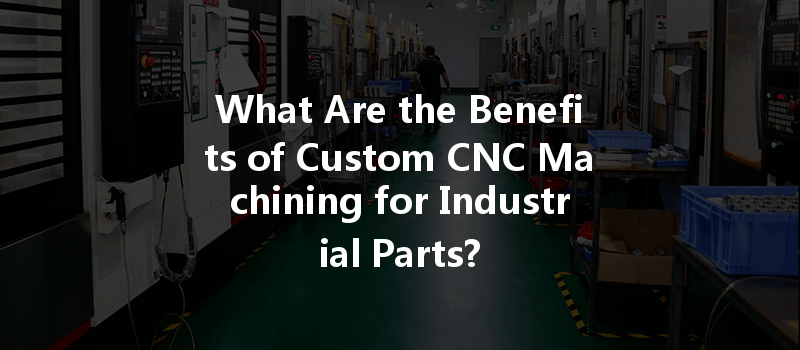
While the initial investment in CNC machines can be significant, the long-term cost savings often outweigh the expenditure. Custom CNC machining helps reduce waste, minimize labor costs, and increase production efficiency.
Moreover, the ability to produce high-quality parts consistently means that companies experience fewer reworks, repairs, and returns. In industries where margins are tight, these savings can greatly enhance profitability.
Speed is a critical component in manufacturing, particularly in highly competitive markets. Custom CNC machining significantly accelerates production timelines due to the automated nature of the process.
Once the initial setup is complete, CNC machines can operate continuously, producing large volumes of parts with minimal downtime. This attribute allows manufacturers to meet tight deadlines and adjust to fluctuating market demands swiftly.
As sustainability becomes a priority for many industries, custom CNC machining aligns with these goals by minimizing material waste. CNC processes are highly efficient, often utilizing only the necessary amount of material for each part, reducing scrap and excess.
Some CNC machining manufacturers also employ eco-friendly practices, such as recycling materials after production. This commitment not only boosts their environmental credentials but also appeals to eco-conscious companies.
Real-World Applications
Custom CNC machining is utilized across a range of industries, each benefiting differently based on their unique needs:
Aerospace Industry
In the aerospace sector, lightweight and durable components are essential. Custom CNC machining provides precision parts that adhere to strict safety regulations while minimizing weight.
Automotive Industry
With the rapid evolution of electric vehicles and autonomous driving technology, car manufacturers require precision-engineered components for performance and reliability. Custom CNC machining supports this by providing high-quality parts tailored for specific vehicle models.
Medical Device Manufacturing
In the medical field, where precision is paramount, CNC machining produces intricate components such as surgical instruments and implants. Manufacturers can ensure compliance with health and safety standards while delivering customized solutions.
Electronics
As technology advances, the demand for complex electronic components rises. Custom CNC machining enables the production of precision parts that meet the unique requirements of electronic devices.
Industrial Equipment
Machinery and equipment manufacturers depend on custom CNC machining for producing robust and highly accurate parts. This reliability enhances the durability and performance of industrial equipment.
What to Consider When Choosing a CNC Machining Partner
To successfully leverage the benefits of custom CNC machining, finding the right partner is crucial. Here are some factors to consider:
Look for a manufacturer with a proven track record in CNC machining. Their experience will often translate into higher quality and reliability in their output.
Ensure that the machining partner employs modern CNC technology and has the capabilities to handle your specific requirements — whether it’s the materials, tolerances, or part complexity.
A reputable CNC machining provider should have Quality Management Systems in place, adhering to recognized industry standards. Their commitment to quality ensures that the end product meets your specifications.
Effective communication is essential. Your CNC partner should be responsive and willing to collaborate throughout the design, prototyping, and manufacturing processes.
While cost is always a factor, be cautious about opting for the cheapest option. Consider lead times and overall value in relation to quality and service.
In summary, custom CNC machining is a transformative solution for industries looking to enhance production efficiency, precision, and customization. The benefits are clear: from delivering high-precision parts to reducing material waste and overall costs, CNC machining has made its mark on modern manufacturing. By understanding the machining process and the advantages it offers, businesses can make informed decisions that will benefit their operations.
Investing resources into custom CNC machining can yield significant dividends — not just in terms of quality and efficiency, but also in aligning with market demands and contributing to sustainability efforts.
Remember, the future of manufacturing is driven by precision, and custom CNC machining is at the forefront of this revolution. By prioritizing CNC technology, businesses can remain competitive in an ever-evolving marketplace.
For manufacturers eager to improve their production processes, embracing custom CNC machining is not just an option — it’s a necessity.