: A Material That Matters
Did you know that the choice of material can significantly affect the performance of precision parts produced by CNC machining? In industries where accuracy and reliability are paramount, the selection of the right material can mean the difference between a successful product and a costly failure. Among the myriad of materials available, 51 brass has garnered attention for its unique properties and advantages in CNC machining. In this blog, we will delve into the numerous benefits of using 51 brass as a material in the CNC machining process, exploring its mechanical properties, applications, and why it stands out for precision research and manufacturing.
The Significance of Material Selection in CNC Machining
Before we dive into the specifics of 51 brass, it’s essential to understand why material selection plays a crucial role in CNC machining. The right material ensures not just the durability of the machined parts, but also their performance in various applications. With CNC machining finding applications in aerospace, automotive, medical devices, and many more fields, the pressure to meet stringent specifications has never been higher.
Challenges in Material Selection
Selecting a material for CNC machining involves various challenges, including:
Considering these factors, 51 brass emerges as a viable option that balances quality, performance, and cost.
What is 51 Brass?
51 brass is a type of alloy primarily made of copper and zinc, characterized by a composition that typically ranges from 55% to 58% copper and 37% to 40% zinc. The balance of this alloy provides unique properties, making it ideal for various applications, especially in CNC machining.
Mechanical Properties of 51 Brass
The advantages of 51 brass can be attributed to its remarkable mechanical properties:
Advantages of Using 51 Brass in CNC Machining
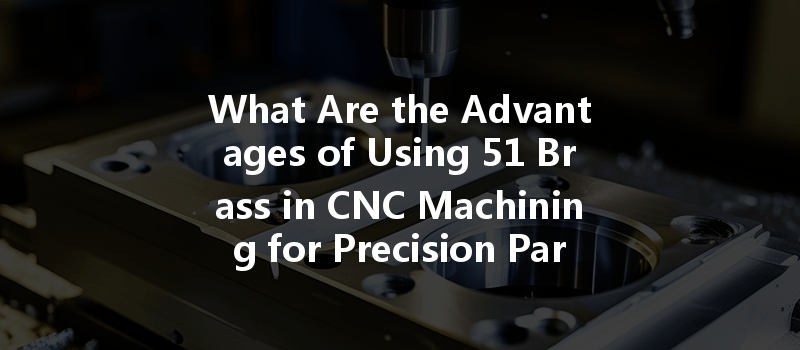
One of the standout features of 51 brass is its superior machinability. Unlike some harder materials, it allows for faster cutting speeds and reduces tool wear, which translates to lower machining costs and quicker turnaround times. Parts can be produced efficiently without compromising on quality.
When comparing 51 brass to more expensive materials, it becomes clear that its cost-effectiveness is a major advantage. Its mechanical properties and ease of machining help reduce production costs, making it an attractive option for manufacturers looking to optimize their budgets without sacrificing quality. When produced in large quantities, the cost per unit remains low, which is crucial for mass production.
51 brass provides consistent material properties across the production run, minimizing variations in the machined parts. This consistency ensures that precision engineering standards are met and helps manufacturers maintain high-quality controls. Parts machined from 51 brass remain reliable and perform well under various stresses, which reduces the need for frequent replacements or repairs.
The applications for 51 brass are extensive. From automotive components and plumbing fittings to electrical connectors and intricate mechanical parts, 51 brass finds uses in various fields. This versatility allows for its adoption in multiple sectors, thus broadening its appeal and usability.
In addition to its mechanical strengths, 51 brass also has an attractive golden yellow color, making it suitable for decorative applications. Its aesthetic appeal is beneficial in industries like jewelry and premium consumer goods, where appearance is often just as important as performance.
Addressing Common Challenges in CNC Machining with 51 Brass
While 51 brass has many advantages, it’s also important to be aware of the potential challenges that can arise during CNC machining. However, many of these challenges can be effectively managed through best practices:
Even though 51 brass is easier to machine, choosing the right cutting tools and speeds is crucial to avoid excess wear. Using high-speed steel or carbide tools, along with optimal feed rates, can enhance the tool’s lifespan and produce better-quality parts.
The chips formed during machining can affect surface finish and can cause tool damage if not managed properly. Implementing an efficient chip removal system or applying appropriate cutting fluids can help maintain the quality of the machined surface and prevent the accumulation of debris.
During machining, excessive heat can lead to warping or dimensional inaccuracies. Adequate cooling through cutting fluids or strategic cooling techniques should be utilized to dissipate heat effectively.
To ensure that parts machined from 51 brass meet specification tolerances, manufacturers should employ precise CNC programming and regular calibration of their equipment. This ensures high accuracy in part dimensions and overall performance.
: The Brass Standard in Precision Machining
In summary, 51 brass stands out as an excellent choice for CNC machining due to its superior machinability, cost-effectiveness, consistent quality, versatility, and aesthetic appeal. Understanding the unique benefits of this material allows manufacturers to elevate their products, meet stringent quality standards, and respond swiftly to market demands.
As high-tech industries continue to evolve, staying informed about material options like 51 brass is crucial for effective decision-making in product development. By considering the advantages outlined in this blog, your manufacturing processes can achieve enhanced efficiency and product performance. Whether you’re in aerospace, automotive, or another industry emphasizing precision parts, exploring the capabilities of 51 brass in CNC machining is a worthwhile consideration for improving your production strategies and ensuring operational excellence.