*
Did you know that 70% of manufacturers believe that adopting advanced manufacturing techniques, such as CNC precision machining, significantly enhances their competitive edge? In today’s fast-paced industrial landscape, precision and efficiency are no longer optional—they are essential for survival. As technology continues to advance, businesses are challenged to produce high-performance parts that meet stringent quality standards while staying agile in their operations. This is where CNC (Computer Numerical Control) precision machining comes into play, revolutionizing how parts are manufactured across various industries.
In this comprehensive blog, we will delve deep into the multifaceted advantages of CNC precision machining, the challenges it addresses, and how it has become a cornerstone in producing high-performance parts. Whether you’re a seasoned manufacturer or a newcomer in the industry, understanding these benefits can help you make informed decisions that align with your business goals.
CNC precision machining refers to the automated control of machining tools and cutting tools by a computer program. The process encompasses various machining operations, including milling, turning, and grinding, to create parts with extraordinary accuracy.
The key elements of CNC precision machining include:
2.1 Enhanced Efficiency and Reduced Production Time
CNC machines operate continuously, often running 24/
2.2 Increased Design Flexibility
In the past, many designs were constrained by the abilities of manual machines. CNC precision machining allows for complex designs that were previously considered impractical. This flexibility enables designers to innovate and create high-performance parts tailored to specific requirements without increasing production costs.
2.3 Improved Quality and Consistency
Quality control is paramount in manufacturing. CNC machining eliminates human error, resulting in parts that are uniform in dimension and quality. For high-performance applications, such as aerospace or automotive industries, consistency is vital. Customers can trust that every produced part meets the same high standards.
2.4 Cost-Effectiveness
While the initial investment in CNC machinery can be significant, the long-term cost savings are notable. The reduction in labor costs, the minimization of waste due to precise cuts, and the elimination of the need for reworks lead to substantial savings over time.
2.5 Minimized Waste Material
CNC machines utilize advanced techniques to optimize the use of raw materials. Because they can be programmed to minimize waste, manufacturers can significantly reduce excess material costs and decrease their environmental footprint.
2.6 Accessibility and Customization
With advancements in CNC technology, even small production runs or customized parts can be produced cost-effectively. Businesses can now offer tailored solutions to clients without the burdensome costs associated with traditional manufacturing methods.
2.7 Safer Work Environment
CNC machines are designed to operate with minimal human intervention. This automated approach helps create a safer work environment by reducing the risk of injuries that can occur with manual machining processes.
CNC precision machining boasts a wide range of applications across different industries, tailoring solutions to meet specific operational needs.
3.1 Aerospace Industry
In aerospace, precision is non-negotiable. CNC machining provides the high tolerances required for engine components, structural parts, and even specialized fixtures, all crucial for the safety and performance of aircraft.
3.2 Automotive Industry
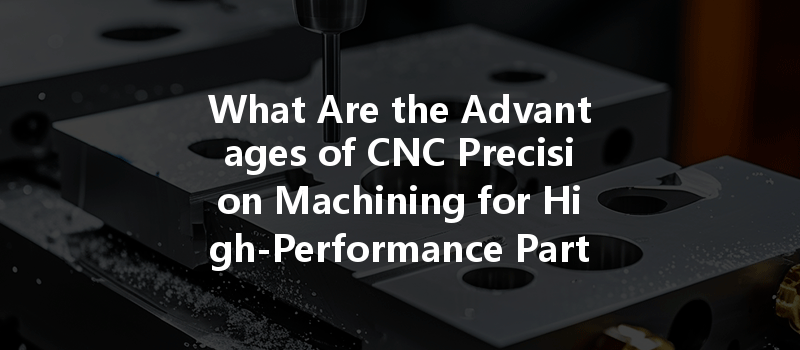
The automotive sector relies heavily on CNC precision machining for producing intricate engine parts, transmission components, and custom interiors. The lightweight materials used in modern cars can be accurately and efficiently machined, a crucial factor in enhancing performance and fuel efficiency.
3.3 Medical Equipment Manufacturing
The demands of the medical field require parts that not only meet precision standards but are also made from biocompatible materials. CNC machining enables manufacturers to produce surgical instruments, implants, and various medical devices with the necessary precision and care.
3.4 Electronics Industry
CNC machined parts play a pivotal role in creating cases, brackets, and connectors used in electronic devices. Precision machining ensures that tiny components fit together perfectly, which is critical for device functionality.
3.5 Defense Industry
In defense, the integrity of parts can be a matter of safety. CNC precision machining produces components that can withstand extreme conditions, thus ensuring the reliability of military hardware.
While CNC precision machining offers numerous advantages, several challenges also arise.
4.1 Initial Investment
The cost of purchasing CNC machinery can be a hurdle for many manufacturers. However, looking into leasing options or investing in refurbished machines could be viable solutions. Engaging with knowledgeable suppliers can also help identify the right equipment suited to your budget and needs.
4.2 Skill Gap
Operating CNC machinery requires specific technical skills. It is crucial to invest in employee training or partner with educational institutions to enhance the skills of your workforce. This ensures that your team is well-equipped to handle the technology effectively.
4.3 Maintenance and Downtime
CNC machines require regular maintenance to function efficiently. Establishing a preventive maintenance schedule can help minimize downtime and prolong the life of the machinery. In case of machine failure, having a reliable service partner can ensure quick resolution.
4.4 Data Security
As CNC machines are increasingly connected to networks, data breaches become a concern. Prioritizing cybersecurity measures and backing up data can mitigate risks.
As technology continues to advance, CNC precision machining is poised for further evolution. The integration of artificial intelligence (AI), machine learning, and the Internet of Things (IoT) will drive innovations in this field.
5.1 Smart Manufacturing
The introduction of IoT in CNC systems allows for real-time monitoring and management. Automated adjustments can optimize production efficiency and resource utilization, leading to significant savings.
5.2 Advanced Materials
Emerging advanced materials, such as composites and lightweight alloys, create new challenges and opportunities. CNC precision machining methods can be adapted to handle these materials effectively, opening up new applications.
5.3 Sustainability
With growing awareness of environmental issues, the shift towards sustainable manufacturing practices is inevitable. CNC machining can contribute to this trend by reducing waste and energy consumption through advanced technologies.
*
In summary, CNC precision machining is not just a manufacturing method; it is a transformative approach that addresses the challenges of modern manufacturing. From enhancing efficiency and flexibility to ensuring high quality and reduced waste, its advantages are manifold.
The insights covered in this blog reflect the significance of embracing CNC precision machining, particularly for those involved in producing high-performance parts. As you consider the future of your manufacturing processes, it’s vital to understand the critical role that CNC machining plays in not only meeting today’s demands but also anticipating and evolving with future industry trends.
Ultimately, investing in CNC precision machining can lead to a competitive advantage, opening avenues for innovation and driving sustainable growth. As the manufacturing landscape continues to evolve, equipping yourself with knowledge of this vital technology is worth your while. The future of manufacturing is undeniably precise—and as we continue forward, the potential for CNC machining remains limitless.