: An Eye-Opening Statistic
Did you know that the aerospace industry is projected to grow to $1 trillion by 2030? This dramatic expansion is primarily fueled by continuous advancements in technology, efficiency, and design. At the heart of this revolution lies an integral process: the use of CNC (Computer Numerical Control) prototypes. In an industry where precision, safety, and innovation coexist, CNC prototyping plays a pivotal role in streamlining design processes, accelerating production timelines, and enhancing overall product quality. But what exactly are the advantages of CNC prototypes in aerospace manufacturing, and how can they improve operational efficiency? In this comprehensive blog, we’ll delve into these questions and explore how CNC prototypes are transforming the aerospace sector.
Understanding CNC Prototypes in Aerospace
CNC prototypes are typically used to create functional models and components for testing prior to mass production. These prototypes serve as representations of the final product and offer valuable insights into performance, material properties, and design functionality. In the context of aerospace, where the stakes are particularly high due to safety regulations and complex engineering requirements, CNC prototypes serve several crucial purposes:
One of the most significant advantages of CNC prototyping is its speed. Traditional prototyping methods can take weeks, if not months, to complete. However, with CNC technology, prototypes can be produced in a fraction of that time—often within days. This rapid turnaround enables aerospace engineers to iterate and refine their designs quickly, which is essential for meeting tight project deadlines and adapting to changing specifications.
Aerospace components must meet stringent tolerance standards to ensure safety and functionality. CNC machines are guided by precise computer programs that result in minimal human error and consistent production quality. This level of precision is particularly important in aerospace applications, where even the smallest deviation can have catastrophic consequences.
While the initial investment in CNC machinery can be significant, the long-term savings are considerable. The ability to produce high-quality prototypes quickly reduces material waste and labor costs. Furthermore, the speed of CNC prototyping allows for faster product launches, enabling companies to capture market opportunities sooner.
The aerospace sector often requires components made from a variety of materials, including metals, plastics, and composites. CNC machining can accommodate a wide range of materials, allowing designers and engineers to explore different options for functionality, weight, and durability. This flexibility is particularly beneficial when testing new materials for specific applications.
CNC prototypes provide an avenue for engineers to validate design concepts before moving into mass production. By producing functional prototypes, teams can conduct rigorous testing under real-world conditions, identifying any potential issues and ensuring the end product meets all performance requirements. This reduces the risk of costly production errors and recalls.
In-Depth Solutions: Bridging the Gap Between Design and Reality
While the benefits of CNC prototypes in the aerospace industry are clear, let’s explore some specific applications and solutions that illustrate how they bridge the gap between design concepts and production realities.
Aerodynamic efficiency is a top priority in aerospace design, impacting fuel efficiency, performance, and safety. CNC prototypes allow engineers to test and refine aerodynamic shapes quickly. By creating prototypes of wing designs, fuselages, and other components, teams can perform wind tunnel tests to gather data on drag, lift, and overall performance.
For example, a leading aerospace company utilized CNC machining to develop a new aircraft wing profile. By rapidly creating and testing multiple designs, they identified a shape that reduced drag by 15%, resulting in significant fuel savings over the aircraft’s lifecycle.
The iterative design process is essential in the aerospace sector, where multiple revisions and refinements are often necessary. CNC prototypes facilitate this process by enabling quick adjustments and iterations based on testing feedback.
Consider the case of a new satellite system. Engineers initially developed a prototype using traditional methods. The lengthy timeline hindered their ability to iterate. However, after switching to CNC prototyping, they created several iterations in a matter of weeks. Testing and refinement cycles increased dramatically, leading to a final design that exceeded performance expectations while coming in under budget.
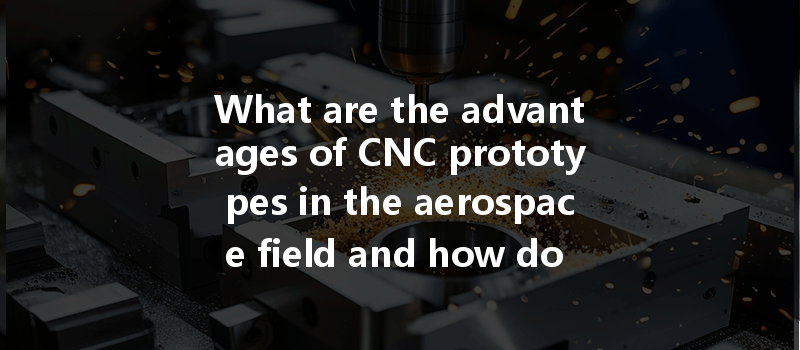
CNC prototyping fosters collaboration among various departments—design, engineering, and manufacturing—all working towards a common goal. By having tangible prototypes, team members can visually and physically assess designs, facilitating discussions and decisions.
For example, mechanical engineers and production managers can identify manufacturability issues early in the design phase, reducing miscommunication that often arises from sketch-based design reviews. This collaborative approach ultimately leads to reduced production costs and improved product quality.
Overcoming Challenges in CNC Prototyping
While the advantages of CNC prototypes in aerospace are numerous, the process is not without its challenges. Here are some common hurdles aerospace companies may face and suggested solutions:
Challenge: The investment in CNC machinery and software can be substantial, posing a barrier for some companies.
Solution: Consider partnering with established CNC prototyping firms that offer contract manufacturing services. This arrangement allows companies to leverage CNC technology without the overhead costs associated with purchasing and maintaining the equipment.
Challenge: Aerospace components often have intricate designs that can be difficult to manufacture.
Solution: Invest in advanced CAD (Computer-Aided Design) and CAM (Computer-Aided Manufacturing) software. These tools can simplify the design process and enhance manufacturability, enabling easier production of complex prototypes.
Challenge: Some materials may pose challenges during the CNC machining process, such as tearing or warping.
Solution: Work closely with material engineers to identify appropriate materials and machining parameters for specific prototypes. Conduct thorough testing at each stage to optimize settings and achieve the desired results.
Case Studies: Successful Implementations of CNC Prototyping
Case Study 1: Boeing and the 787 Dreamliner
Boeing incorporated CNC prototyping extensively in the development of the 787 Dreamliner. By using rapid CNC prototyping, they created numerous wing and fuselage components that allowed for early testing of weight distribution and aerodynamic efficiency. As a result, Boeing could streamline the design process and achieve a weight reduction of 20% compared to previous models, leading to improved fuel efficiency and reduced environmental impact.
Case Study 2: SpaceX and Reusable Rockets
SpaceX utilized CNC prototyping techniques to develop reusable rocket components for its Falcon 9 launch vehicle. The rapid prototyping capabilities ensured swift iterations of rocket designs, allowing for extensive testing in a shorter timeframe. This pushed technological boundaries forward, culminating in the world’s first operationally reusable orbital rocket, significantly reducing launch costs.
: The Future of CNC Prototyping in Aerospace
CNC prototypes are transforming the aerospace industry in remarkable ways. Their advantages—rapid production, enhanced precision, cost-effectiveness, and collaborative potential—enable teams to innovate, iterate, and deliver high-quality products. As we advance towards an increasingly technology-driven aerospace landscape, CNC machining will become even more integral in navigating complexities and challenges.
Reflecting on the pivotal role that CNC prototypes play in the aerospace sector, companies must embrace these technologies to remain competitive, efficient, and innovative. With the continued growth of the aerospace industry, understanding and utilizing CNC prototyping can make all the difference in adapting to new challenges and elevating successes.
The implications of this discussion extend beyond mere manufacturing; they underscore the importance of precision, safety, and responsiveness in an industry that quite literally reaches for the sky. As aerospace continues to evolve, the strategic integration of CNC prototyping must remain at the forefront of design and production paradigms. Embracing these advancements is not just a necessity; it’s an opportunity to shape the future of air travel and exploration.