Did you know that the global CNC machining market is expected to reach over $100 billion by 2025? This remarkable growth is largely due to the diverse applications of CNC (Computer Numerical Control) technology across various industries, such as aerospace, automotive, medical, and electronics. CNC machining has revolutionized the way manufacturers produce precision metal parts and custom designs, offering unparalleled advantages in speed, accuracy, and efficiency. In this blog, we will delve deep into the myriad benefits of CNC machining for precision metal parts, exploring its applications, technologies, and best practices. By the end, you’ll have a comprehensive understanding of how CNC machining can significantly enhance your manufacturing processes.
The Evolution of CNC Machining
CNC machining has come a long way since its early days in the 1950s. Initially developed for the aerospace industry to improve manufacturing processes, CNC has since permeated virtually every sector that requires high-precision components. The introduction of computers into machine tools allowed operators to automate complex machining tasks, leading to increased productivity and reduced human error.
The technology has evolved from simple 2D operations to sophisticated 5-axis machining centers that can execute intricate designs with extreme accuracy. Modern CNC machines can now process various materials, including metals, plastics, and composites, making them versatile solutions for manufacturers.
Understanding Precision in CNC Machining
Precision is the cornerstone of CNC machining. It refers to the degree to which an operation is performed accurately and consistently. In industries such as aerospace and medical manufacturing, tolerances can be as tight as ±0.001 inches. Achieving this level of precision requires a stable process that not only minimizes error but also allows for repeatability across multiple production runs.
Advantages of CNC Machining for Precision Metal Parts
CNC machining’s automated nature ensures that parts are produced with exceptional accuracy. Unlike manual machining, where human error can lead to imperfections, CNC machines follow programmed commands to execute tasks precisely. This automation results in consistent quality across all produced components, crucial for high-stakes applications like aerospace or medical devices.
The speed of CNC machining substantially reduces lead times. Once a design has been programmed and tested, CNC machines can operate continuously, producing high volumes of parts without compromising quality. This speed is particularly advantageous in industries with tight deadlines and high demand for custom components.
While the initial investment in CNC machines can be significant, the long-term savings often outweigh the upfront costs. Factors contributing to cost-effectiveness include reduced labor costs, minimal material wastage due to precision cutting, and fewer machining errors, which can lead to expensive rework.
CNC machining is inherently adaptable to a wide range of materials and designs. This flexibility allows manufacturers to pivot quickly based on market demands or customer requests. With the ability to handle complex geometries and diverse materials—ranging from aluminum and steel to plastics—CNC machining empowers businesses to expand their offerings without the need for extensive retooling.
One of the most significant benefits of CNC machining is its ability to produce custom designs tailored to specific requirements. Whether it’s creating unique prototypes or specialized components, CNC machining can accommodate customizations that manual processes may not handle effectively. This personalization is vital in industries such as automotive or medical, where unique parts can be pivotal to product performance.
CNC machining is an excellent solution for prototyping. The technology allows engineers to swiftly create physical models of their designs, facilitating iterative testing and refinement. This rapid manufacturing capability ensures that businesses can get their products to market faster, ultimately gaining a competitive edge.
CNC machining is capable of working with a vast array of materials, each requiring specific machining techniques. Precision machining can effectively mold hard metals, composites, and plastics, making it suitable for both high-performance parts and prototyping. Moreover, advanced materials like titanium and stainless steel can be accurately processed due to CNC machining’s efficiency and precision.
CNC Machining Techniques
CNC turning involves rotating a workpiece against a cutting tool to shape it into the desired form. This process is particularly effective for cylindrical parts, such as shafts, bushings, and fittings.
CNC milling employs rotary cutters to remove material from a workpiece. Using various cutting tools, CNC milling can create intricate shapes and features, making it highly versatile.
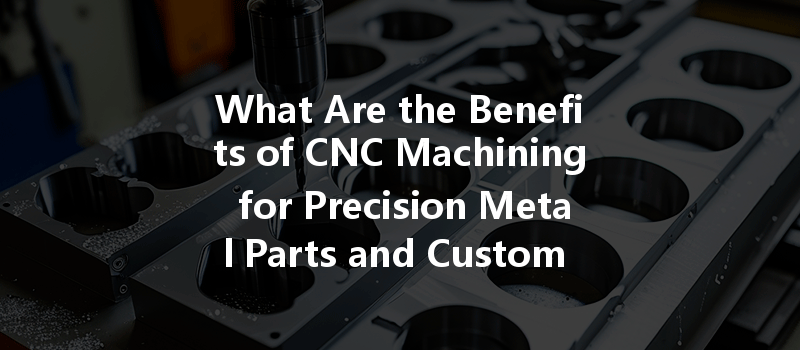
CNC drilling is used to create precisely placed holes in a workpiece. This technique is essential for parts requiring multiple joining points or assembly features.
EDM uses electrical discharge to cut hard materials, such as metals that are challenging to machine with traditional tools. This method facilitates high precision in intricate shapes.
Challenges and Solutions in CNC Machining
Challenge: The purchase of CNC machinery can represent a substantial financial commitment for manufacturers, especially small businesses.
Solution: Consider leasing machines or investing in used equipment to mitigate upfront costs. Additionally, evaluating the total cost of ownership—including maintenance, training, and operation—can provide a more accurate financial outlook.
Challenge: Operating CNC machines requires a specialized skill set, which can be a barrier for some businesses.
Solution: Invest in workforce training programs that can upskill employees. Alternatively, outsourcing machining processes to specialized firms can alleviate the need for in-house expertise.
Challenge: CNC machines require regular maintenance, and unexpected downtime can disrupt production schedules.
Solution: Establishing a preventive maintenance schedule can help reduce the risk of equipment failure and unplanned downtime. Keeping an inventory of vital spare parts can also expedite repairs.
Case Study: CNC Machining in Aerospace Manufacturing
The aerospace industry is one of the most demanding sectors for precision manufacturing. Components such as turbine blades and fuselage parts must meet stringent performance and safety standards.
Problem: Traditional machining methods struggled to achieve the required tolerances for complex geometries, resulting in lengthy lead times and increased costs.
Solution: By adopting CNC machining, an aerospace manufacturer transformed its production line. Implementing 5-axis CNC milling allowed for the creation of intricate designs without setup changes, leading to unmatched precision and a reduced time-to-market. In just two years, the company reported a 40% decrease in production costs and a tripling of its custom part offerings.
The Future of CNC Machining
Advances in technology are set to redefine CNC machining in the coming years. Here are some trends likely to shape the future landscape:
CNC machining represents a cornerstone of modern manufacturing, providing unparalleled precision, flexibility, and efficiency in producing metal parts and custom designs. From enhancing accuracy and consistency to enabling rapid prototyping and cost-effective solutions, the benefits of CNC technology are extensive. By leveraging advanced techniques and understanding the challenges involved, businesses can harness the full potential of CNC machining to deliver high-quality products tailored to meet their specific needs.
As industries continue to evolve and demands increase, CNC machining will remain vital for maintaining competitive advantages in precision manufacturing. The insights shared in this blog emphasize not just the technological advancements but also the importance of skilled workforce and proactive maintenance strategies in ensuring seamless operations.
In light of these factors, investing in CNC machining technology and expertise is paramount for businesses aiming to thrive in today’s fast-paced manufacturing landscape. The future is bright for those who embrace the possibilities that CNC machining has to offer, making it an essential consideration for anyone involved in manufacturing precision parts.
Let’s keep the conversation going—what are your thoughts on the future of CNC machining? Have your experiences been similarly transformative? Your insights could contribute to this ever-evolving field!