As an expert in the CNC machining industry, I often get asked about how to handle high-hardness materials in precision machining. If you’ve ever worked with materials like hardened steel, titanium, or ceramics, you know that machining these materials is no small feat. It requires not just the right machinery, but also an understanding of the right techniques. Whether you’re doing CNC turning, CNC milling, or 5-axis machining, mastering the art of machining hard materials is crucial to ensure high precision and efficiency.
In this guide, I’ll walk you through the ins and outs of CNC machining for high-hardness materials. I’ll share my experience and tips that can make the process smoother and more successful. And if you’re someone who’s ever struggled with maintaining accuracy or facing tool wear issues, you’ll find this article particularly valuable.
Understanding High-Hardness Materials in CNC Machining
When we talk about high-hardness materials, we’re referring to materials that have been treated or are naturally harder and tougher than regular materials. These materials are often used in industries that demand durability, such as aerospace, automotive, medical devices, and defense. Some common high-hardness materials include:
- Hardened Steel: Steel that has been heat-treated to increase its hardness. This is widely used in manufacturing high-performance parts, such as gears and shafts.
- Titanium: Known for its high strength-to-weight ratio and resistance to corrosion. It’s a popular choice in the aerospace industry.
- Ceramics: Super hard and wear-resistant materials often used in medical devices and electronics.
- Tool Steels: Often used for making cutting tools and molds.
These materials are tough to machine because they tend to be abrasive, and they can quickly wear down cutting tools if not properly managed. But with the right CNC machining techniques, you can achieve excellent results.

The Challenges of Machining High-Hardness Materials
Before diving into the techniques, it’s essential to understand the challenges of machining hard materials. If you’re struggling with CNC turning or CNC milling on these materials, here are some common issues you might face:
1. Tool Wear
High-hardness materials can cause significant wear on tools. The abrasive nature of these materials means that even the toughest cutting tools can wear out quickly, leading to higher tool replacement costs and longer setup times.
2. Heat Generation
Machining hard materials generates a lot of heat, which can cause several problems:
- Thermal expansion: Heat can cause the material to expand, which can impact the precision of your cuts.
- Tool degradation: Excess heat can lead to rapid tool wear and even tool failure.
3. Surface Finish Quality
Achieving a smooth, high-quality surface finish on hard materials can be tricky. These materials tend to have more resistance to cutting, which can lead to rougher finishes if not properly managed.
4. Chip Removal
Hard materials generate tough chips that are difficult to remove. Improper chip removal can cause the chips to re-enter the cutting zone, leading to poor surface finishes and even damage to the workpiece or tooling.
CNC Machining Techniques for High-Hardness Materials
Now that we’ve covered some of the challenges, let’s explore the strategies and techniques that will help you navigate these hurdles when machining high-hardness materials.
1. Choosing the Right Tools
The key to successful CNC machining of hard materials lies in selecting the right tools. Here are a few considerations:
- Carbide Tools: Carbide tools are hard and heat-resistant, making them ideal for machining high-hardness materials. You should opt for carbide inserts that are specifically designed for hard materials.
- Cermet and Ceramic Tools: For extremely hard materials like ceramics or hardened steel, cermet (ceramic-metal composites) and ceramic cutting tools can perform better than carbide. They can withstand high temperatures and maintain sharpness longer.
- Coated Tools: Tool coatings such as TiN (Titanium Nitride) or TiAlN (Titanium Aluminum Nitride) can help reduce wear and increase tool life. These coatings are particularly useful when machining materials that are prone to high thermal loads.
2. Optimizing Cutting Parameters
Machining hard materials requires careful tuning of cutting parameters. These parameters will help you optimize efficiency while reducing tool wear.
- Lower Cutting Speeds: While it might be tempting to run at higher speeds to improve productivity, hard materials often benefit from lower cutting speeds. Slower speeds generate less heat, reducing tool wear and helping to maintain the dimensional accuracy of your parts.
- Increased Feed Rates: Using a higher feed rate can help in reducing heat buildup by taking deeper cuts with less force. However, it’s essential to balance this with the tool material and the desired surface finish.
- Depth of Cut: Shallow cuts are often more effective than deep cuts when machining hard materials. This technique reduces the load on the tool and minimizes the heat generated during cutting.
3. Coolant Use and Heat Management
Since heat is a major issue when machining high-hardness materials, managing it effectively is crucial. Here’s how you can approach this challenge:
- Flood Coolant: Using flood coolant can help to reduce temperatures, remove chips, and maintain a consistent cutting environment. In some cases, high-pressure coolant systems can also improve tool life and surface finish.
- Dry Machining: For certain materials, dry machining might be the better option. However, it requires special tools and setups to prevent heat build-up from becoming an issue.
- Chip Removal: High-pressure coolant systems can also help with chip removal, ensuring that chips don’t interfere with the cutting process.
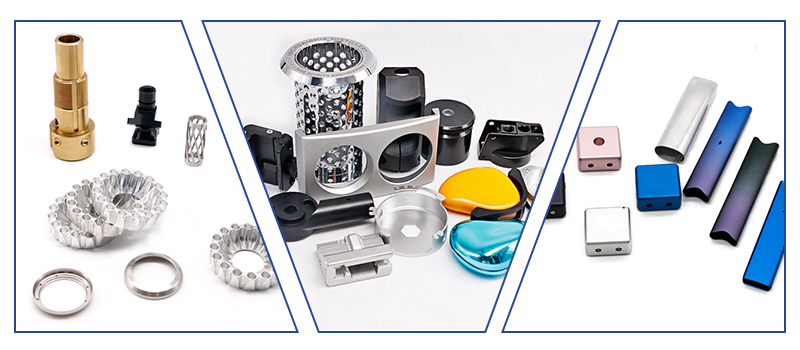
4. Advanced Machining Techniques
Incorporating advanced CNC machining techniques can make a significant difference when working with hard materials. Some of these techniques include:
- 5-Axis Machining: If you’re working with complex geometries or need to reduce the number of tool changes, 5-axis machining can be a game-changer. It allows for more precise cutting angles and can reduce tool wear by distributing cutting forces more evenly.
- High-Energy Milling: This technique involves applying rapid, high-force movements to the cutting tool to enhance material removal rates. It works well for materials that are tough to machine but can handle a little extra force.
- Laser-Assisted Machining: For very hard materials, using laser-assisted machining can help soften the material at the cutting point, making it easier to machine.
5. Minimizing Vibration
Vibration during machining, especially when using high-speed cutting tools, can lead to poor surface finishes and reduced tool life. Here are some ways to reduce vibration:
- Rigid Fixtures: Using rigid fixturing to hold the material firmly in place helps to minimize vibration during the cutting process.
- Damping Systems: Using damping systems in the machine tool or the cutting tool can absorb vibrations and improve stability.
- Toolpath Optimization: Proper toolpath planning can also reduce vibrations by ensuring that the cutting forces are evenly distributed.
Practical Tips for CNC Turning and Milling Hard Materials
If you’re specifically focusing on CNC turning or CNC milling, here are a few practical tips:
CNC Turning Tips:
- Use Slow Speeds and High Feed Rates: When turning high-hardness materials, using slower spindle speeds and higher feed rates can help avoid excessive heat and wear on the tools.
- Use a Single Cut per Pass: To avoid tool strain and ensure that the material is evenly removed, make a single, deep cut instead of multiple shallow cuts.
CNC Milling Tips:
- Climb Milling vs. Conventional Milling: When milling hard materials, climb milling is generally preferred over conventional milling. In climb milling, the cutter moves in the same direction as the material, which helps reduce cutting forces and improves surface finish.
- Use Smaller Tools for Detail: For intricate features and details, use smaller tools. They help maintain high precision and are less prone to damage from the hardness of the material.
Machining high-hardness materials doesn’t have to be a daunting task. With the right tools, parameters, and techniques, CNC machining can produce high-quality, precise parts even from the hardest materials. Whether you’re CNC turning, CNC milling, or using 5-axis machining, careful attention to detail can reduce tool wear, improve surface finishes, and ensure that your parts meet the required tolerances.
At YL-Machining, we specialize in precision CNC machining services for a wide range of hard materials. If you’re facing challenges with machining tough materials, don’t hesitate to reach out. We’re here to help you find the most effective solutions and ensure your project is a success!