Did you know that aluminum is one of the most recycled metals on the planet, with an astounding 75% of all aluminum ever produced still in use today? This means aluminum is not only a sustainable choice for manufacturing but also continues to play a pivotal role in modern industries. One of the most effective methods for creating high-quality, custom aluminum alloy parts is CNC machining. In this comprehensive blog post, we will dive deep into the benefits of CNC machining for custom aluminum alloy parts, explore the technology involved, and detail how it addresses various industrial challenges.
Understanding CNC Machining
What is CNC Machining?
CNC (Computer Numerical Control) machining is a manufacturing process where pre-programmed computer software dictates the movement of machinery and tools. This technology is essential for producing parts and components with high precision and efficiency. CNC machining can make intricate shapes or designs in various materials, including metals, plastics, wood, and composites.
Why Aluminum Alloys?
Aluminum alloys are a popular choice in many industries because they offer an excellent strength-to-weight ratio, corrosion resistance, and high conductivity. The versatility of aluminum alloys encompasses a wide range of applications, from aerospace and automotive to electronics and consumer goods. The ability to create custom parts using CNC machining allows manufacturers to optimize performance and meet specific design requirements.
The Advantages of CNC Machining for Custom Aluminum Alloy Parts
One of the primary advantages of CNC machining is its ability to achieve high levels of precision and accuracy. CNC machines are equipped with advanced software that minimizes human error, allowing for the creation of parts that adhere to tight tolerances. For industries where precision is critical, such as aerospace and medical devices, CNC machining provides a reliable solution.
CNC machining can produce intricate designs and complex geometries that would be challenging to achieve through traditional manufacturing methods. This capability enables engineers and designers to push the boundaries of innovation and create parts with unique features that enhance functionality.
CNC machining ensures high repeatability, meaning that once a design is programmed into the machine, it can produce the same part consistently with the same quality and specifications. This is particularly important for production runs, where uniformity is essential for interoperability.
CNC machining allows for rapid production of parts, significantly reduced lead times, and a shorter manufacturing process. The automated nature of CNC machines enables them to operate continuously, reducing downtime and maximizing efficiency. In industries where speed is crucial, CNC machining can deliver parts much faster than traditional methods.
CNC machining is known for its ability to reduce waste. Compared to subtractive manufacturing techniques, which often leave significant scrap behind, CNC machining optimizes the use of raw materials, leading to cost savings and reduced environmental impact. This benefit is particularly valuable for industries that prioritize sustainability.
In today’s fast-paced market, the ability to adapt to design changes is vital. CNC machining allows for easy modifications to the programming, enabling manufacturers to produce different parts or adjust designs quickly without extensive retooling. This flexibility can result in a faster response to market demands.
While the initial investment in CNC machinery may be higher than traditional methods, the long-term cost-effectiveness of CNC machining can be significant. Reduced labor costs, minimal waste, high precision, and shorter production times contribute to overall savings. Additionally, CNC machining minimizes the risk of defects, further reducing costs associated with rework or scrap.
The integration of computerized systems in CNC machining allows for detailed monitoring and control of the manufacturing process. This leads to better quality assurance measures, including real-time data collection, which can identify issues before parts leave the facility. Enhanced quality control results in reliable products that meet industry standards.
Application of CNC Machining in Different Industries
Aerospace
The aerospace industry demands precision-engineered parts that can withstand extreme conditions. CNC machining of custom aluminum alloy parts plays an essential role in fabricating components such as aircraft brackets, housings, and frames. The lightweight properties of aluminum alloys, combined with CNC machining’s precision, contribute to fuel efficiency and overall performance.
Automotive
In the automotive sector, custom aluminum parts are vital for reducing weight while maintaining strength and durability. CNC machining facilitates the production of components like engine blocks, transmission parts, and chassis systems. By leveraging aluminum alloys, manufacturers can improve vehicle performance, fuel efficiency, and reduce emissions.
Electronics
The electronics industry often requires intricate and precise components and enclosures. CNC machining allows for the creation of custom aluminum housings, connectors, and brackets that meet specific design requirements. The thermal and electrical conductivity of aluminum alloys further enhances their use in electronic applications.
Medical Devices
Precision is paramount in the medical field, where manufacturers must produce critical components that meet strict regulatory standards. CNC machining offers the accuracy and repeatability needed for surgical instruments, implants, and diagnostic equipment. Custom aluminum parts ensure lightweight and biocompatible solutions for medical applications.
Military and Defense
The military and defense sectors also benefit significantly from CNC machining for custom aluminum alloy parts. Durability, lightweight construction, and resistance to corrosion are crucial attributes of parts used in vehicles, equipment, and weaponry. CNC machining aids in meeting the stringent specifications required for military applications.
Steps Involved in CNC Machining of Custom Aluminum Alloy Parts
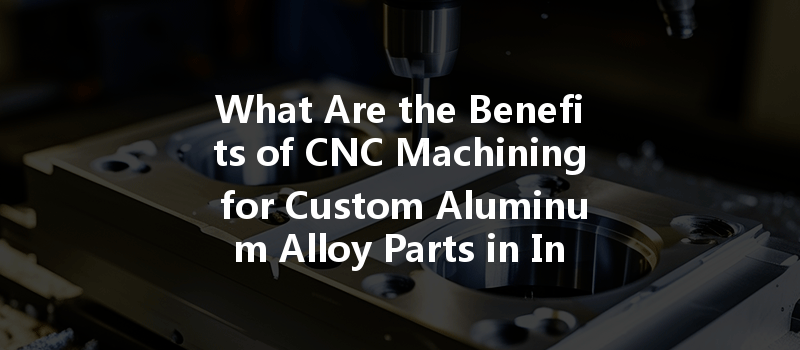
The first step in CNC machining is the design phase, where engineers use CAD (Computer-Aided Design) software to create precise 3D models of the desired parts. The design must account for factors such as tolerances and material properties.
Following the design phase, the next step is programming. The CAD model is converted into a format that CNC machines can read, typically using CAM (Computer-Aided Manufacturing) software. This software generates the specific commands that guide the CNC machine tool movements.
Once the programming is complete, manufacturers select the appropriate aluminum alloy for the job. The raw material is then cut into manageable sizes and shaped for machining.
With everything prepared, the CNC machine begins the machining process. Tools such as end mills, drills, and lathes remove material precisely to create the desired shape and finish. The machine continuously monitors performance to ensure adherence to specifications.
After machining, parts undergo rigorous quality control inspections. Measurements are taken to verify tolerance accuracy, surface finish, and overall integrity. This step is crucial for industries with stringent certification requirements.
Depending on the application, additional finishing operations such as anodizing, painting, or polishing may be performed to enhance aesthetics or corrosion resistance. Finishing ensures that the part meets final specifications and client expectations.
Once the final inspections and finishing operations are complete, parts are carefully packaged and prepared for delivery to the customer. Timely delivery is an integral part of customer service, especially in industries with strict timelines.
Addressing Common Challenges in CNC Machining for Aluminum Alloys
Material Characteristics
Aluminum alloys have unique characteristics that can pose challenges in CNC machining. For instance, their softness can lead to rapid wear on cutting tools. Employing high-quality, specialized tools and optimizing machining parameters can mitigate these issues, enhancing tool life and performance.
Thermal Management
The machining process generates heat, which can affect the integrity of the aluminum alloy and machining accuracy. Effective thermal management practices, such as using coolant lubricants and optimizing feed rates, can help dissipate heat and maintain optimal machining conditions.
Surface Finish Requirements
Depending on the application, the required surface finish can vary significantly. Achieving a high-quality surface finish may require multiple machining processes or additional finishing treatments. Understanding the specific finish requirements upfront allows for better planning and resource allocation.
Future Trends in CNC Machining for Custom Aluminum Alloy Parts
As technology evolves, we can expect further automation in CNC machining processes, driven by artificial intelligence and machine learning. This integration will enable predictive maintenance and optimization in real-time, leading to even higher levels of efficiency and precision.
The development of new aluminum alloys and composites will open doors to creating parts with advanced properties suitable for cutting-edge industries such as aerospace and medical devices. CNC machining will adapt to these materials, offering manufacturers flexible solutions.
The combination of CNC machining with additive manufacturing (3D printing) will likely reshape how parts are created, integrating both methods to optimize the manufacturing process, reduce waste, and boost design capabilities.
As industries increasingly focus on sustainability, CNC machining practices will evolve to include eco-friendly materials, energy-efficient processes, and waste-reduction efforts, reinforcing aluminum’s status as a recycling champion.
In conclusion, CNC machining for custom aluminum alloy parts presents a wealth of benefits that address many challenges in today’s industrial landscape. From precision and efficiency to adaptability and material utilization, this manufacturing technology is essential for various sectors, including aerospace, automotive, electronics, and medical devices.
As industries continue to evolve and seek innovative solutions, understanding the advantages and processes of CNC machining will empower manufacturers to leverage its potential for enhanced productivity and quality.
Reflecting on the state of today’s manufacturing technologies, it’s critical to recognize how CNC machining not only optimizes efficiency but also aligns with sustainable practices. Engaging with CNC machining technologies can yield significant returns on investment and open new avenues for product development.
We hope this blog has provided valuable insights into the importance of CNC machining for custom aluminum alloy parts. As industries move toward a future defined by precision and innovation, considering CNC machining as a fundamental component of your manufacturing strategy is essential.
Your thoughts and strategies on adopting CNC machining could be the key to unlocking the next level of success in your industry. Let’s embrace the future of manufacturing together!