Did you know that copper is one of the most versatile metals widely used in various industries, from electronics to construction? In fact, it’s not only prized for its excellent electrical conductivity (the highest of all non-precious metals) but also for its resistance to corrosion. However, when it comes to CNC machining—a method where precision meets efficient manufacturing—copper can become susceptible to corrosion, particularly if proper processes are not followed. This article aims to dive deep into the fascinating interplay between CNC machining and copper corrosion, identifying the main causes and providing detailed solutions to this pressing issue.
Understanding Copper Corrosion in CNC Machining
Copper corrosion refers to the deterioration of the metal due to environmental factors, chemical reactions, or improper machining techniques. Post-CNC machining, exposure to air, moisture, or harmful substances can accelerate this corrosion process. Understanding why corrosion occurs is essential for developing effective preventative measures.
Common Causes of Increased Copper Corrosion After CNC Machining
Effective Strategies for Preventing Copper Corrosion
Now that we understand the causes of copper corrosion after CNC machining let’s explore proven strategies for prevention.
Selecting the right tools for CNC machining copper is crucial in minimizing corrosion risks. Tools with a high rake angle reduce cutting forces, thus generating less heat. Using coated tools, like TiN (Titanium Nitride), can also protect the copper surface from wear and oxidation.
Adjusting the feed rates, speeds, and depth of cuts during CNC machining can influence the heat generated and the amount of strain on the copper surface. Lower speeds may help reduce oxidation risks, while maintaining optimal feed rates prevents excessive heat buildup.
Speed and Feed Table:
Utilizing the right coolant is critical for minimizing corrosion. Water-soluble coolants can help wash away chips while cooling the part. Choosing a coolant with rust inhibitors specifically designed for non-ferrous metals ensures better protection against corrosion.
Coolant Selection Criteria:
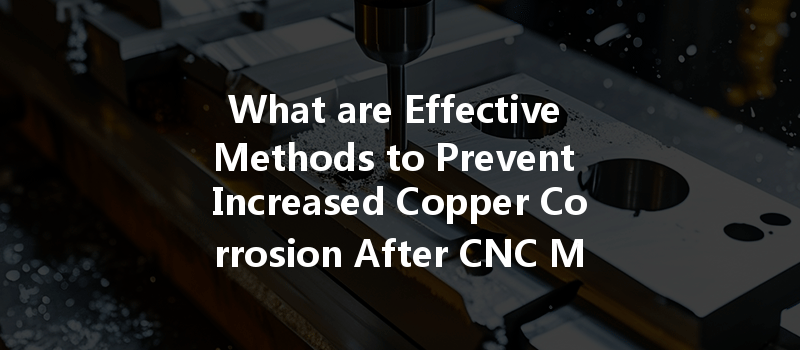
After machining, the immediate handling and cleansing of copper components can significantly reduce corrosion risks. Here’s how to approach post-machining care:
Applying protective coatings post-machining is ideal for enhancing corrosion resistance. Common options include:
Establishing a routine for inspecting copper components can aid early identification of potential corrosion issues. Implementing a maintenance schedule allows for:
Ensuring that staff is knowledgeable about machining copper and the risks related to corrosion can significantly improve outcomes. Training sessions should focus on:
Preventing increased copper corrosion during and after CNC machining is paramount to maintaining quality and durability in copper components. By understanding the factors that contribute to corrosion and actively implementing appropriate measures—such as choosing the right tools, employing suitable coolants, and providing proper care and storage—manufacturers can significantly reduce the likelihood of corrosion.
As industries continue to rely on copper for its excellent properties, ensuring its resilience against corrosion is more vital than ever. The preventative strategies discussed herein not only enhance the longevity of copper components but also contribute to overall efficiency within manufacturing processes.
The significance of addressing this issue cannot be overstated. In a world where precision and quality are non-negotiable, investing time and resources into preventing copper corrosion is an investment in excellence. Remember, each decision made in the CNC machining process impacts the end product—and in the case of copper, proactive steps today will result in significant benefits tomorrow.