Did you know that aluminum is the most widely used non-ferrous metal in the world? According to the Aluminum Association, the demand for aluminum is expected to increase by over 30% in the next decade, driven particularly by industries such as automotive, aerospace, and electronics. This projection emphasizes the ongoing need for innovative manufacturing processes, including CNC machining, to meet the growing demand. In this blog post, we will delve into the advantages of CNC machining for custom aluminum alloy parts and provide a comprehensive understanding of how this advanced method can address various industry challenges.
CNC (Computer Numerical Control) machining is an automated manufacturing process where pre-programmed software controls CNC machinery in the production of various precision parts and components. This technology transforms ideas into tangible products with severe precision, versatility, and efficiency. But why exactly is CNC machining becoming increasingly favored for custom aluminum alloy parts?
Aluminum alloys are made by combining aluminum with other elements to enhance specific properties, making them suitable for various applications. These elements can include copper, magnesium, manganese, silicon, and zinc. The result is a material that possesses unique characteristics such as improved strength, corrosion resistance, and enhanced workability, making it ideal for manufacturing.
Aluminum alloys are favored by manufacturers due to their lightweight nature, strong strength-to-weight ratio, and impressive resistance to corrosion. These properties make them perfect for various industries, especially where weight and durability matter, such as in aerospace and automotive applications. By using aluminum alloys, manufacturers can reduce energy use and improve performance while adhering to sustainability goals.
The CNC machining process involves several core steps, including:
As we explore the advantages of CNC machining for custom aluminum alloy parts, it’s vital to recognize how these benefits cater to current industry demands.
5.1 Precision and Accuracy
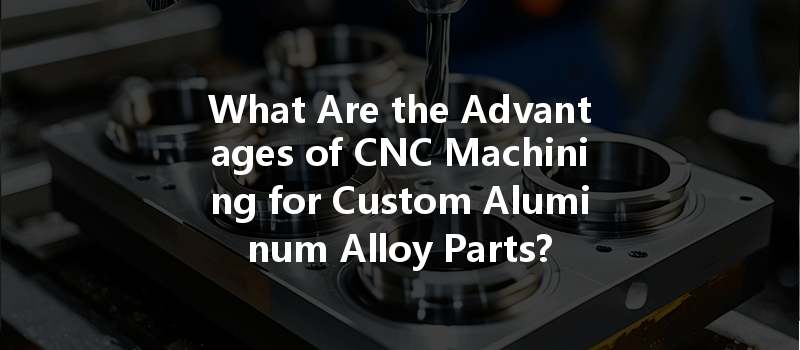
One of the most significant advantages of CNC machining is the high precision it offers. Manufacturers can create intricately designed parts that meet exact dimensions and tolerances without compromising quality. The programmed machinery minimizes the risk of human errors prevalent in manual machining, hence enhancing accuracy exponentially.
5.2 Flexibility and Customization
CNC technology allows for extensive flexibility. Whether producing a small batch of custom parts or a large-scale production run, CNC machines can adapt quickly. It can accommodate various designs, materials, and alterations, enabling manufacturers to customize parts to narrower specifications tailored to distinct applications.
5.3 Efficiency and Speed
Time is a crucial factor in manufacturing. CNC machining significantly reduces the time needed to produce parts. Once programming is complete, CNC machines can operate continuously without breaks, leading to faster turnaround times in production schedules. This efficiency also bolsters business responsiveness to market demands.
5.4 Cost-Effectiveness
Although initial setup costs may be higher for CNC machining, the long-term savings are substantial. High precision reduces waste material, and the efficiency of the process minimizes labor costs. Additionally, the scalability of CNC machining allows manufacturers to keep production costs low for larger orders, enhancing overall profitability.
5.5 Repeatability and Scalability
With CNC machining, the ability to replicate parts precisely can be done indefinitely. Once the design is programmed into the system, the same calculations and operations are repeated reliably to produce identical parts with consistent quality. This repeatability ensures that larger production runs maintain uniformity and quality standards.
Numerous industries are already benefiting from the advantages of CNC machining for aluminum alloys. Some key sectors include:
While CNC machining offers many advantages, it also comes with challenges, such as:
To ensure successful CNC machining of aluminum alloy parts, consider the following best practices:
Understanding the advantages of CNC machining for custom aluminum alloy parts provides insight into how this method not only addresses current manufacturing challenges but sets the stage for future innovations. The precision, flexibility, efficiency, and repeatability associated with CNC machining make it a formidable technique that continues to shape industry standards.
In a world where customization and speed are pivotal, businesses that embrace CNC machining technology position themselves favorably against competitors. The ongoing demand for aluminum and its alloys emphasizes the importance of adopting efficient, advanced machining techniques to stay relevant in the marketplace.
This blog serves as a reminder that exploring innovative manufacturing processes like CNC machining can streamline operations, reduce costs, and enhance product quality. As the landscape of manufacturing evolves, understanding these methodologies becomes vital for sustainable growth and success in a dynamic market.