Did you know that polycarbonate (PC) is one of the most widely used thermoplastic polymers in the world, and its versatility is unmatched in various applications? From eyewear lenses to optical disks and automotive components, polycarbonate holds its ground as an excellent material choice. Within the world of CNC machining, polycarbonate has become increasingly popular for prototyping due to its unique characteristics. However, while it boasts many advantages, it also comes with certain disadvantages that designers and manufacturers must carefully consider.
In this comprehensive blog, we will delve into the advantages and disadvantages of using polycarbonate for CNC prototypes. We will explore its properties, applications, best practices, potential challenges, and even tips to optimize CNC machining processes. By the end of this article, you will have a clear understanding of whether polycarbonate is the right choice for your CNC prototyping needs.
Properties of Polycarbonate
Polycarbonate is renowned for its high impact resistance, which is significantly greater than that of glass and other materials. This quality makes it an ideal candidate for applications requiring durability and toughness.
With a light transmittance exceeding 90%, polycarbonate offers excellent optical clarity. This property makes it a popular choice for applications involving lenses or visual displays.
Polycarbonate has the ability to withstand a considerable amount of heat, with a glass transition temperature of around 147°C (297°F). This feature enables it to maintain physical integrity under higher temperatures.
Special coatings can be applied to enhance UV resistance in polycarbonate sheets. This modification makes them suitable for outdoor applications, preventing yellowing and degradation over time.
Compared to glass and many metals, polycarbonate is relatively lightweight, making it easier to handle and install.
Polycarbonate can be shaped, cut, and finished using CNC machining techniques. Its lower density allows for faster processing times.
Advantages of Using Polycarbonate in CNC Prototypes
One of the standout benefits of using polycarbonate for CNC prototypes is its durability. With its high impact resistance, components made from polycarbonate can endure rigorous conditions without compromising their structural integrity. This characteristic is particularly advantageous for prototypes used in rigorous tests or simulations, providing accurate data for product iterations.
While the initial raw material cost of polycarbonate may be higher compared to other plastics, its durability and longevity contribute to lower long-term costs. The investment in a polycarbonate CNC prototype can lead to reduced failure rates and less frequent replacements.
Polycarbonate’s adaptability enables it to be used across a wide array of industries, including automotive, electronics, medical devices, and consumer products. Its ability to be tailored for different specifications makes it a flexible choice for diverse applications.
For visual prototypes or components that need to be aesthetically pleasing, polycarbonate’s clear and glossy finish can enhance the overall appearance. It allows designers to showcase their product designs without the need for extensive finishing processes.
Polycarbonate’s fast machining capabilities facilitate rapid prototyping. This enables designers and engineers to generate and test iterations of their designs quickly, speeding up development cycles and time to market.
Polycarbonate parts can be easily painted, coated, or bonded with other materials. These finishing techniques add unmatched versatility, helping prototypes meet aesthetic and functional requirements.
Disadvantages of Using Polycarbonate in CNC Prototypes
One of the primary drawbacks of polycarbonate is its susceptibility to scratches compared to materials like acrylic or glass. While it is tough, the surface can be easily damaged, outpricing polished finish aesthetics.
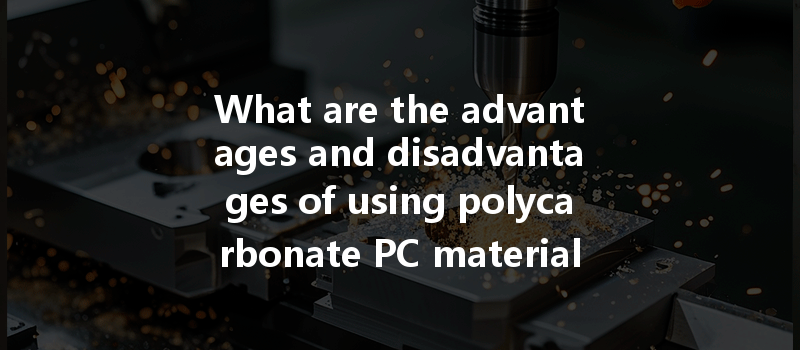
Polycarbonate may develop stress cracks if subjected to extensive mechanical stress or extreme environmental conditions. Therefore, careful consideration must be given to the design of the prototype to mitigate this risk.
Certain chemicals can adversely affect polycarbonate, leading to degradation or discoloration. Sensitive applications should ensure that the materials will not come into contact with corrosive substances.
Though polycarbonate can lead to cost savings in the long run, the original machining and processing costs may be higher than other materials due to specific tooling requirements and slower cutting speeds for thicker materials.
The environmental footprint of polycarbonate production can be significant. Designers may need to consider more eco-friendly alternatives if sustainability is a primary concern in their projects.
Best Practices for CNC Machining Polycarbonate
Using the correct cutting tools is essential. Carbide-tipped tools work best as they can cut through polycarbonate without generating excessive heat, which can cause melting or chipping.
Using the right cutting speeds and feed rates is crucial for maintaining the integrity of polycarbonate prototypes. Slower speeds can help minimize heat buildup and prevent melting during the machining process.
Introducing coolant while machining polycarbonate can help dissipate heat and minimize surface melting. Water-soluble lubricants can also assist in reducing friction during cutting operations.
Allowing the coefficient of thermal expansion to stabilize is imperative. Preheating the material slightly before CNC machining can reduce the risk of warping and increase accuracy.
Avoiding sharp bends or tight radii in designs can help mitigate stress and protect against cracking. Always aim for smoother transitions in the design phase.
Post-processing procedures such as sanding, polishing, or applying protective coatings can enhance performance while providing a visually appealing finish.
Challenges and How to Overcome Them
Consider applying a hard coating or using a surface treatment procedure that enhances scratch resistance. This can be an effective way to increase the durability of the prototypes.
Designing in a way that eliminates point loads or sharp angles can reduce stress concentrations. Engineers can also conduct tests to ascertain the ultimate tolerance levels of prototype materials.
Conduct extensive research on the chemicals the prototypes will encounter. A diversified testing phase will ensure the chosen materials can withstand exposures without adverse effects.
In conclusion, polycarbonate materials present a wealth of advantages for CNC prototyping, such as unparalleled durability, exceptional aesthetic quality, and swift machining capabilities. However, they are not without challenges, as their limitations in scratch resistance and chemical sensitivity pose significant considerations.
When weighing the decision to employ polycarbonate in CNC prototypes, it’s vital for engineers and designers to evaluate the specific requirements and constraints of their projects. By following best practices in machining and addressing potential challenges, users can optimize the strengths of polycarbonate in their prototyping endeavors.
This blog post emphasizes the importance of making informed choices in material selection for CNC prototyping. Understanding the trade-offs can lead to innovative solutions, advancing projects more effectively and efficiently.
Considering the multifaceted applications across industries, polycarbonate’s suitability will ultimately depend on the precise requirements of each project. It is imperative for stakeholders to focus on adaptability, functionality, and aesthetics, ensuring the prototypes meet their intended needs while balancing potential ethical and environmental considerations. As technology continues to evolve, polycarbonate stands a strong chance of cementing itself as a staple in CNC machining, reinforcing the vital role that informed decisions play in shaping our material world.