In our fast-paced world of advanced manufacturing, the techniques and technologies employed to create products have evolved dramatically. One of the most significant advancements is in computer numerical control (CNC) machining, a transformative process that has redefined how we produce high-precision parts. To illustrate the impact of CNC machining, consider this startling statistic: according to a report by the International Data Corporation (IDC), 70% of all manufacturing companies report that their productivity has significantly increased due to the adoption of CNC technology. This statistic emphasizes that the implications of CNC machining extend far beyond mere convenience — it has become a linchpin in the quest for efficiency, precision, and quality in manufacturing.
The Rise of CNC Machining in Manufacturing
A Brief Overview
CNC machining refers to the process of using computer-controlled machinery to remove material from a workpiece to produce desired shapes and dimensions. This technology has roots tracing back to the 1940s when the first numerical control machines were developed to utilize punched tape. Over the decades, advancements in computers revolutionized this technology, culminating in the sophisticated CNC systems that dominate the industry today.
Understanding High-Precision Aluminum Parts
Why Aluminum?
Aluminum, known for its lightweight properties, corrosion resistance, and excellent machinability, is a favored material in industries such as aerospace, automotive, and electronics. The demand for high-precision aluminum parts is ever-increasing due to the material’s role in improving energy efficiency, reducing weight, and enhancing overall performance in various applications. To achieve these benefits, manufacturers must harness the capabilities of precision machining.
Key Characteristics of High-Precision Machining
High-precision machining involves producing parts with tight tolerances, keen attention to detail, and superior surface finishes. Tolerances often range from ±0.01 mm to ±0.005 mm, pushing the limits of engineering capabilities. This level of precision is vital in applications like aerospace components, where even slight variations can have catastrophic consequences.
Advantages of CNC Machining for High-Precision Aluminum Parts
One of the primary advantages of CNC machining is its ability to produce extraordinarily accurate parts. Computer-controlled machines can replicate designs and tolerances with an accuracy of up to 0.001 inches. This precision is vital for high-performance components, where even a minor deviation can lead to functional failure or safety hazards.
CNC machines can replicate production runs with impeccable consistency. Once a program is set up to produce a particular part, it can be run multiple times with identical results. This consistency is unparalleled in manual machining, where human error can introduce discrepancies over time.
CNC machining is far more efficient than traditional machining methods. The automation of the machining process allows for reduced setup times, faster production cycles, and less manual labor. This efficiency translates into lower operational costs and shorter lead times for customers.
CNC machines can be programmed to perform various machining tasks, including milling, turning, drilling, and grinding. As a result, manufacturers can adapt their machines to produce different parts or components without the need for extensive retooling or downtime. This versatility makes CNC machining a vital choice in rapidly evolving industries.
Modern CNC machines can handle complex geometries and intricate designs that are impossible to achieve through manual machining methods. This capability enables manufacturers to push the boundaries of innovation in product design, leading to more durable and efficient products.
While the upfront costs of CNC machinery may seem high, their long-term benefits outweigh these expenses. The reduced labor, increased efficiency, and decreased waste ultimately lead to cost savings that can benefit businesses significantly. Additionally, the ability to produce high-quality parts on-demand minimizes the need for extensive inventory management.
CNC machining can seamlessly integrate with other advanced technologies, such as computer-aided design (CAD) and computer-aided manufacturing (CAM), to enhance the overall manufacturing process. This integration allows for real-time monitoring and adjustments, ensuring optimal production quality and efficiency.
The CNC Machining Process for Aluminum Parts
Step 1: Design and Programming
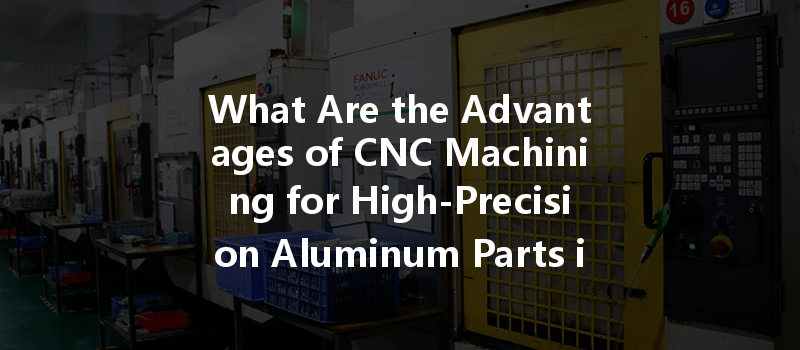
The CNC machining process begins with designing the part using CAD software. Engineers create precise 3D models that outline every detail of the part. Once finalized, the design is translated into G-code, a programming language that instructs the CNC machine on how to create the part.
Step 2: Material Selection
Choosing the right aluminum alloy is crucial to achieving the desired properties in the final product. Depending on the application, manufacturers often select from various aluminum grades, including 6061, 7075, and 5052, each offering distinct mechanical characteristics.
Step 3: Machining Operations
Once the machine is programmed and the material is secured, the machining process can begin. CNC machines use various operations, including:
Step 4: Quality Control
Quality control is an integral part of the CNC machining process. Parts are regularly inspected during production using advanced measurement technology (coordinate measuring machines and laser scanners) to ensure they meet tolerances.
Step 5: Finishing Treatments
After machining, parts may require finishing treatments to enhance their properties or aesthetics. Popular options include anodizing, which adds a protective layer and improves corrosion resistance, or polishing for a smooth surface finish.
The Challenges of CNC Machining Aluminum Parts
While CNC machining offers numerous advantages, challenges remain, particularly in the context of high-precision parts production:
Aluminum, while easier to machine than many metals, can produce chips that lead to tool wear. Manufacturers must regularly monitor and replace cutting tools to maintain quality and precision.
CNC machining generates heat, which can affect both the workpiece and the tools. Effective cooling strategies or machining strategies must be employed to manage this heat effectively.
The cost of CNC machines and the associated software can be substantial. Businesses need to weigh their investments against the potential productivity and quality improvements.
In an industry where precision, efficiency, and quality are non-negotiable, CNC machining for high-precision aluminum parts has become an indispensable element in modern manufacturing. The advantages it offers—accuracy, repeatability, efficiency, versatility, complexity handling, cost-effectiveness, and integration with advanced technologies—point toward a future where CNC machining continues to thrive.
Understanding the CNC machining process is essential for manufacturers who wish to leverage its benefits effectively. The journey begins with design and programming, moves through the machining operations, and ends with thorough quality control and finishing treatments. Despite the challenges posed by tool wear, heat management, and initial financial investments, the long-term rewards make CNC machining a crucial ally in producing high-precision components.
This blog underscores the importance of CNC machining in an evolving manufacturing landscape. As industries strive for excellence and innovation, embracing CNC technology isn’t just a strategic option; it’s an essential pathway to achieving superior quality and efficiency in producing high-precision aluminum parts. The time has come to recognize the potential of CNC machining and consider how it can elevate your manufacturing processes.