Did you know that the aerospace industry is projected to reach a market value of approximately $1 trillion by 2025? With skyrocketing demand, the emphasis on precision, reliability, and efficiency has never been more critical. Among the various manufacturing methods adopted in this industry, CNC (Computer Numerical Control) machining has emerged as a game-changer for creating customized aerospace metal components. In this blog, we will explore the myriad benefits of CNC machining for aerospace applications, discussing everything from precision engineering to cost-effectiveness and flexibility.
What is CNC Machining?
To understand the advantages of CNC machining in the aerospace field, it is essential to grasp what this technology entails. CNC machining is a manufacturing process that uses computerized controls to operate and manipulate machine tools. Unlike traditional machining methods, CNC allows for greater precision and automation, letting companies manufacture complex parts with minimal errors. Factors such as consistency, speed, and flexibility make CNC machining the preferred choice for many engineering applications, particularly in a niche as demanding as aerospace.
The Importance of Customized Components in Aerospace
In aerospace, there are significant challenges that require tailored solutions. Airplanes and spacecraft are designed to operate across various conditions, necessitating components that meet specific requirements such as weight reduction, durability, and aerodynamics. Off-the-shelf parts often fall short, leading manufacturers to seek bespoke solutions that adhere to stringent safety and performance standards.
Key Benefits of CNC Machining for Customized Aerospace Metal Components
CNC machining’s most significant draw is its precision. According to aerospace engineering standards, even the smallest deviation can lead to catastrophic failures. CNC machines operate with a degree of accuracy that can be measured in microns (one-millionth of a meter).
The aerospace sector employs a diverse range of materials, from lightweight aluminum alloys to strong titanium and high-performance composites. CNC machining can handle various materials with ease, enabling the creation of parts that exhibit the unique properties each material has to offer.
Unlike traditional machining methods, which require multiple setups and manual interventions, CNC machining automates the manufacturing process, allowing for faster production times and streamlined workflows.
The aerospace industry constantly evolves, often requiring non-standard parts tailored to specific applications. CNC machining provides unparalleled customization capabilities that allow engineers to design components according to precise specifications.
While the initial investment in CNC machinery may be higher than traditional methods, the long-term financial benefits often outweigh these costs. Precision machining reduces waste material and production errors, leading to significant savings in the manufacturing process.
Another significant advantage is the ease of implementing quality control during the CNC machining process. Digital designs allow for real-time monitoring of machine performance. This capability ensures that each component manufactured adheres to high-quality standards throughout the production run.
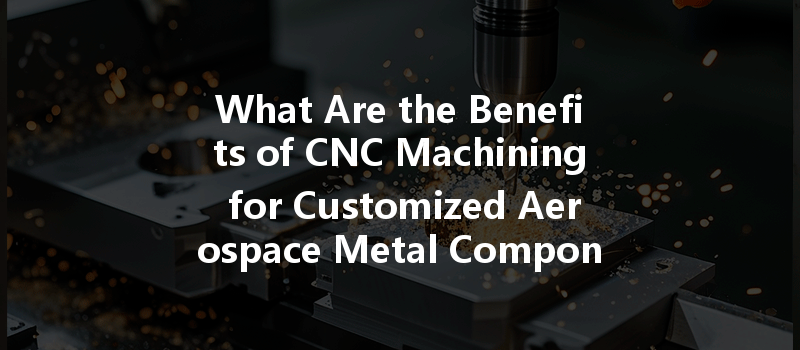
Markets change, technology advances, and consumer preferences evolve, often leading to fluctuations in demand. CNC machining is inherently flexible, allowing manufacturers to quickly adapt their production processes to meet changing market conditions.
A major hurdle in aerospace manufacturing is the challenging lead times associated with custom parts. Traditional manufacturing methods often involve lengthy prototyping and approval processes, leading to production delays.
Integrating CNC machining into the production process leads directly to enhanced productivity. Operator efficiency is improved due to automation, and machining operations can be conducted around the clock with minimal human intervention.
In recent years, there has been an increased focus on sustainable practices within the aerospace sector. CNC machining supports sustainability through efficient use of materials, reduced waste, and energy efficiency.
Challenges and Considerations for Implementing CNC Machining
While the advantages of CNC machining are extensive, specific challenges may arise during implementation. Understanding these hurdles can better position manufacturers for success:
Initial Investment Costs
CNC machines can represent a considerable upfront investment. It is essential to conduct a thorough cost-benefit analysis to ensure it aligns with long-term production goals.
Skilled Workforce
Although CNC machines are automated, skilled professionals are still needed to program, operate, and maintain these machines. Investing in training programs or hiring experienced operators can be vital for effective execution.
Maintenance Requirements
CNC machines require regular maintenance to ensure optimal performance and longevity. Manufacturers must develop a maintenance schedule and possibly invest in preventative measures to mitigate downtime.
CNC machining is not just a trend but a transformative force in the aerospace industry. With the substantial demand for customized aerospace metal components, the benefits of CNC technology are increasingly hard to ignore—high precision, versatility in materials, streamlined processes, and enhanced productivity are merely the tip of the iceberg.
As we have explored, implementing CNC machining offers a comprehensive solution to the complex challenges facing aerospace manufacturers, providing them with the tools necessary to innovate and adapt. As the industry continues to evolve, so will the technology and techniques surrounding CNC machining.
In a market where safety, reliability, and performance are paramount, understanding the intricacies and advantages of CNC machining is essential. The time to consider adaptation is now; as the aerospace sector grows, embracing modern manufacturing techniques will position companies for ongoing success in an interconnected world.
For anyone in aerospace manufacturing—be it engineers, product managers, or decision-makers—this blog emphasizes the importance of investing in CNC machining capabilities, ensuring that your operations remain resilient and competitive in today’s rapidly changing environment. Keep innovating, keep evolving, and remember there is always room for improvement in the quest for quality and excellence!