When we think about the aerospace industry, we often picture advanced spacecraft, sleek jets, and the latest aviation technologies—innovations that push the boundaries of human achievement. But behind every great leap in aerospace technology lies a complex and meticulous development process, where precision, efficiency, and reliability are not merely goals; they are requirements. Did you know that the aerospace sector is projected to be worth over $1 trillion by 2030, according to industry analyses? This astonishing figure underscores the critical importance of not only new technologies but also the methods through which they are developed.
In this blog, we will delve into the fascinating world of Computer Numerical Control (CNC) machining and prototyping in the aerospace industry. We will explore the advantages of using CNC prototypes over traditional machining methods, elucidate the processes involved, and discuss how CNC technology can lead to significant improvements in quality, speed, and cost-efficiency.
—
Understanding CNC Prototyping
CNC machining involves using computer software to control machine tools in the manufacture of parts. This technology has been a game-changer in various industries, but it holds particular significance in aerospace due to the specific demands for precision, material properties, and compliance with stringent safety regulations.
What is CNC Prototyping?
CNC prototyping refers to creating prototypes using CNC machines, which can be programmed to produce complex geometries with extreme accuracy. The process allows engineers and designers to quickly generate prototypes for testing and evaluation before moving on to full-scale production.
Traditional Machining vs. CNC Prototyping
Traditional machining methods, such as manual milling or turning, often involve a higher likelihood of human error, longer lead times, and difficulties in reproducing complex geometries. In contrast, CNC machining allows for:
Key Advantages of CNC Prototypes in Aerospace
In aerospace, every millimeter counts. Any deviation in a part can have dire consequences, from function and safety to compliance issues. CNC machining’s ability to create parts with high precision ensures that each prototype will conform to exact specifications. The use of 3D CAD software aids in designing parts that can be replicated accurately by the CNC machine, maintaining consistency throughout the production process.
Time is of the essence in aerospace development. Traditional methods can involve multiple iterations and lengthy set-up processes, making the prototyping phase sluggish. CNC prototyping can significantly cut lead times through automated processes and the immediate capability to produce multiple prototypes concurrently. This acceleration allows teams to focus on design iterations more rapidly, facilitating faster project completion.
While the initial investment for CNC technology may be higher compared to traditional methods, the return on investment (ROI) often outweighs the costs. The accuracy of CNC machines reduces material waste, while accelerated production times lower labor costs. Moreover, the swift transition from prototype to full-scale production can lead to cost savings across the entire project.
CNC prototyping allows aerospace engineers to experiment with various designs and materials without significant retooling costs. Engineers can rapidly prototype components in different materials (like aluminum, titanium, and advanced composites) to evaluate performance, strength, weight, and durability. This flexibility is particularly vital in aerospace, where material choice directly impacts performance and compliance with regulatory standards.
Prototyping is not just about creating a physical part; it’s also about testing and validation. CNC-produced prototypes can be put through rigorous testing to evaluate functionality and performance under various conditions. This capacity enables engineers to pinpoint issues early in the development process, reducing risks associated with late-stage errors.
CNC prototyping seamlessly integrates with other advanced technologies, such as 3D printing and modeling simulation software. Engineers can use advanced modeling to predict how a part will behave under various conditions, then employ CNC machining to generate highly accurate prototypes for physical testing. This interconnectedness enhances the overall precision and efficiency of the design-to-production workflow.
Detailed Process: CNC Prototyping in Aerospace
Initial Conceptual Design
The process begins with an initial design idea that is often derived from rigorous requirement analysis and brainstorming sessions. During this phase, engineers will consider the functional requirements, aesthetic factors, material characteristics, and manufacturing feasibility.
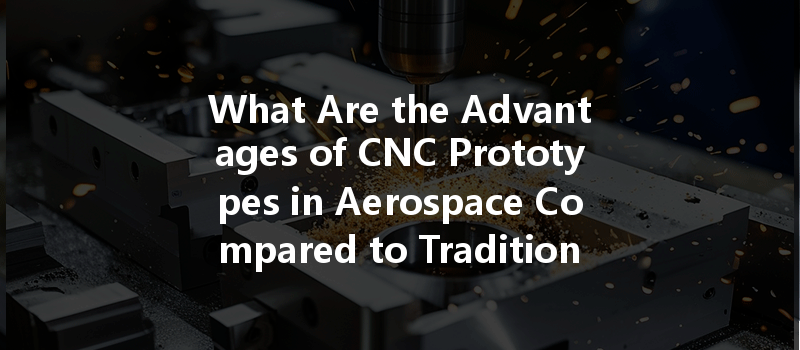
CAD Modelling
Once the initial concept is defined, the next step is to create a CAD model of the part or assembly. Computer-Aided Design (CAD) software allows engineers to visualize the part in 3D, refine its design, and prepare it for CNC machining. CAD programs support detailed simulations, which can help predict how the designed part will perform in the real world.
CAM Programming
Following the CAD modeling, engineers will use Computer-Aided Manufacturing (CAM) software to convert the CAD design into instructions that the CNC machine can understand. This stage involves determining the machining operations, tool paths, feed rates, and cutting parameters necessary to fabricate the part.
CNC Machining
Once programmed, the CNC machine begins the machining process. Depending on the material and complexity of the part, this process may involve several types of operations, including milling, turning, drilling, and grinding. The machine will work directly from the CAM-generated code, ensuring precision and accuracy throughout.
Quality Control and Testing
Post machining, the prototype undergoes quality control checks to ensure it meets the specified tolerances and requirements. Coordinate Measuring Machines (CMMs) and other inspection tools may be employed for this process. Parts may also be subjected to functional testing to see how they perform under realistic conditions.
Iteration and Feedback
The feedback from quality control and testing allows engineers to make informed decisions on design adjustments. CNC prototyping enables rapid iterations, which are crucial for improving part performance and ensuring compliance with aerospace industry standards.
—
Challenges and Considerations in CNC Prototyping
While CNC technology offers various advantages, it is not without its challenges. Here are key factors to consider when implementing CNC prototyping in aerospace:
Maintaining Precision with Complex Geometries
As designs become more complex, maintaining precision can become challenging. Engineers and machinists must collaborate closely throughout the design and machining process to ensure that all specifications are met without sacrificing quality.
Material Limitations
Although CNC can handle a variety of materials, each material has its own machining characteristics. Engineers must understand these properties to choose suitable cutting speeds, tool types, and techniques to avoid issues such as tool wear or material deformation during machining.
Initial Costs and Investment
The up-front costs for CNC machines can be significant, which may deter smaller aerospace firms. However, the long-term savings in time and material costs often outweigh these initial investments, making the shift to CNC prototyping worthwhile.
Skilled Workforce
Operating CNC machines and interpreting CAD/CAM software requires a skilled workforce. Continuous training and development are crucial in ensuring that personnel can maximize the benefits of CNC technology.
: Embracing the Future of Aerospace Prototyping
CNC prototypes have undeniably transformed the aerospace industry, providing a pathway to innovation through enhanced precision, speed, and flexibility. As this sector continues to grow rapidly, utilizing advanced technology will be pivotal in developing the next generation of aerospace solutions.
Why Should You Care?
The implications of CNC prototyping extend beyond the walls of aerospace companies. They carry weight in improving passenger safety, reducing environmental impacts through efficient designs, and delivering cutting-edge technologies. Understanding these processes is crucial not just for aerospace professionals but also for consumers who rely on these innovations for safe and sustainable travel.
In a world where technology continues to advance at an unprecedented rate, staying informed about these intricacies and their benefits will empower professionals and enthusiasts alike. The future of aerospace relies on our ability to leverage technologies like CNC machining effectively, and with it, we can continue to soar to new heights in engineering excellence.
Thank you for joining me on this exploration of CNC prototyping in aerospace. Here’s to pushing the boundaries of what’s possible!