Did you know that aluminum is the second most widely used metal in industrial applications, right after steel? Its lightweight nature, resistance to corrosion, and excellent overall mechanical properties have made it a popular choice for companies and sectors ranging from aerospace to automotive. However, producing custom aluminum alloy parts with precision and efficiency poses its own set of challenges. This is where CNC (Computer Numerical Control) machining comes into play.
In this comprehensive blog, we will explore the benefits of CNC machining for custom aluminum alloy parts in industrial applications, diving deep into the processes, advantages, best practices, and more. With a focus on providing detailed solutions to the challenges faced in this area, this guide aims to serve as a valuable resource for industries looking to leverage modern machining techniques.
—
What is CNC Machining?
Computer Numerical Control (CNC) machining is an automated manufacturing process that utilizes software to control machine tools. These machine tools can include lathes, mills, routers, and grinders. CNC machining allows for precision in creating complex shapes and high-quality parts by specifying every aspect of the machining process through a computer program.
How CNC Machining Works
The process begins with a computer-aided design (CAD) file, which contains the specifications and dimensions of the desired part. This electronic blueprint is then converted into a CNC program using computer-aided manufacturing (CAM) software. The CNC machine reads this program, guiding its movements with utmost precision to cut and shape the material.
Importance in Modern Manufacturing
CNC machining is critical in modern manufacturing due to its ability to enhance productivity and reduce manual errors. As industries increasingly push for efficiency, CNC machining remains at the forefront of innovation to meet these demands.
—
Common Types of Aluminum Alloys
Aluminum alloys are categorized into two main groups: wrought and cast alloys. Each type includes several subcategories based on their chemical composition and mechanical properties. Common alloy series include:
Mechanical Properties and Benefits
Aluminum alloys are prized for their lightweight, high strength-to-weight ratio, excellent corrosion resistance, and thermal and electrical conductivity. These traits make aluminum alloys suitable for applications requiring durability without adding excess weight.
Applications Across Industries
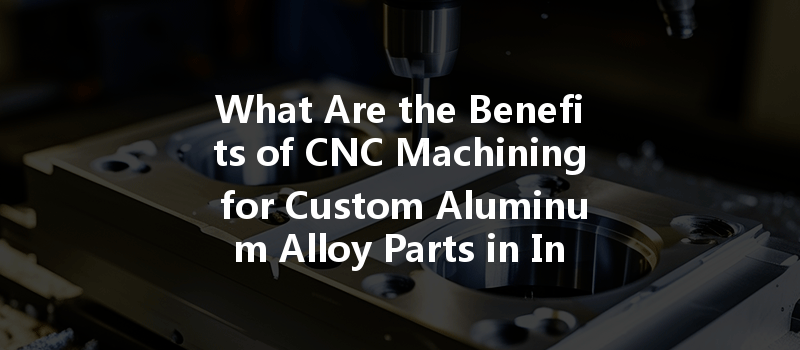
—
Design Considerations
When designing parts for CNC machining, it is essential to consider manufacturability. A well-thought-out design allows for shorter lead times, lower costs, and less waste. For instance, minimizing tight tolerances where possible can streamline production.
Machining Techniques
Common machining techniques include milling, turning, drilling, and electrical discharge machining (EDM). Each technique has specific strengths suited for different types of aluminum components.
Materials and Tooling
Using the right materials and tooling is critical for CNC machining. Carbide tools are often preferable for machining aluminum due to their durability and heat resistance.
—
Precision and Accuracy
One of the key advantages of CNC machining is its ability to produce parts with high precision and accuracy. CNC machines can consistently create complex geometries, ensuring parts meet stringent tolerances.
Cost-effectiveness
CNC machining can be more cost-effective than traditional machining methods, especially for large production runs. The rapid setup processes and automated operations lead to reduced labor costs and higher output rates.
Flexibility and Scalability
CNC machining operations can be easily adjusted to accommodate different designs, making it a flexible option suitable for both prototypes and full-scale production. This flexibility allows manufacturers to quickly respond to market demands.
Improved Lead Times
Because of automation and rapid production capabilities, CNC machining significantly reduces lead times. Parts can be produced overnight or within days, allowing companies to meet tight deadlines.
Reduced Waste
CNC machining uses material more efficiently than traditional methods. The precision of CNC reduces scrap rates and optimizes material usage, which is particularly crucial in industries where material costs are high.
Automated Customization
CNC machining allows for easy customization through programming. Manufacturers can switch between different designs and specifications without needing extensive retooling, enhancing operational efficiency.
—
Tool Wear
While machining aluminum is generally easier on tools compared to harder metals, tool wear can still be an issue, particularly with high-speed cutting. Regular monitoring of tool condition is essential to maintain quality.
Heat Management
As aluminum is an excellent conductor of heat, excessive heat during machining can lead to thermal deformation and affect the integrity of the part. Effective cooling systems and appropriate cutting speeds can mitigate this challenge.
Setup Complexity
Depending on the complexity of the part, CNC setup can be time-consuming. Load times, tool changes, and calibration processes are critical areas where good planning can help maintain efficiency.
Surface Finish Quality
Achieving a high-quality surface finish can be challenging with CNC machining. The selection of cutting tools, speeds, and feeds must be carefully managed to meet required finishes.
—
Selecting the Right Tools and Machinery
Choosing the correct tools is vital for successful CNC machining. Carbide end mills, face mills, and specialized cutting tools designed for aluminum can provide better results.
Optimizing Machining Parameters
Factors such as feed rate, cutting speed, and depth of cut should be optimized based on the specific alloy being machined. Tools should also be cooled properly during operation to enhance performance.
Quality Control Measures
Incorporating rigorous quality control measures within the manufacturing process helps catch defects early and reduces scrap rates. Regular calibration of machines is also crucial to maintaining accuracy.
Post-Processing Techniques
Post-processing techniques, such as anodizing, polishing, or coating, can enhance the performance and aesthetics of CNC machined parts. Understanding these techniques can add significant value to manufactured products.
—
Aerospace Industry
A leading aerospace manufacturer transitioned to CNC machining for their aluminum parts and realized dramatic reductions in production time while increasing accuracy. This shift allowed for more complex designs and lightweight components crucial for aviation.
Automotive Industry
An automotive company focused on electric vehicles used CNC machining to create custom battery casings from aluminum. The flexibility of CNC machining allowed rapid prototyping and the ability to tweak designs based on performance tests.
Consumer Electronics
CNC machining enabled a consumer electronics company to produce lightweight and highly durable enclosures for their gadgets. The precision allowed for a better assembly of internal components, resulting in improved product performance.
Medical Devices
In the medical field, CNC machining’s precision is unmatched. A medical equipment manufacturer produced custom aluminum components for surgical devices, ensuring both reliability and cleanliness.
—
Advancements in Technology
The future of CNC machining is characterized by three key trends: automation, smart technology, and improved software. New advancements in machine learning and AI will optimize machining processes, leading to even more efficient production cycles.
Sustainability in Manufacturing
Concern over sustainability has prompted manufacturers to examine waste production and energy consumption. CNC machining is evolving to include sustainable practices, such as minimizing waste and employing recycled materials.
Integration with Industry 4.0
As industries embrace smart manufacturing solutions, CNC machining is set to integrate closely with IoT technology, resulting in data-driven decision-making to enhance productivity and monitoring.
—
CNC machining stands at the intersection of innovation and precision, offering significant benefits for the manufacturing of custom aluminum alloy parts. The advantages, ranging from enhanced precision and reduced lead times to cost-effectiveness and reduced material waste, are crucial for businesses aiming to remain competitive in today’s fast-paced industrial landscape.
Understanding the challenges faced during CNC machining, along with best practices and emerging trends, will empower industries to make informed decisions for their manufacturing needs. As we continuously strive for innovation, CNC machining remains a cornerstone of modern manufacturing, paving the way for advanced, high-quality products in a range of applications.
In summary, investing in CNC machining for aluminum alloys not only offers immediate benefits but also prepares companies for the future of manufacturing. With the right knowledge, technology, and practices, industries can optimize their operations and enhance product reliability, performance, and sustainability. The implications of these advancements are profound—transforming how industries operate and how we approach modern manufacturing.